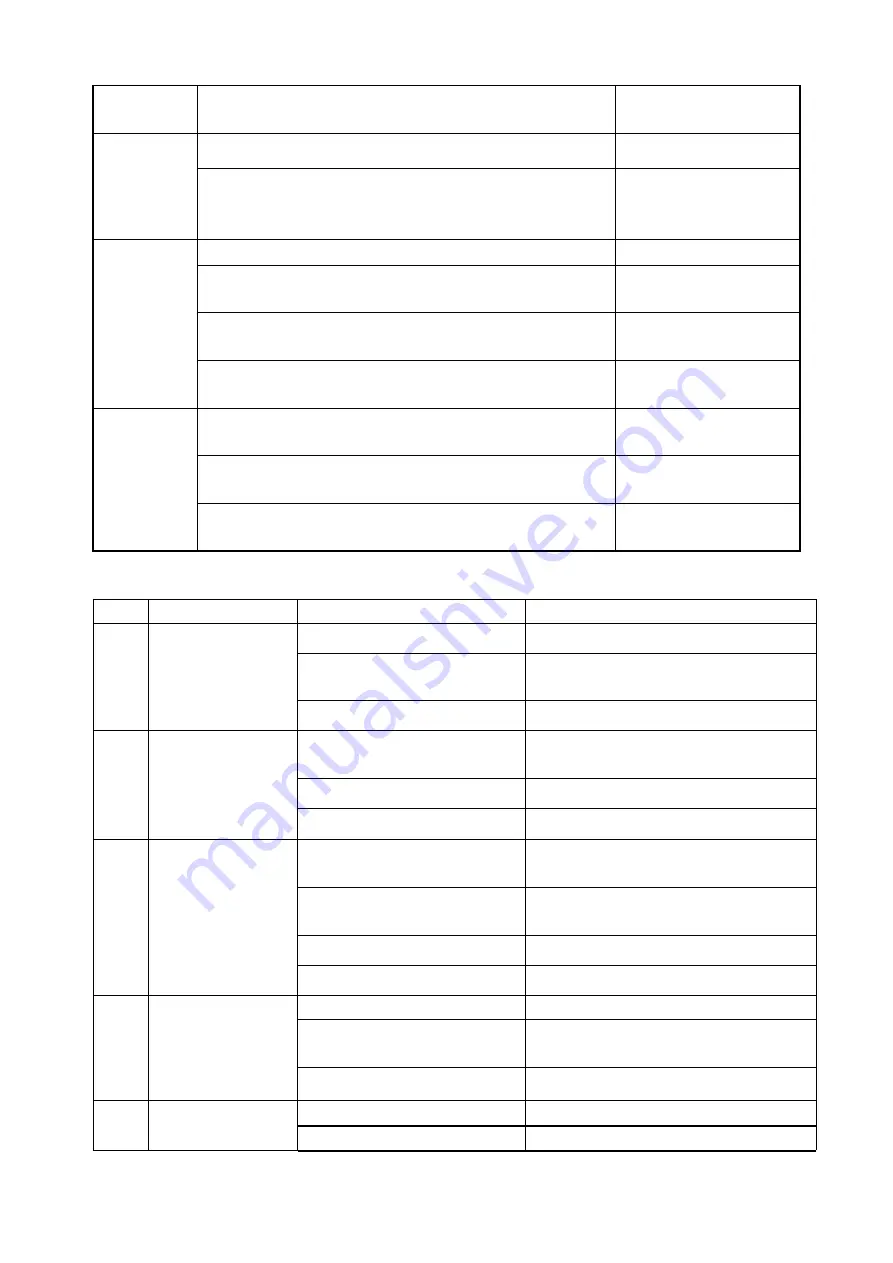
17
base plate groove is too deep
change
the
shallow
plate groove
Slag
Inclusion
the former molten slag of welding bead is not cleaned
remove molten slag
small current, too much weld slowly deposition, to much
swing during welding
increase
the
current
and reduce the swing
during welding
Big spatter
welding current and voltage doesn’t match
Adjust the welding data
There is too much oil, rust or water on wire or work-piece
clean the wire and work
piece
wire is streching too long outside the nozzle
press the torch closer to
work-piece
too big diameter of the nozzle
Change
to
suitable
nozzle
Penetration
is
not
enough
welding current is too small
Increase
welding
current
wire is streching too long outside the nozzle
press the torch closer to
work-piece
groove is not good
,
too small angle
,
too small gap
change
the
welding
technology process
* Common Failure of welding machines and solution
No.
Failure
Failure reason
Solution
F1
Fan is not turing
Fan is broken
Change the fan
Loose connection
Check where is the loss connection
and tighten it
other
Contact the seller
F2
Protection LED is
on
overheat
of
the
internal
machine
Wait till the temperature is coming
down and light is off
Thermal relay is broken
Change thermal relay
other
Contact the seller
F3
Current
and
voltage no display
Current and voltage display is
broken
Change the display
Loose connection
Check where is the loss connection
and tighten it
Main control board is broken
Change the main control board
Other
Contact the seller
F4
When press the
torch button, the
torch is not on
Torch switch is broken
Change the torch switch
Cable
connection
is
not
connected
Contact the cable
Control board is broken
Change or repair the control board
F5
No gas
Gas hose is blocked
Connect the gas
Gas hose is press
Check the gas flow