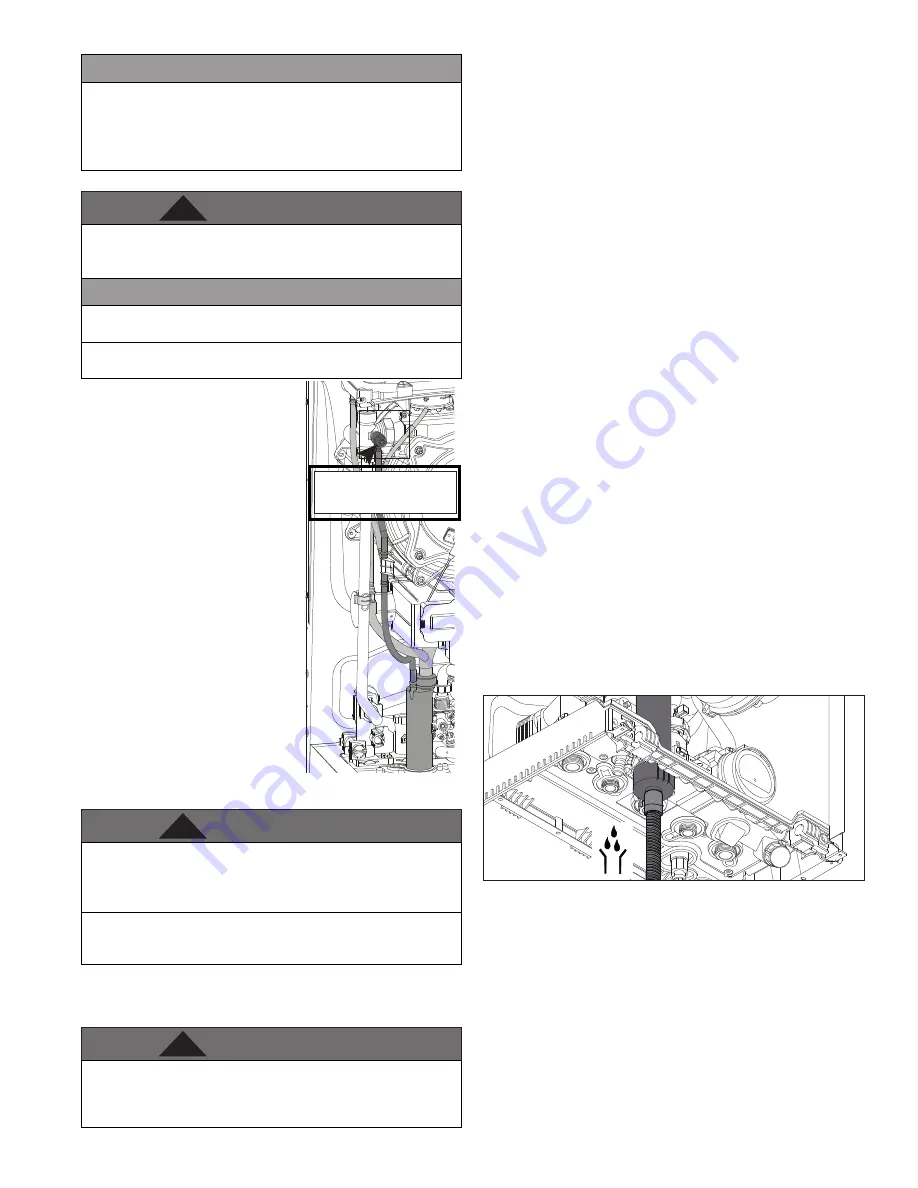
420010970304 - LP-700 Rev. 000 Rel. 002 Date 4.21.21
75
D. System Water Fill, Purge, and Test
WARNING
!
Ensure the boiler is full of water before firing the burner. Failure to do
so will damage the boiler. Such damage IS NOT covered by warranty,
and could result in property damage, severe personal injury, or death.
The boiler and heating system must
be thoroughly purged of air during
the initial installation or system
maintenance. Proceed as follows to
purge the boiler and heating system:
1. Open the manual air vent
positioned on the side of the primary
exchanger. The valve is already
connected to a discharge hose routed
to the condensate trap.
2. Lift the cap on the automatic air
release valve on the pump. Leave
open permanently.
3. Gradually open the main water
valve until water flows. Do not open
fully.
4. Thoroughly purge each zone
starting with the lowest point and
close them only when clear water free
of air is visible.
5. Close the manual air vent when
clear water free of air is visible.
6. Continue filling the system until at
least 12 psi registers on the pressure
gauge.
WARNING
!
Eliminate all system leaks. Continual fresh make-up water will
reduce boiler life. Minerals can build up in the heat exchanger,
reducing heat transfer, overheating the heat exchanger and
causing heat exchanger failure.
It is important to purge the system of air to avoid damage to the
boiler.
CAUTION
Connect the condensate discharge pipe before filling and purging
the heating circuit.
Figure 86 - Manual Air Vent
Position
Check if the condensate trap contains water. If not, it must be refilled.
Open the manual air vent on the main exchanger until completely
filled. Check the system pressure on the pressure gauge again.
F. Check Thermostat Circuit(s)
1. Disconnect the two external wires connected to the boiler
thermostat terminals TT1/TT2 (low voltage terminal strip).
2. Connect a voltmeter across these two incoming wires with power
supplied to the thermostat circuits. Close each thermostat, zone
valve and relay in the external circuit one at a time and check the
voltmeter reading across the incoming wires.
3. There should NEVER be a voltage reading.
4. If a voltage reading does occur under any condition, check and
correct the external wiring. (This is a common problem when using
3-wire zone valves.)
5. Once the external thermostat circuit wiring is checked and
corrected if necessary, reconnect the external thermostat circuit
wires to the boiler low voltage terminal strip. Allow the boiler to
cycle.
E. Purge Air from DHW System
WARNING
!
Ensure the boiler is full of water before firing the burner. Failure
to do so will damage the boiler. Such damage IS NOT covered by
warranty, and could result in property damage, severe personal
injury, or death.
1. Make sure the CH and DHW lines are open and full of water. Turn
on all electric power to boiler.
2. Open hot water faucets in the DHW system. Start with the faucets
nearest the boiler.
3. Keep faucets open until water runs freely and all air is purged. Then
move on to faucets further away from the boiler in the system.
4. When water flows freely from all hot water faucets, DHW purging
is complete.
G. Condensate Removal
1. The boiler is a high efficiency condensing appliance. Therefore,
the unit has a condensate drain. Condensate fluid is nothing more
than water vapor, derived from combustion products, similar to that
produced by an automobile when it is initially started.
Condensation is slightly acidic (typically with a pH of 3 to 5) and
must be piped with the correct materials. Never pipe the condensate
using steel, copper, brass or other materials that will be subject to
corrosion. Plastic PVC or CPVC pipe are the only approved materials.
A condensate neutralizer, if required by local authorities, can be made
up of lime crystals, marble or phosphate chips that will neutralize the
condensate. This may be done by the installer or you may purchase a
condensate neutralizer from HTP (7450P-212).
2. The boiler is equipped with a barbed outlet fitting, to which the
supplied hose must be installed and routed to a local drain. It is very
important that the condensate line is sloped downward away from
the boiler to a suitable indoor drain.
Figure 87 - Condensate Discharge
If the condensate outlet on the boiler is lower than the drain, you
must use a condensate removal pump, available from HTP (554200).
This pump is equipped with two leads that can be connected to
an alarm or another type of warning device to alert the user of a
condensate overflow, which, if not corrected, could cause property
damage.
3. If a long horizontal run is used, it may be necessary to create a vent
in the horizontal run to prevent a vacuum lock in the condensate
line.
4. Do not expose the condensate to freezing temperatures.
5. It is very important you support the condensation line to assure
proper drainage.
It is highly recommended to carefully follow the glycol manufacturer’s
recommended concentrations, expansion requirements, and
maintenance recommendations (pH additive breakdown, inhibitor
reduction, etc.) You must carefully calculate the additional friction
loss in the system as well as the reduction in heat transfer coefficients.
CAUTION
Boiler Manual Air
Vent