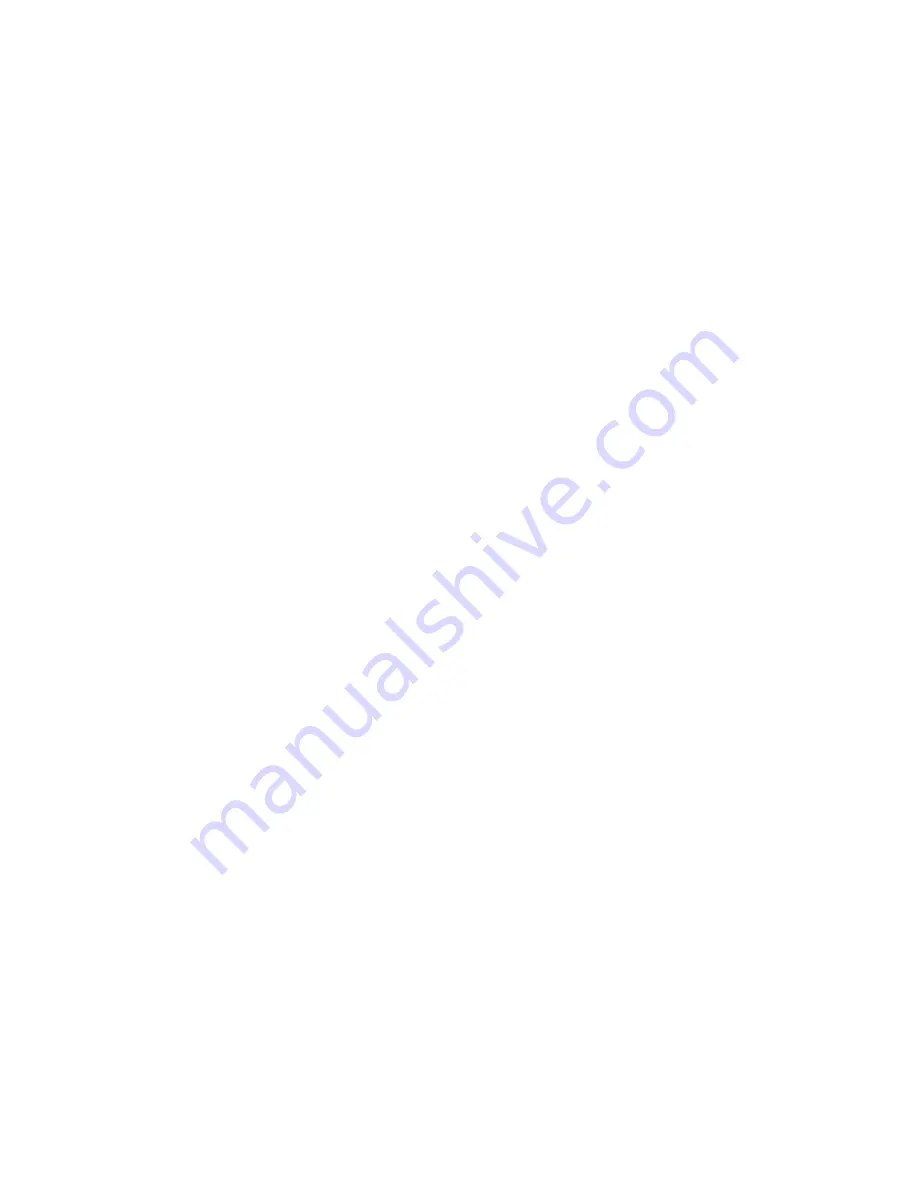
2-40 HP Portable Chillers
Chapter 2: Functional Description
13 of 78
Low Pressure Cutout
This electro-mechanical cutout device opens the compressor control circuit if refrigeration
system compressor suction pressure drops below 15 psi. It automatically resets when
refrigerant suction pressure reaches 30 psi.
Note:
The low pressure cutout is an automatic reset device typically mounted on the
compressor suction line inside the mechanical cabinet. Call a refrigeration
service technician to analyze the problem and reset the control.
Oil Pressure Safety Switch
This mechanical cutout device is installed on chillers built with semi-hermetic compressors
that have oil pumps. A differential pressure switch monitors the difference between crankcase
pressure and oil pump pressure.
If the pressure drops to an unsafe level for more than two minutes, the switch opens the
control wiring circuit, shutting off the compressor and turning the light on, but the pumps will
continue running.
Note:
The oil pressure safety switch is a manual reset device. Call a refrigeration
service technician to analyze the problem and reset the control.
Fan Cycling Switch
Air-cooled models only. 5 hp and 7.5 hp models have one fan. The fan cycling switch turns
on the fan when the discharge pressure in the condenser reaches 300 psi and turns it off when
the pressure drops below 190 psi.
10 hp to 30 hp models have two fans. One fan runs continuously every time the compressor
operates. The second fan turns on when the discharge pressure in the condenser reaches 275
psi and turns off when the pressure drops below 200 psi.
Pressure Switch
2 hp and 3 1/2 hp models have a pressure switch cutout device mounted in the process piping.
The switch shuts down the chiller if it senses that the water/glycol pressure through the
evaporator has dropped below an acceptable level. The pressure switch opens the control
circuit, shuts down the pumps, and shuts off the chiller.
Flow Switch
5 hp to 40 hp models only. The flow switch cutout device, mounted in the process piping,
shuts down the chiller if senses that the water/glycol flow rate through the evaporator has
dropped below an acceptable level. The flow switch opens the control circuit and shuts down
the pumps and the chiller.
Remote Start/Stop Interlock
An additional contact is provided to allow the remote starting or stopping of the chiller. To
use this feature, remove the jumper between terminals X1 and 1, and supply a switch or dry
contact interlock connected in series between these two terminals. Refer to the schematic
inside the control enclosure door.