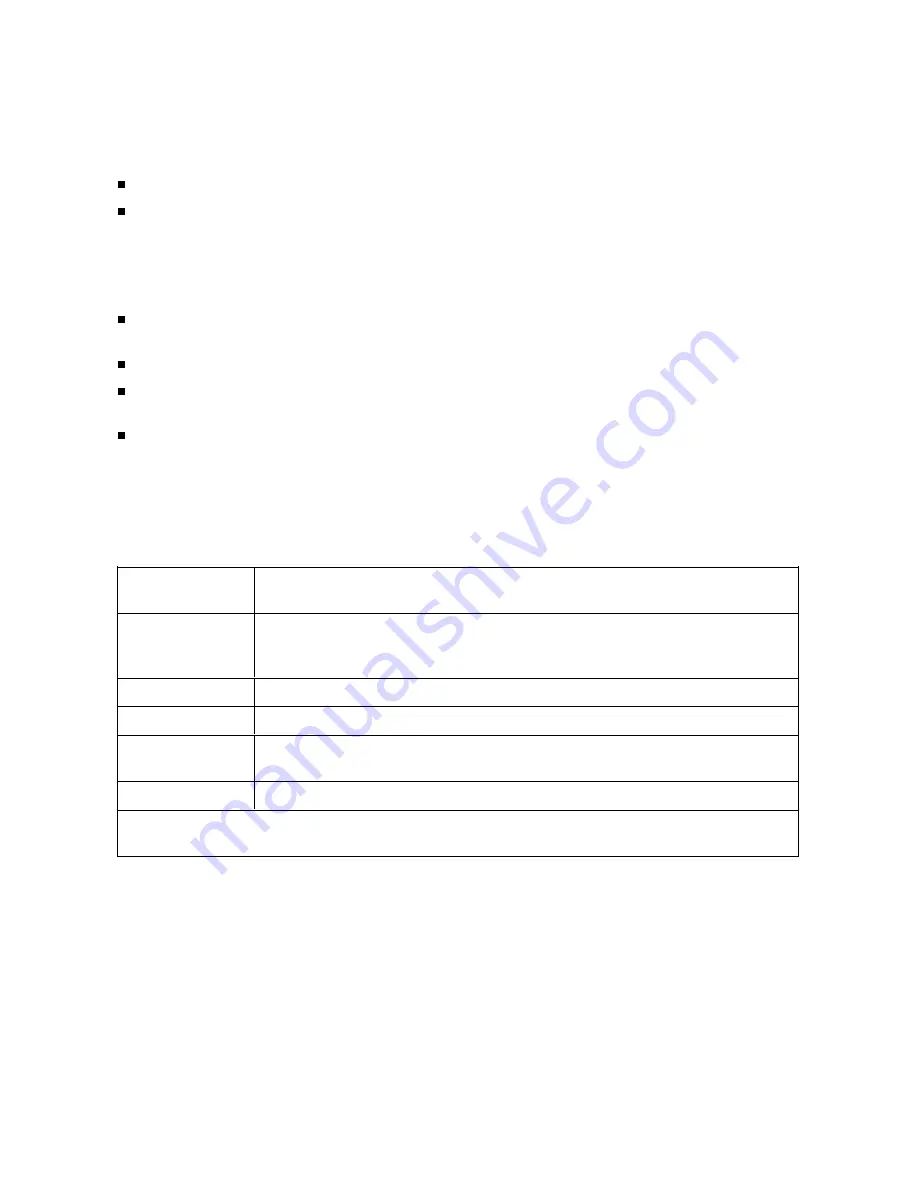
Preparing
a
Static-Safe
W
ork
Station
Reducing
ESD
Damage
T
o
help
reduce
the
amount
of
ESD
damage
that
occurs
during
testing
and
servicing
use
the
following
guidelines:
Be
sure
that
all
instruments
are
properly
earth-grounded
to
prevent
buildup
of
static
charge
.
P
ersonnel
should
be
grounded
with
a
resistor-isolated
wrist
strap
before
touching
the
center
pin
of
any
connector
and
before
removing
any
assembly
from
a
piece
of
equipment.
Use
a
resistor-isolated
wrist
strap
that
is
connected
to
the
HP
70000
Series
modular
spectrum
analyzer
system
mainframe's
chassis
.
If
you
do
not
have
a
resistor-isolated
wrist
strap
,
touch
the
chassis
frequently
to
equalize
any
static
charge
.
Before
connecting
any
coaxial
cable
to
an
instrument
connector
for
the
rst
time
each
day
,
momentarily
short
the
center
and
outer
conductors
of
the
cable
together
.
Handle
all
PC
board
assemblies
and
electronic
components
only
at
static-safe
work
stations
.
Store
or
transport
PC
board
assemblies
and
electronic
components
in
static-shielding
containers
.
PC
board
assembly
edge-connector
contacts
may
be
cleaned
by
using
a
lintfree
cloth
with
a
solution
of
80%
electronics-grade
isopropyl
alcohol
and
20%
deionized
water
.
This
procedure
should
be
performed
at
a
static-safe
work
station.
Static-Safe
ESD
A
ccessories
T
able
4-1.
Static-Safe
ESD
A
ccessories
HP
P
art
Number
Description
9300-0797
Set
includes:
3M
static
control
mat
0.6
m
2
1.2
m
(2
ft
2
4
ft)
and
4.6
m
(15
ft)
ground
wire
.
(The
wrist-strap
and
wrist-strap
cord
are
not
included.
They
must
be
ordered
separately
.)
9300-0865
Ground
wire
,
4.6
m
(15
ft)
9300-0980
Wrist-strap
cord
1.5
m
(5
ft)
9300-1367
Wrist-strap
,
color
black,
stainless
steel,
without
cord,
has
four
adjustable
links
and
a
7
mm
post-type
connection.
9300-1308
ESD
heel-strap
(reusable
6
to
12
months).
Order
the
above
by
calling
HP
DIRECT
at
(800)
538-8787
or
through
any
Hewlett-P
ackard
Sales
and
Service
Oce
.
T
roubleshooting
4-3
Summary of Contents for 70908A
Page 7: ...Servicing at a Glance vi ...
Page 19: ......
Page 44: ...Figure 2 1 Main Menu Softkeys Module Veri cation Software 2 19 ...
Page 45: ...Figure 2 2 Mass Storage Menu and Parameter Menu Softkeys 2 20 Module Veri cation Software ...
Page 47: ...Figure 2 4 Test Menu Softkeys 2 22 Module Veri cation Software ...
Page 55: ......
Page 61: ......
Page 94: ...Troubleshooting the A3 SYTFMD Figure 4 5 Discriminator Output Waveform Troubleshooting 4 33 ...
Page 125: ......
Page 139: ......
Page 205: ......
Page 209: ...Test 01 Flatness Figure 8 2 Equipment Setup for Test 01 Flatness 8 4 Module Veri cation Tests ...
Page 267: ......
Page 271: ...Front Panel Figure 9 2 Front Panel Removal Replacement 1 of 2 9 4 Replacing Major Assemblies ...
Page 272: ...Front Panel Figure 9 3 Front Panel Removal Replacement 2 of 2 Replacing Major Assemblies 9 5 ...
Page 274: ...Rear Panel Figure 9 4 Rear Panel Removal Replacement 1 or 2 Replacing Major Assemblies 9 7 ...
Page 275: ...Rear Panel Figure 9 5 Rear Panel Removal Replacement 2 or 2 9 8 Replacing Major Assemblies ...
Page 284: ...A3 SYTFMD Figure 9 10 A3 SYTFMD Removal Replacement Replacing Major Assemblies 9 17 ...
Page 294: ...A7 2nd Mixer Figure 9 17 A7 2nd Mixer Removal Replacement Replacing Major Assemblies 9 27 ...
Page 329: ......