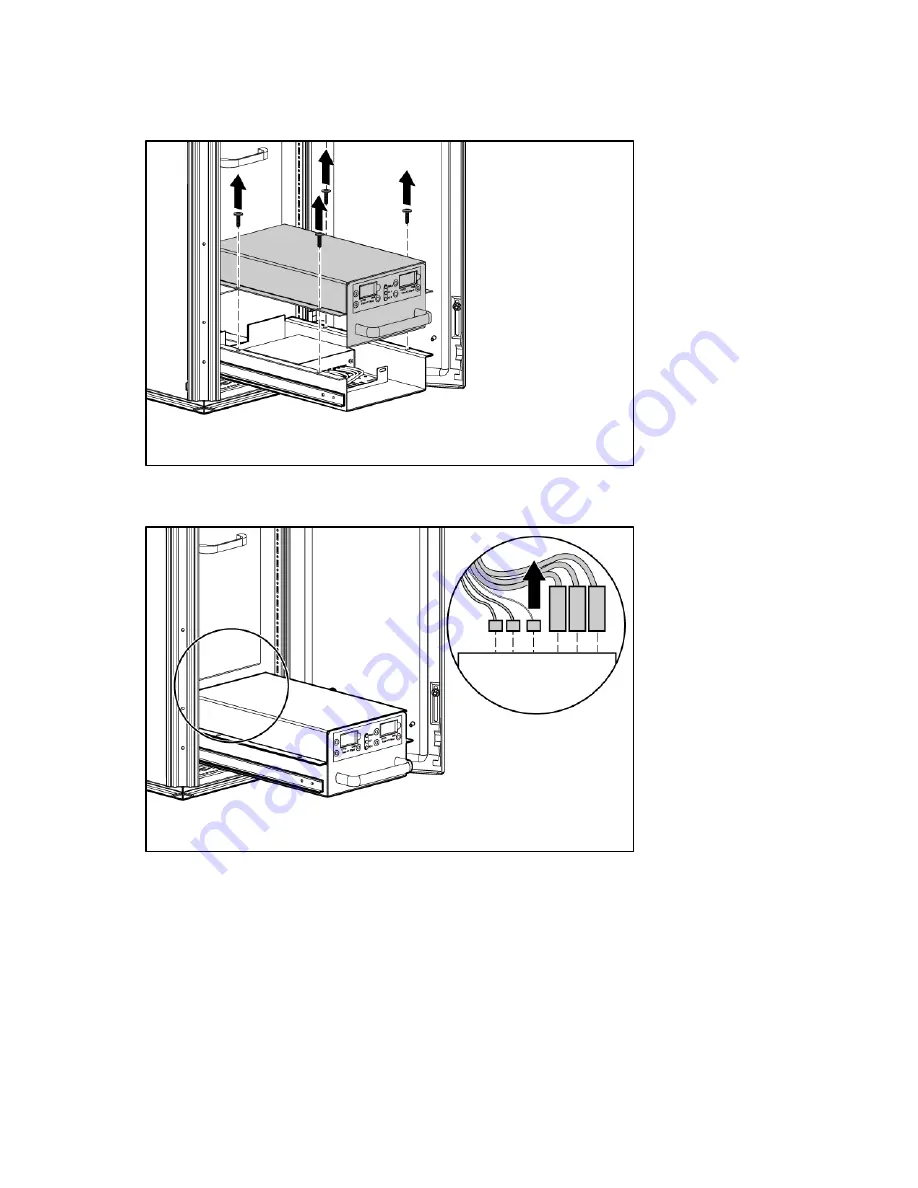
Removal and replacement procedures 27
4.
Using a T-25 Torx driver, remove the four Torx screws securing the AC transfer switch chassis to the
water group controller chassis. The transfer switch chassis cannot be completely removed yet
because the cables are still connected.
5.
Disconnect the green and yellow ground bonding wires from the water group controller.
6.
Disconnect the electrical power cables from the rear of the AC transfer switch.
Summary of Contents for 403349-003
Page 13: ...Customer self repair 13 ...
Page 14: ...Customer self repair 14 ...
Page 15: ...Customer self repair 15 ...
Page 16: ...Customer self repair 16 ...