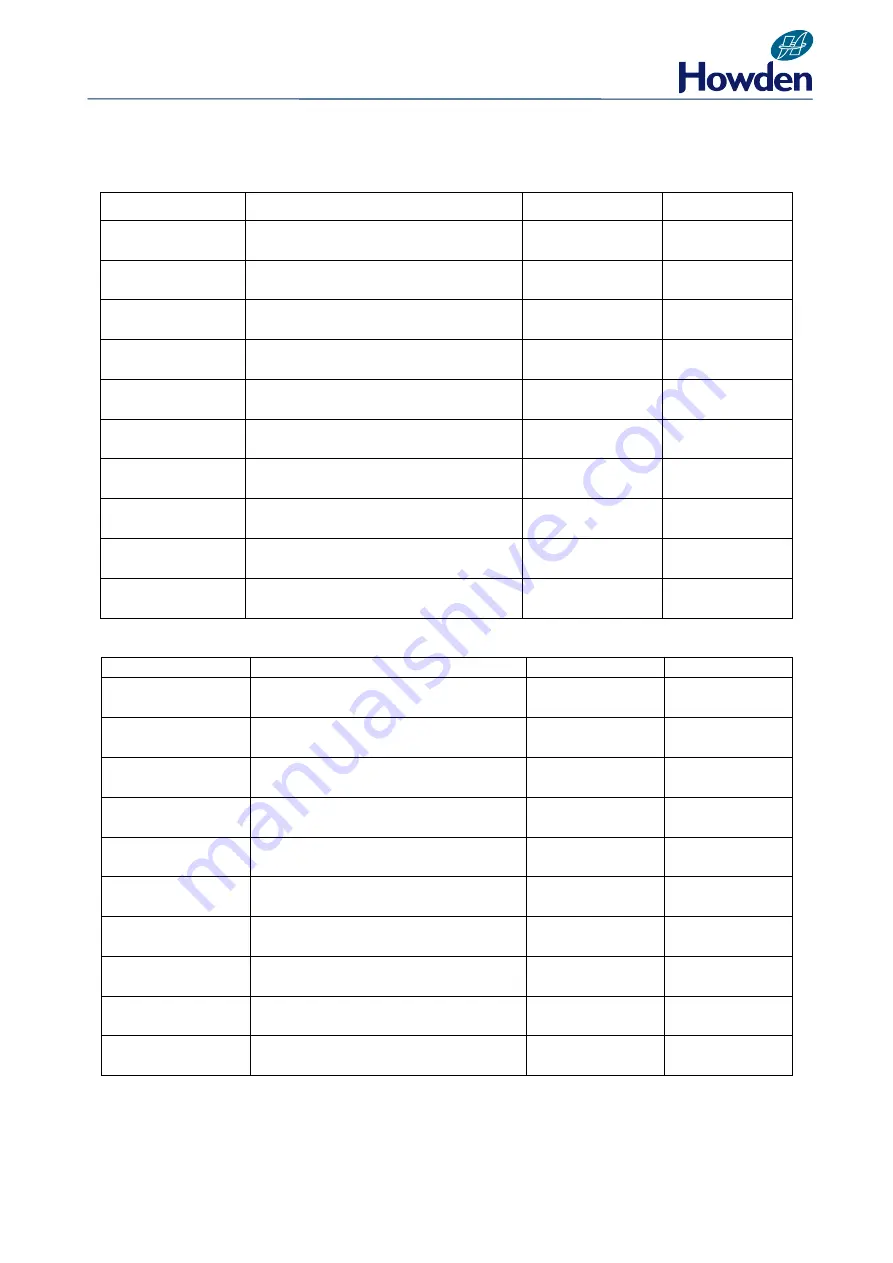
50
9.1
TORQUE SPECIFICATIONS
Fig.73 Torque Specifications for Fasteners on WRV163 compressors.
PART NUMBER
TYPE OF FASTENER
TORQUE lb ft
TORQUE Nm
R25055
40mm Locknut
Actuator Piston
206
150
G26019
¼” UNC x 5/8” Long Set Screw
Piston Seal Retaining Plate
4
5.5
M0216050
M12 x 60 Long Capscrew
Cylinder to outlet cover
37
50
M0313050
½” x 2” Long Set Screw
Inlet and Outlet Casings
40
55
R16154
Locknut M42
Slide Valve
165
225
G25062
½” x 1” Long Capscrew
Thrust Bearing Clamp Plate
10
14
G39007
50mm Locknut
Thrust Bearing Retaining Locknut
210
284
G25058
3/8” x 1” Long Capscrew
Rotor Cover Plates
18
25
G29012
M16 x 40mm Long Capscrew
Cylinder End Cover to Cylinder
88
120
G21015
5/8” x 2” Long Setscrew
Superfeed Flange
80
108
Fig.74 Torque Specifications for Fasteners on WRV204 compressors.
PART NUMBER
TYPE OF FASTENER
TORQUE lb ft
TORQUE Nm
R25055
40mm Locknut
Actuator Piston
150
206
G26019
¼” UNC x 5/8” Long Set Screw
Piston Seal Retaining Plate
4
5.5
M0216050
M12 x 60 Long Capscrew
Cylinder to outlet cover
37
50
M0316060
M16 x 60mm Long Set Screw
Inlet and Outlet Casings
88
120
R20313
36mm Locknut
Slide Valve
125
167
G29012
M16 x 40mm Long Capscrew
Thrust Bearing Clamp Plate
10
14
G27001
M12 x 40mm Long Setscrew
Bearing Retaining Plate
69
95
G29007
M10 x 30 Long Capscrew
Rotor Cover Plates
22
30
G29012
M16 x 40mm Long Capscrew
Cylinder End Cover to Cylinder
88
120
G21047
3/4” x 1-3/4” Long Setscrew
Superfeed Flange
140
190
Summary of Contents for WRV
Page 1: ...WRV WRVi COMPRESSOR RANGE SERVICE MANUAL...
Page 3: ...2 SECTION 1 FOREWORD...
Page 5: ...4 HOWDEN SECTION 2 DESCRIPTION...
Page 10: ...9 SECTION 3 INSTALLATION...
Page 14: ...13 SECTION 4 FIRST START UP...
Page 16: ...15 SECTION 5 NORMAL OPERATION...
Page 18: ...17 SECTION 6 PROCEDURES DURING SHUTDOWN...
Page 20: ...19 SECTION 7 MAINTENANCE...
Page 33: ...32 SECTION 8 OVERHAUL...
Page 50: ...49 SECTION 9 SPECIAL INSTRUCTIONS...
Page 57: ...56 SECTION 10 SPARES...
Page 64: ...63 Printed in the UK Issue HCL September 2012 Howden Compressors Limited...