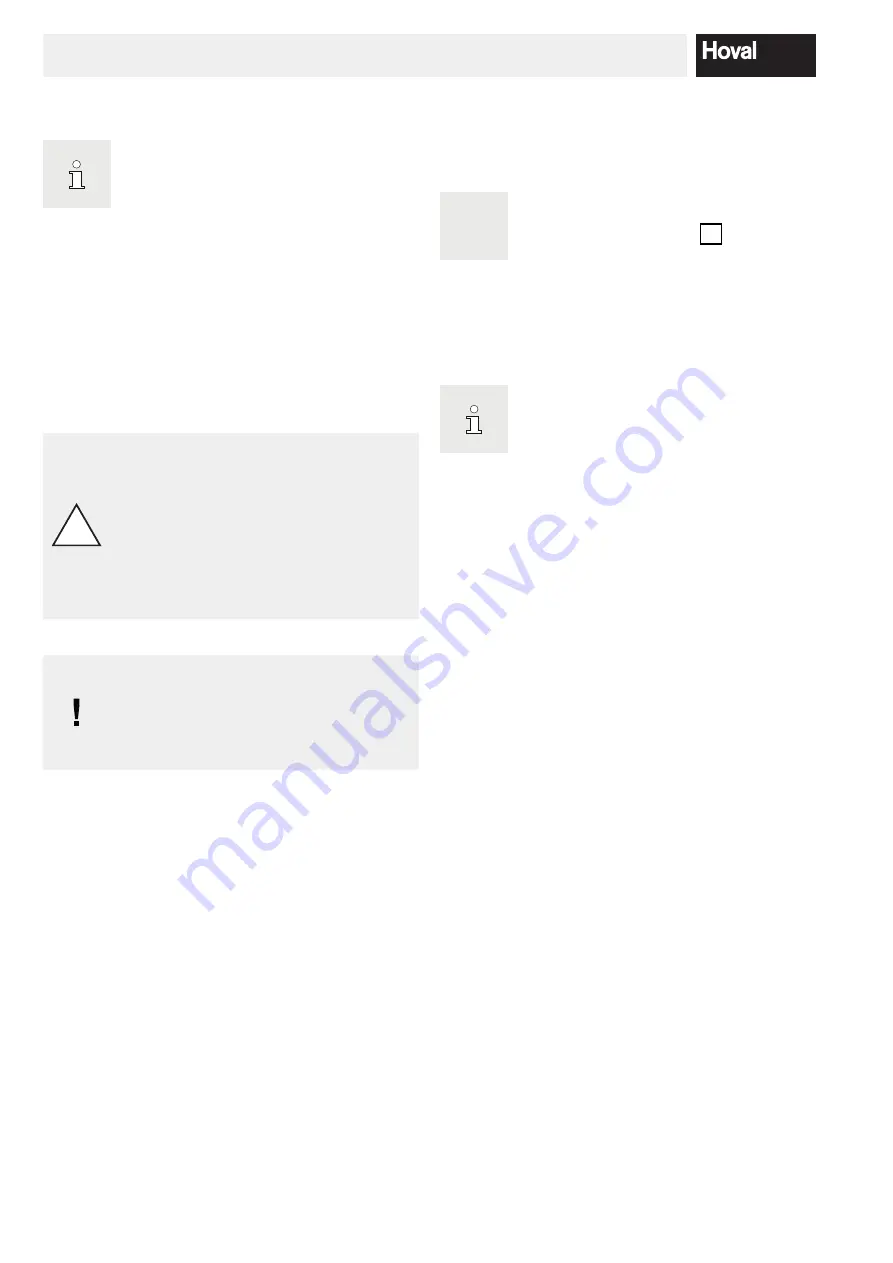
5.
Commissioning
•
After filling, always thoroughly bleed the
system and check the water circuit for leaks.
• Before commissioning, the condensate trap
or the neutraliser box must be filled with water.
•
When starting up the system for the first
time, the function of all safety and control
devices must be verified.
• The operation and maintenance of the sys-
tem must be explained to the user in detail.
•
The combustion air must be filtered if there
is a heavy build-up of building dust.
•
It is essential to check the gas flow pressure
and set the CO
2
value correctly.
5.1
Safety instructions
!
CAUTION
• Cutting injuries as a result of sharp edges.
• Handle parts of the casing carefully and
avoid contact with sharp edges!
• Risk of injury for non-expert personnel.
• Initial start-up, maintenance and cleaning
work are only allowed to be performed by
trained specialist personnel or by Hoval
customer service.
NOTICE
Damage to the system by filling unauthorised
liquids.
•
The filled water must be of drinking water
quality.
5.2
Filling the heating system
Filling of the heating system must be carried out by
trained personnel.
§
ÖNORM H5195, European Standard
EN 14868 and VDI Guideline 2035 must
be complied with (see point 4.3).
•
Open shut-off valves in the flow and return lines.
•
Connect the water hose to the filler tap.
•
Slowly fill the heating system.
• Observe the water level by means of a pressure gauge.
• Only use chemical additives for which the
chemicals supplier has confirmed their safe
-
ty and suitability.
• If frost protection agent is being used,
a separate engineering sheet is available
from Hoval.
34
4 217 215 / 00
COMMISSIONING
Summary of Contents for UltraGas 1000
Page 57: ...57 4 217 215 00...