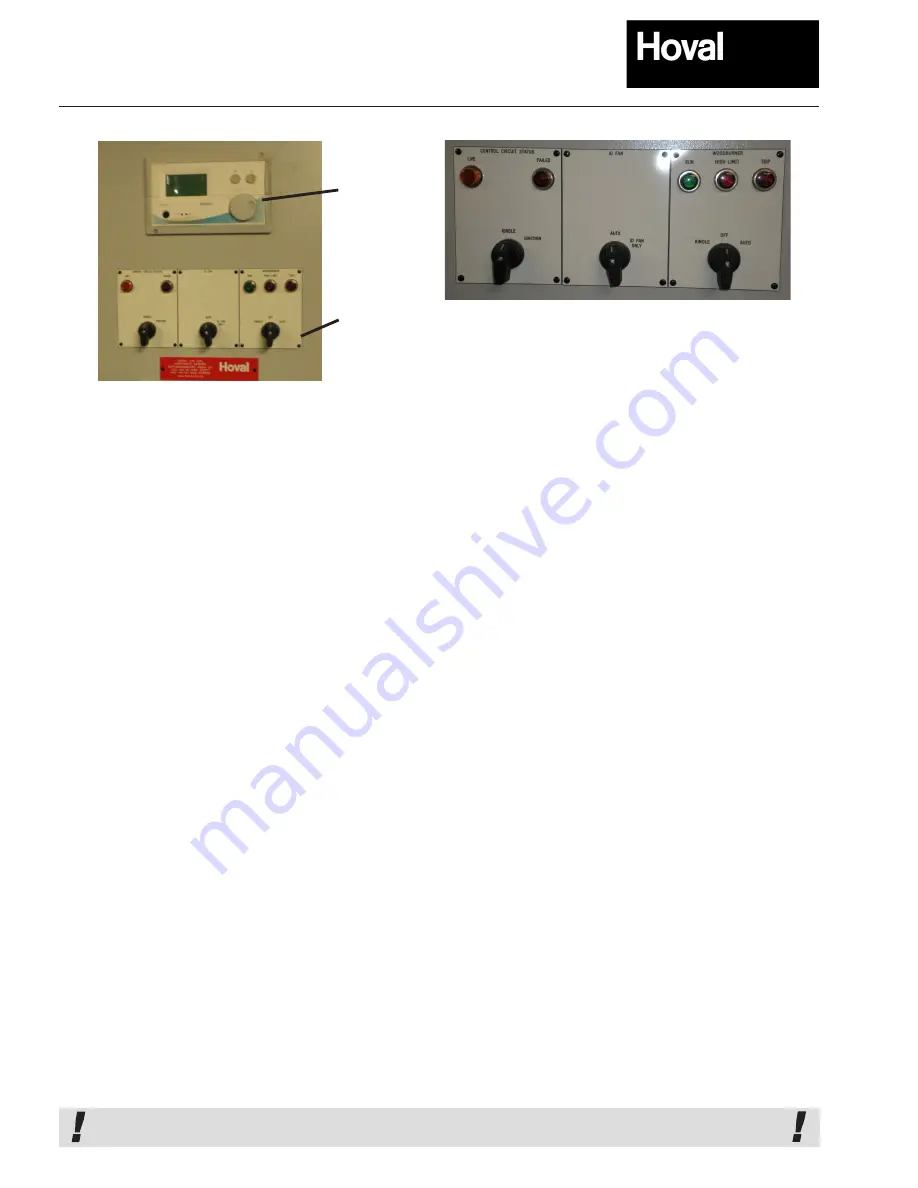
26
Hoval STU Wood Pellet Boiler
In addition to the stoker control panel (see below) a boiler flow temperature gauge is fitted at the front of the boiler.
Control Details and Safety Features
• The stoker control panel consists of:
•
Mains Isolator (not shown above)
•
LRP control unit and Display.
•
On/Off Switch with settings Kindle/Off/Auto.
•
ID Fan Switch with settings Auto/ID Fan Only
•
Optional Ignition switch with settings Kindle / Ignition
• The LRP controller and display
has a wide variety of settings
available for fine control of the wood pellet-burning stoker. In normal
operation only a few of these may be required to be displayed
but they can be altered at the time of commissioning to suit the
site conditions. The following are the most common parameters
available for display.
•
Boiler Flow set point.
•
Wood pellet feed speed.
•
Oxygen set point.
• The Mains Isolator will:
•
Electrically isolate the stoker and pick-up auger(s). The
isolator is provided with a lock-off facility.
• The stoker Kindle/Off/Auto switch will:
•
Turn the stoker off when in the off position.
•
In the Auto position the stoker will be under control of
the LRP and time clock or the Building Management
System and will modulate to follow the load accordingly
and may kindle if the set point water temperature is
satisfied (includes frost protection).
•
Kindle only, when in Kindle position (
Note
the boiler will
be held in a standby or kindle condition and there will
be no frost protection in this position).
• The Auto/ID Fan Only switch will:
•
Normally be in the Auto position.
•
I.D. Fan only position when the boiler door is opened.
• The Kindle/Ignition switch (where fitted) will:
•
Normally be in the kindle position.
•
In the Ignition position the retort will be primed (from
empty) with pellets and the ignition process started.
The operator must ensure that the retort is totally
emptied of pellets before starting the ignition process.
The Stoker Control Panel also houses a series of indicator lights
as follows:
•
Panel Live (Orange).
•
Fuse Failed (Red).
•
Stoker Run (Green).
•
High Limit (Red).
•
Trip (Red).
Under normal operation the LRP controller monitors and regulates
the boiler water temperature. In addition to this, mounted in a pocket
on top of the boiler are two thermostats. The first of these has a
temperature dial, which can be adjusted in the range of 70-83
o
C, this
effectively acts as a first limit stat, and if the boiler water temperature
exceeds the set temperature the stoker will shut off and will only re-
fire once the water temperature has fallen. It should be set higher
than the programmed water temperature setting in the LRP controller.
The second stat is set at commissioning, usually 11
o
C above the first,
and is a second or high limit stat. If the boiler temperature exceeds
this limit then the stoker will shut off and the High Limit indicator will
be illuminated. The stoker will not re-fire until this second limit stat
is manually reset.
Under normal operation the Stoker Run (green) light should show
on the control panel.
A fuse Fail or a motor Trip would illuminate the appropriate light - if
illuminated the cause should be investigated prior to resetting.
The stoker control panel can be fitted or mounted on either side
of the boiler or where requested can be supplied separately for
mounting on a wall within the plant room. Site wiring will be re-
quired to connect the pellet auger feed motors, FD and ID fan
motors, each must be connected via individual isolating switches
that should be clearly labelled. In addition the flow temperature
sensor, damper control on both FD and ID fans, burn back stat,
combustion chamber pressure switch and lambda control will also
require wiring back to the panel. This wiring is NOT generally part
of the stoker installation unless arranged at the time of order.
IMPORTANT - A 3 Phase 32A 400V supply is required for stoker and control panel operation.
LRP Controller
and Display
Screen
Selector
Switches