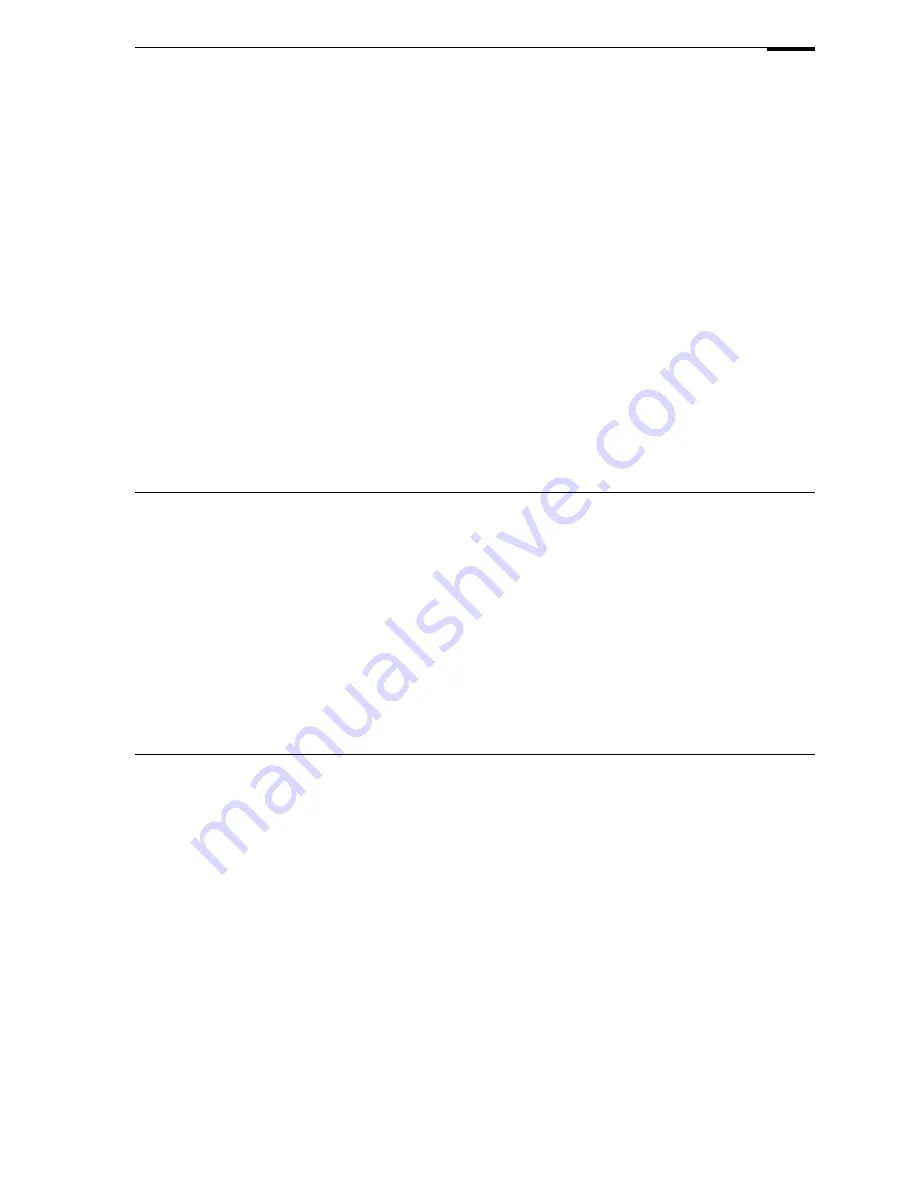
9
Space requirements, boiler plant house noise levels
Space Requirements
Where ever possible space should be left around the boiler to enable all parts to be examined and
the cubicle casings to be fitted or removed easily.
Clearances
a)
Back clearance is required for the system water, flue connections and access to cleaning door.
b)
Front clearance is required to swivel the boiler door ncluding burner by 90
o
, (standard to the
right optional to left) Space requirements to right when right hinged 80mm (plus burner length).
Clearance is equal to approximately the length of the boiler base (D) should be allowed for tube
cleaning and tube repairs. Shorter clearances are possible subject to cleaning methods and
plantroom layout.
c)
When the boiler is gas fired, allowance must be made for bringing the gas piping up to the
boiler front and to leaving space for the gas pipework at he side of the boiler or in the most suitable
direction
e)
It is possible to install two boilers without intermediate space. (Important boiler door on left boiler
must be swivelled to the left and boiler door on the right boiler to the right).
Additional points
When pipework is being connected to the boiler, care must be taken not to damage the casings,
which are not designed to be stood on.
External weight or thrust from system pipework attached to the boiler should be avoided by careful
design of pipework runs and the use of expansion joints as required
.
Measures can be adopted to reduce noise levels if it
is considered that any of the following sources will be
objectionable:
1) Direct transmission through the building structure,
e.g. rooftop boilerhouses causing vibration and
sound to be transmitted to the space below.
2) Sound transmission through the boilerhouse fabric
e.g. dwellings very close to the boilerhouse may be
subject to objectionable noise from a building,
without sound insulation, through the walls and air
ventilation openings.
3) From the chimney outlet e.g. where dwellings are
located very close by the boilerhouse or above the
chimney outlet. Natural gas fired plant has low
frequency sound pressure levels which are
disturbing to nearby residents when the boilers are
operating, particularly at night.
The following are sound and vibration control measures
which can be taken in respect of the points raised
above:
• Acoustic burner and booster shrouds
• Acoustic air intake baffle or acoustic louvres.
• Heavy construction or sound insulated external
walls, double glazing, heavy and close fitting doors
to the boilerhouse.
• Heavy construction flue with insulated cavity all
round when the flue rises within the occupied areas
of the building. Double skin insulated flues for flues
installed outside the building.
• Flue noise attenuator.
• Anti-vibration mounts for the boiler case.
• Peripheral gaps around pipes to be sealed with
suitable acoustic material.
• Anti-vibration connections to pipework and pumps.
• Heavy construction of suspended floor or ceiling.
Boiler Plant Noise Levels
Changing the door hinged side
The boiler door is substantially hinged to carry the full burner weight but no extra weight should be imposed.
1.
Open the door as hinged and screw on two spare locknuts on the door hinge bolts to locate
the door bosses on the new side.
2.
Close the door. Adjust the locknuts temperorarily and replace one door nut tightly.
3.
Change the other nut over with its plain diagonal counterpart from the other side of the door
and tighten both.
4.
Adjust the locknuts so that a seal is obtained all round the fibre joint.
5.
Open the door and remove the original locknuts.
Important
•
Always have two nuts tightened to prevent the door falling.
•
It is essential that the door seal is in place correctly after closing the door every time.
Replace the joint if in doubt and check there are no fumes escaping.
This is a specialist subject and where noise due to vibration, combustion or mechanical sources is
likely to be a problem, Hoval should be advised.
August 2014