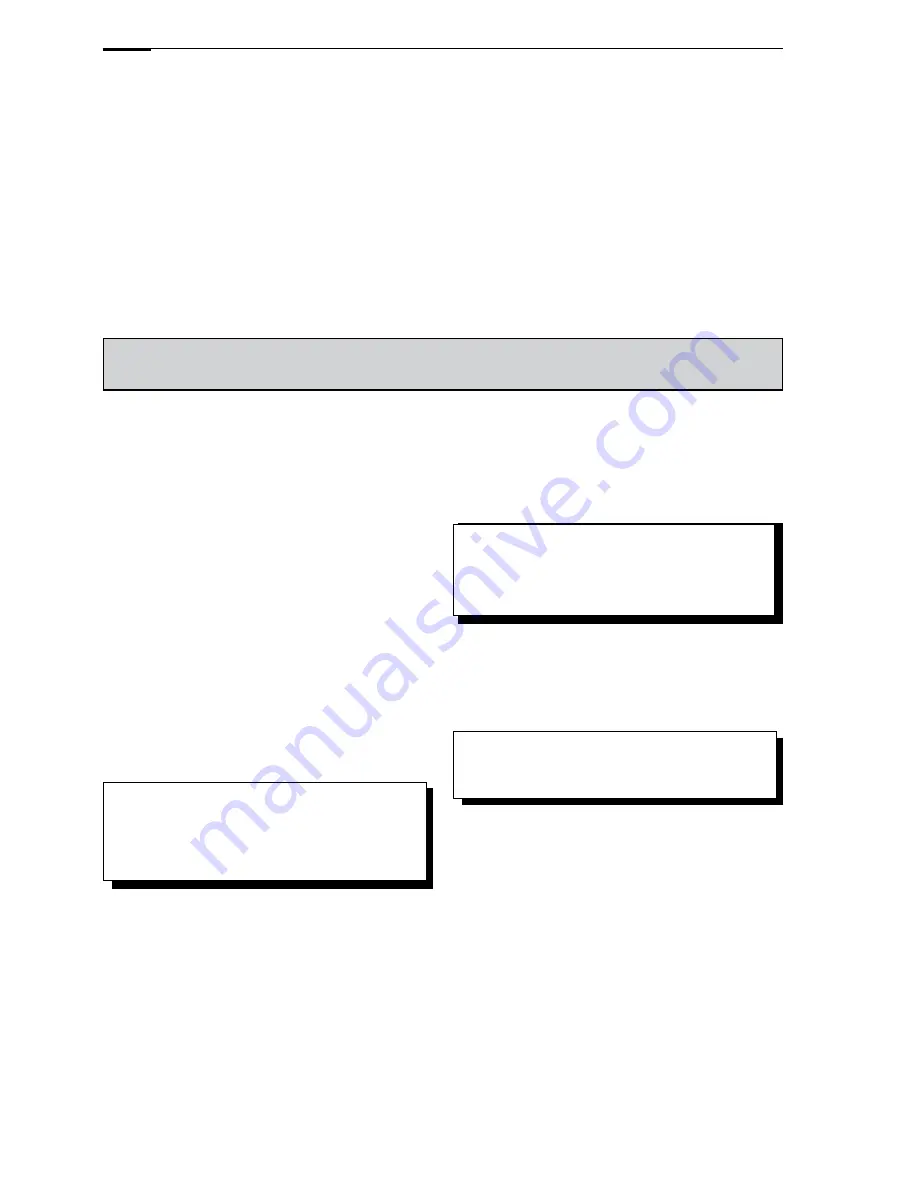
20
Boiler & Burner Servicing
In addition to the periodic inspections given on page 19 it is recommended that a complete check is carried
out on all components at appropriate intervals.
These checks must be made by a qualified boiler/burner service engineer, ideally under an annual sevice and
maintenance contract.
Hoval Service Department normally provides this service and will be pleased to provide a written quotation on
request. This would typically cover the operation, cleanliness, combustion efficiency etc., of the fuel burner
and associated controls. In the case of gas burners it would include a check on the gas tightness of the gas
control valves at the burner if a gas leak detection unit is not fitted. In addition if a gas booster is fitted it
could also be covered in this service.
Please note No adjustment of internal components is permissible on either gas
or oil burners except by a qualified service/burner engineer.
If flexible pipes are used for connecting the gas burner make a monthly leak test on these pipes.
Maintenance - Boiler & Burner Servicing
Boiler Cleaning for Heating Surface
Frequency of cleaning will be dependent on usage in conjunction with the condition of the boiler at the periodic
inspections, but the minimum requirements when using the various fuels are:-
1) Run the boiler until the burner automatically switches
off under action of the control thermostat. (It is
easier to clean a warm boiler).
2) Switch OFF electrical supply to the burner. Where
a plug connection is fitted in the cable from the boiler
to the burner, disconnect at this point. Switch OFF
electrical supply to the booster.
3) Turn OFF all fuel shut-off valves at the burner.
4) Where rigid fuel pipes to burner are employed,
e.g. gas burners, disconnect pipe(s) to allow the
boiler door to open.
5) Fully open the boiler door complete with burner.
6) Clean the tubes using the supplied brush. Similarly
clean the combustion chamber when required. Avoid
damage to the ceramic sealing strip against which
the door closes.
NB remove spirals if fitted.
7) Remove rear cleaning/explosion door. Clear loose
soot from the smoke outlet box and thoroughly clean
the box. Clean and examine the boiler backplate;
no hard deposit should be present. Remove any
build up occuring between the projecting tube ends.
8) Refit spirals if originally fitted.
(9) Check conditions of cleaning/explosion door gasket.
Refit door, ensuring it seats correctly on the gasket
tighten the wing nuts only two full turns against
spring compression.
Gas (natural or LPG) - once per heating seaon
Oil BS Class D (35 sec) - twice per heating season
Oil heavy grades - 3 to 4 times per heating season
NOTE: Lengthy periods between cleaning
should only be resorted to when the
periodic inspections prove this is possible.
NOTE: Where any hard scaling is present,
use a propietary cleaning medium
to soften and assist removal.
NOTE: Where heavy oil is being used
on a circulatory fuel system,
ensure that fuel pump(s) heaters
and tracers are left in operation at
all times.
August 2014