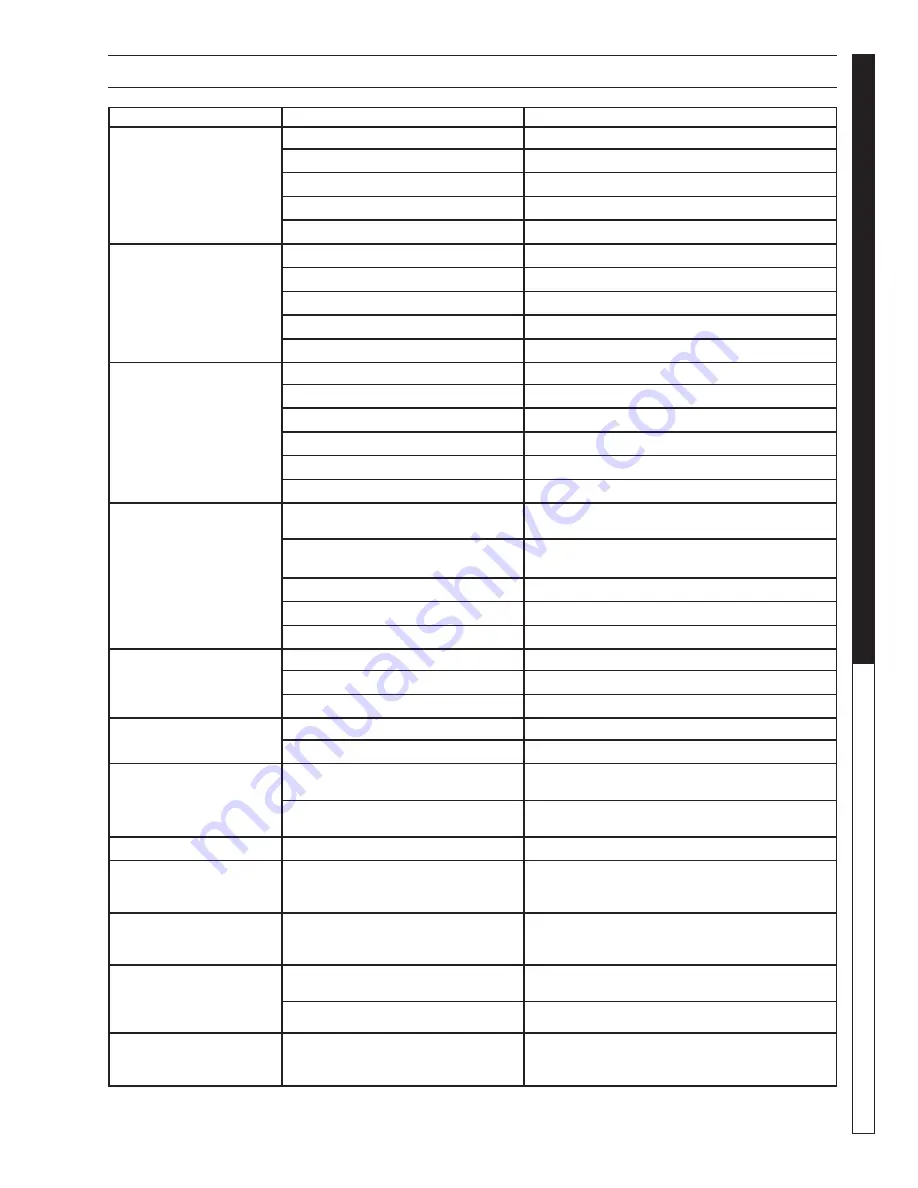
Hotsy EP • 8.914-444.0 • Rev. 07/13
11
PRESSURE
W
ASHER
T
roub
leshooting Guide
TROUBLESHOOTING
PROBLEM
POSSIBLE CAUSE
SOLUTION
PUMP RUNNING
NORMALLY BUT
PRESSURE LOW ON
INSTALLATION
Pump sucking air
Check water supply and possibility of air seepage.
Check valves sticking
Check and clean or replace if necessary.
Unloader valve seat faulty
Check and replace if necessary.
Nozzle incorrectly sized
Check and replace if necessary.
Worn piston packing
Check and replace if necessary.
FLUCTUATING
PRESSURE
Valves worn
Check and replace if necessary.
Blockage in valve
Check and replace if necessary.
Pump sucking air
Check water supply connections.
Worn piston packing
Check and replace if necessary.
Insuffi cient water
Check fi lter and hose for breakage.
PRESSURE LOW AFTER
PERIOD OF NORMAL
USE
Nozzle worn
Check and replace if necessary.
Suction or delivery valves worn
Check and replace if necessary.
Suction or delivery lines blocked
Check and clean if necessary.
Unloader valve seat worn
Check and replace if necessary.
Worn piston packing
Check and replace if necessary.
Water temperature excessive
Reduce to below 160
o
F.
PUMP NOISY
Air in suction line
Check water supply and connections on suction
line.
Broken or weak suction or delivery
valve spring
Check and replace if necessary.
Foreign matter in valves
Check and clean if necessary.
Worn bearings
Check and replace if necessary.
Excessive temperature of water
Reduce to below 160
o
F.
PRESENCE OF WATER
IN PUMP OIL
Oil seal worn
Check and replace if necessary.
High humidity in air
Check and replace if necessary.
Piston packing worn
Check and replace if necessary.
WATER DRIPPING FROM
UNDER PUMP
Piston packing worn
Check and replace if necessary.
O-ring plunger retainer worn
Check and replace if necessary.
WATER DRIPPING FROM
PUMP PROTECTOR
Water supply pressure too high (over
90 PSI)
Lower water supply pressure using a regulator.
Spray gun is in the off position for over
5 minutes
Turn machine off if not in use for over 1-2 minutes.
OIL DRIPPING
Oil seal worn
Check and replace if necessary.
EXCESSIVE VIBRATION
IN HIGH PRESSURE
HOSE
Irregular functioning of the pump
valves
Check and replace if necessary.
MOTOR DOES NOT
START WHEN SWITCHED
ON
Plug not well connected or lack of
power supply
Check plug, cable and switch.
WHEN SWITCHING ON
THE MACHINE, MOTOR
HUMS BUT DOES NOT
RUN
Main voltage is insuffi cient, lower than
the minimum required
Check to make sure main power supply is ad-
equate.
The pump is stuck or frozen
Check by turning the motor manually.
MOTOR STOPS
Tripped thermal overload due to over-
heating
Check that main voltage corresponds to the speci-
fi cations. Wait a few minutes before turning on the
machine again by resetting the GFCI cord.