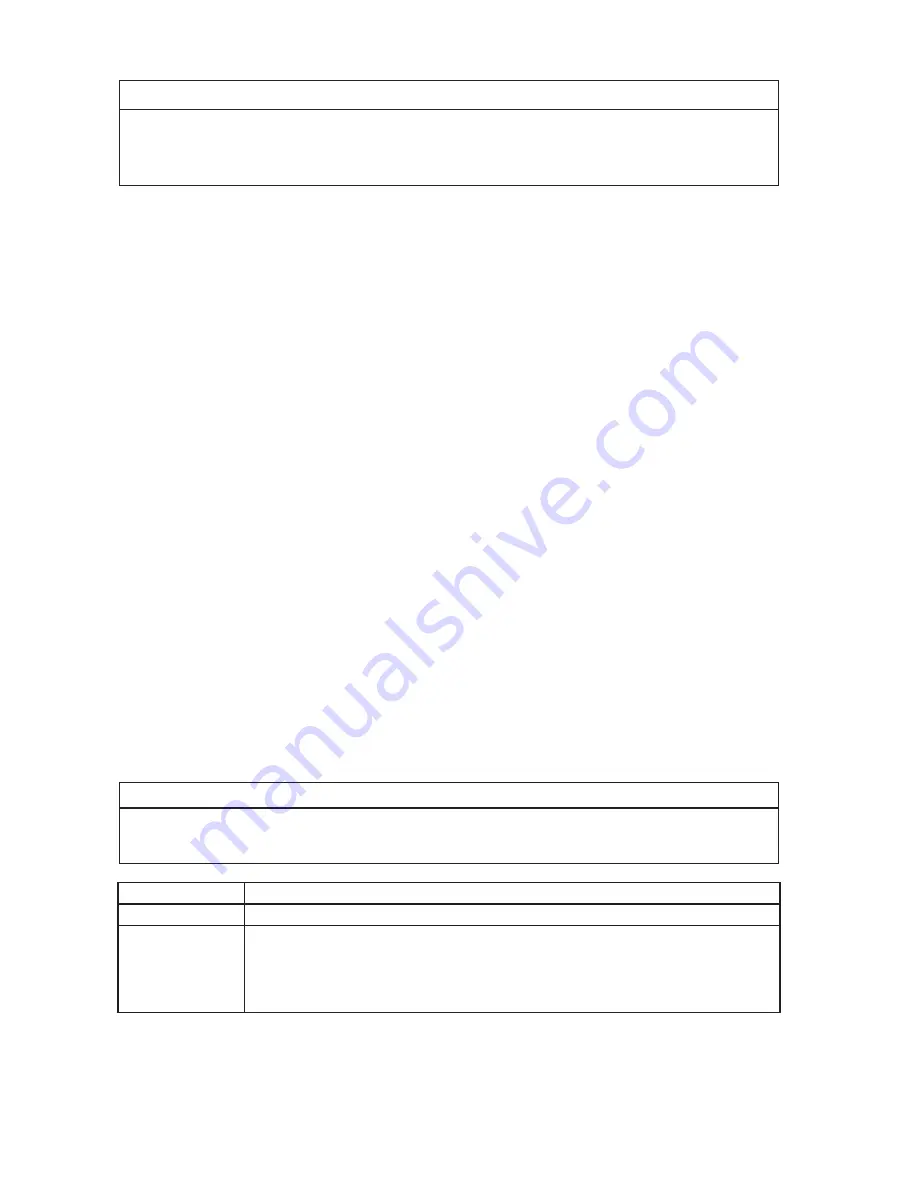
42
IMPORTANT
The vacuum level and vacuum pump may be the same as those for current
refrigerants. However, the rubber hose and gauge manifold to be used for
evacuation and refrigerant charge should be exclusively for POE oils.
2) Turn on the vacuum pump. Open the gauge manifold valves. Never allow the oil in
the vacuum pump to flow backwards.
3) Allow the vacuum pump to pull down to a 29.9” Hg vacuum. Evacuating period
depends on pump capacity.
4) Close the low-side valve and high-side valve on the gauge manifold.
5) Disconnect the gauge manifold hose from the vacuum pump and attach it to
a refrigerant service cylinder. Remember to loosen the connection and purge
the air from the hose. For the required refrigerant charge, see the nameplate.
Hoshizaki recommends only virgin refrigerant or reclaimed refrigerant which meets
AHRI Standard 700 (latest edition) be used.
6) A liquid charge is required when charging an R-404A system (to prevent
fractionation). Place the service cylinder on the scales; if the service cylinder is not
equipped with a dip tube, invert the service cylinder, then place it on the scales.
Open the high-side valve on the gauge manifold.
7) Allow the system to charge with liquid until the proper charge weight is met.
8) If necessary, add any remaining charge to the system through the low-side.
NOTICE!
To prevent compressor damage, use a throttling valve or liquid
dispensing device to add the remaining liquid charge through the low-side
access valve with the appliance running.
9) Close the gauge manifold valves, then disconnect the gauge manifold hoses.
10) Cap the access valves to prevent a possible leak.
B. Component Service Information
NOTICE
When replacing a component listed below, see the notes to help ensure proper
operation.
Component
Notes
Compressor
Install a new start capacitor and start relay (if applicable).
Thermostatic
Expansion Valve
• Attach the thermostatic expansion valve bulb to the suction line in the same
location as the previous bulb.
• The bulb should be between the 10 and 2 o'clock positions on the tube.
• Secure the bulb with the clamp and holder, then insulate it.
Summary of Contents for KM-300BAJ
Page 57: ...56 C Wiring Diagram ...