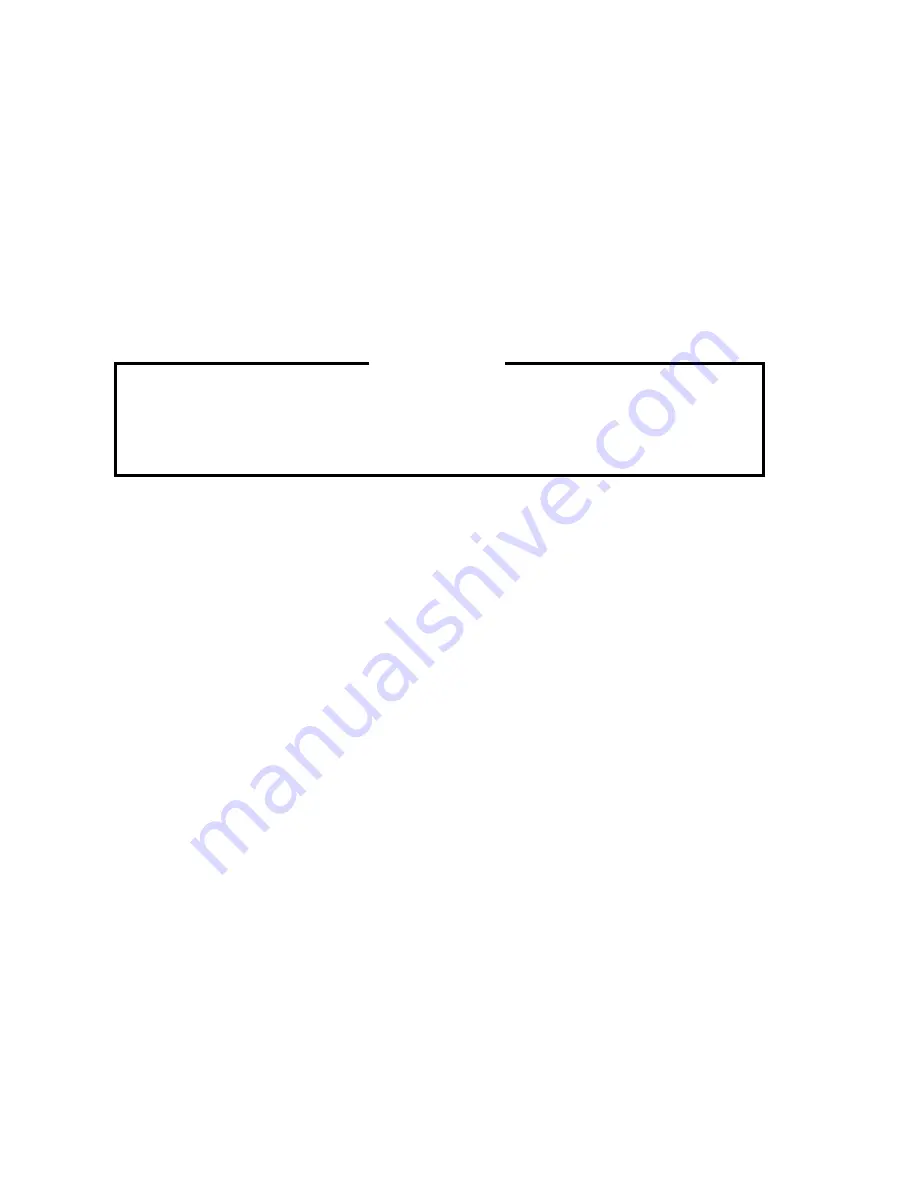
36
15) Evacuate the system, and charge it with refrigerant. See the Nameplate for the
required refrigerant charge.
16) Connect the Terminals, and replace the Terminal Cover in its correct position.
17) Replace the panels in their correct positions.
18) Turn on the power supply.
4. REMOVAL AND REPLACEMENT OF DRIER
IMPORTANT
Always install a new Drier every time the sealed refrigeration system is
opened. Do not replace the Drier until after all other repair or replacement
has been made.
1) Turn off the power supply.
2) Remove the panels.
3) Recover the refrigerant and store it in an approved container.
4) Remove the Drier.
5) Install the new Drier, with the arrow on the Drier, in the direction of the refrigerant flow.
Use nitrogen gas at the pressure of 3-4 PSIG when brazing the tubings.
6) Check for leaks using nitrogen gas (140 PSIG) and soap bubbles.
7) Evacuate the system, and charge it with refrigerant. See the Nameplate for the required
refrigerant charge.
8) Replace the panels in their correct positions.
9) Turn on the power supply.