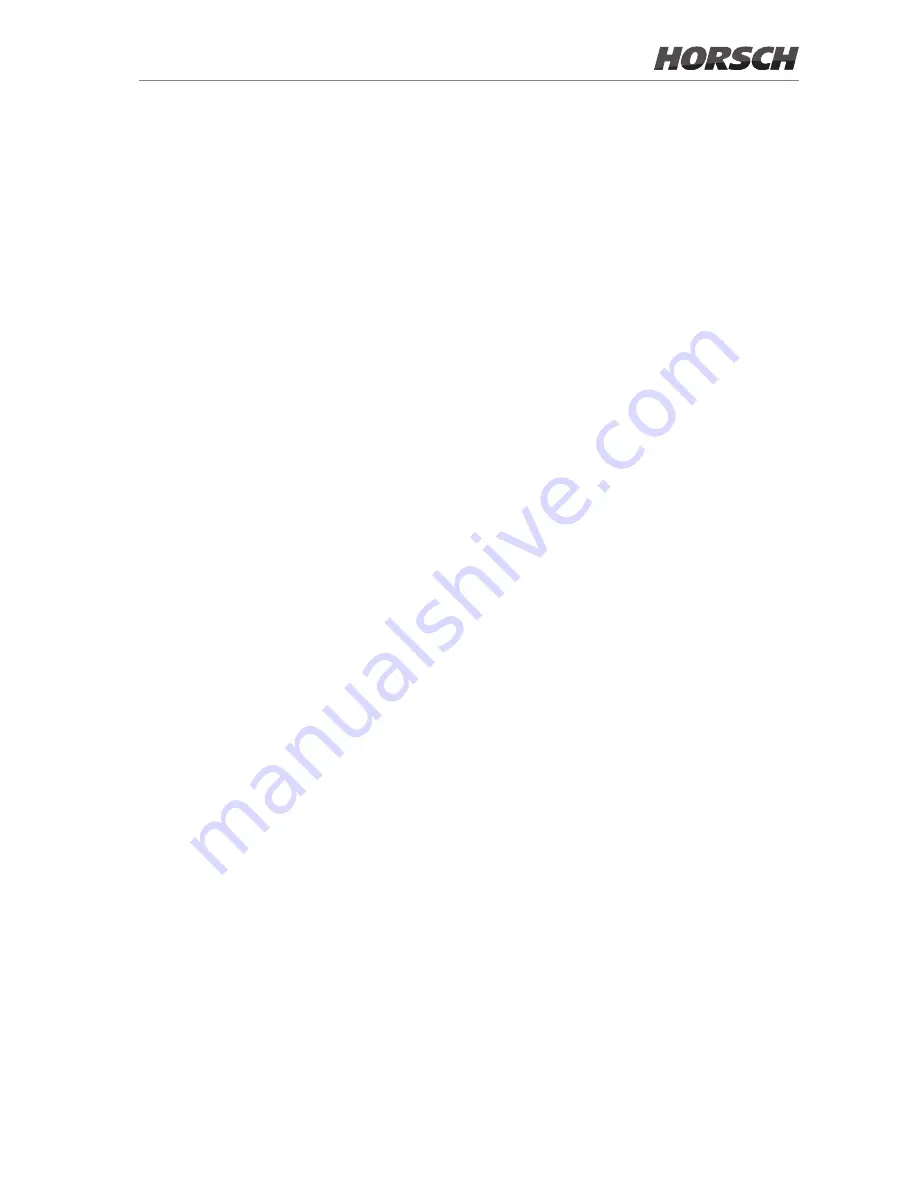
Depth setting ................................................63
Basic setting ..............................................63
Tine field depth setting ...............................63
DiscSystem depth setting ..........................63
Use in the field ..............................................64
Checks..........................................................65
Optional equipment ....................................66
Brake system ................................................66
Pneumatic brake ........................................66
Hydraulic brake ..........................................67
Parking brake .............................................68
Optional equipment ....................................69
TopRing Packer ............................................69
SteelDisc Packer ..........................................70
Rear drawing hook .......................................70
Fertiliser distribution .....................................71
Bout marker ..................................................72
Rear two-point hitching .................................73
Maintenance and Servicing .......................74
Cleaning .......................................................74
Lubricating machine .....................................74
Maintenance Periods ....................................74
Storage .........................................................74
Maintenance overview ..................................75
Appendix .....................................................80
Coulter arrangement.....................................80
Waste disposal ...........................................84
Appendix .....................................................85
Tightening torques ........................................85
Index ............................................................87
3
Summary of Contents for Tiger 3 MT
Page 2: ......
Page 5: ......
Page 21: ...Position of safety stickers depending on equipment Tiger 8 MT 17...
Page 85: ...Direction of travel Tiger 4 MT rigid Tiger 4 MT Direction of travel 81...
Page 86: ...Direction of travel Tiger 5 MT Direction of travel Tiger 6 MT 82...
Page 87: ...Direction of travel Tiger 8 MT 83...
Page 93: ......