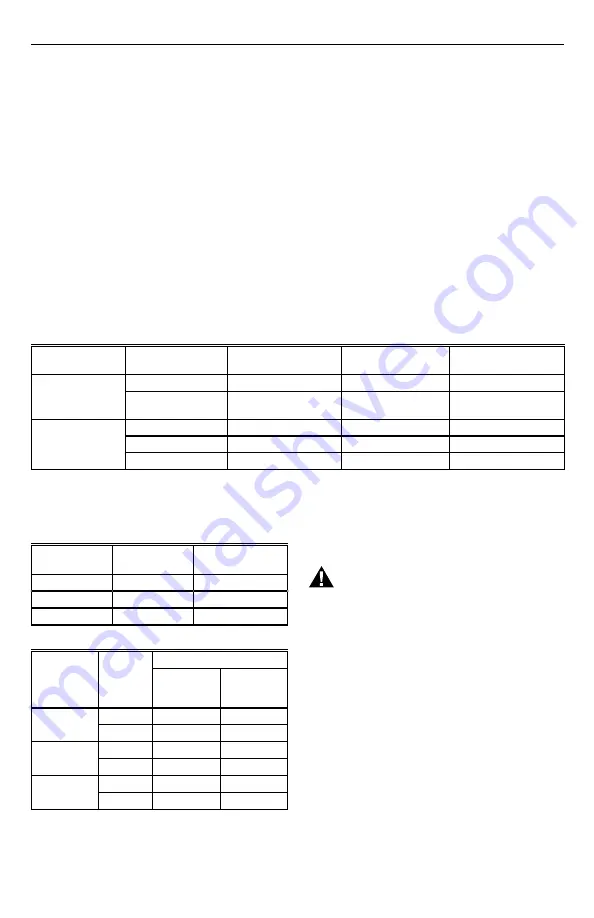
69-1059
2
SV9540; SV9640 SmartValve™ SYSTEM CONTROLS
PLANNING THE INSTALLATION
WARNING
FIRE OR EXPLOSION HAZARD
CAN CAUSE PROPERTY DAMAGE,
SEVERE INJURY, OR DEATH
Follow these warnings exactly:
1.
Plan the installation as outlined below.
2.
Plan for frequent maintenance as described in
the Maintenance section.
When intermittent pilot systems are used on central
heating equipment in barns, greenhouses, and commercial
properties and on heating appliances such as commercial
cookers, agricultural equipment, industrial heating
equipment and pool heaters, heavy demands are made on
the controls. Special steps may be required to prevent
nuisance shutdowns and control failure due to frequent
cycling, severe environmental conditions related to
moisture, corrosive chemicals, dust or excessive heat.
These applications require Honeywell Home and Building
Control Engineering review; contact your Honeywell Sales
Representative for assistance.
Review the following conditions that can apply to your
specific installation and take the precautionary steps
suggested.
Regulation Range (Btuh);
SV9540 with 1/2 in. NPT Outlet:
Natural Gas:
Minimum: 20,000.
Maximum: 200,000.
LP Gas:
Minimum: 40,000.
Maximum: 200,000.
SV9540 with 1/2 in. Inverted Flare Outlet:
Natural Gas:
Minimum: 20,000.
Maximum: 180,000.
LP Gas:
Minimum: 40,000.
Maximum: 180,000.
SV9640 (3/4 in. x 3/4 in.):
Natural Gas:
Minimum: 30,000.
Maximum: 415,000.
LP Gas:
Minimum: 30,000.
Maximum: 415,000
Natural-LP Gas Conversion Kits:
Natural Gas to LP:
393691 Conversion Kit.
LP to Natural Gas:
394588 Conversion Kit.
IMPORTANT
SV9540P; SV9640P CANNOT be field-converted
to LP or natural gas.
Pipe Adapters:
Angle and straight adapters available for 3/8-, 1/2- and 3/
4-in. pipe. See Table 5. Flange kits include one flange with
attached O-ring, four mounting screws, a 9/64 in. hex
wrench and instructions.
Approvals:
International Approval Services (IAS):
Design Certified C2030025.
Table 3. Capacity
b
of SV9540; SV9640.
Model
Size
(Inlet x Outlet) (in.)
Capacity (at 1 in.
wc pressure drop
a,c
)
Minimum
Regulated Capacity
Maximum
Regulated Capacity
SV9540
1/2 x 1/2 NPT
150 ft
3
/hr (4.2 m
3
/hr)
20 ft
3
/hr (0.6 m
3
/hr)
200 ft
3
/hr (5.7 m
3
/hr)
1/2 NPT x 1/2
inverted flare
130 ft
3
/hr (3.7 m
3
/hr)
20 ft
3
/hr (0.6 m
3
/hr)
180 ft
3
/hr (5.1 m
3
/hr)
SV9640
1/2 x 1/2
240 ft
3
/hr (6.8 m
3
/hr)
30 ft
3
/hr (0.8 m
3
/hr)
340 ft
3
/hr (9.6 m
3
/hr)
1/2 x 3/4
270 ft
3
/hr (7.6 m
3
/hr)
30 ft
3
/hr (0.8 m
3
/hr)
370 ft
3
/hr (10.5 m
3
/hr)
3/4 x 3/4
300 ft3/hr (8.5 m3/hr)
30 ft3/hr (0.8 m3/hr)
415 ft3/hr (11.8 m3/hr)
Gas
Specific
Gravity
Multiply Listed
Capacity By
Manufactured
0.60
0.516
Mixed
0.70
0.765
Propane
1.53
1.62
a
Capacity based on 1000 Btu/feet
3
, 0.64 specific gravity natural gas at 1 in. wc pressure drop (37.3 MJ/meter
3
, 0.64
specific gravity natural gas at 0.25 kPa pressure drop).
b
Capacity is reduced by 5 percent with the use of outlet screen.
c
Valves are guaranteed at only 77 percent of the rating.
Part No.
a,b
Inlet/Outlet
Pipe Size
Flange
Type
Without
Hex
Wrench
With Hex
Wrench
3/8 in. NPT
Straight
393690-1
393690-11
Elbow
393690-2
393690-12
1/2 in. NPT
Straight
393690-6
393690-16
Elbow
393690-3
393690-13
3/4 in. NPT
Straight
393690-4
393690-14
Elbow
393690-5
393690-15
Table 4. Gas Capacity Conversion Factor.
Table 5. Adapter (Flange) Part Numbers.
a
Flange kits include one flange, one O-ring and four
mounting screws.
b
Do not use flanges on control models with 3/4 in. inlet
and 3/4 in. outlet. On models with 1/2 in. inlet and
3/4 in. outlet, use flanges only on the 1/2 in. inlet side.