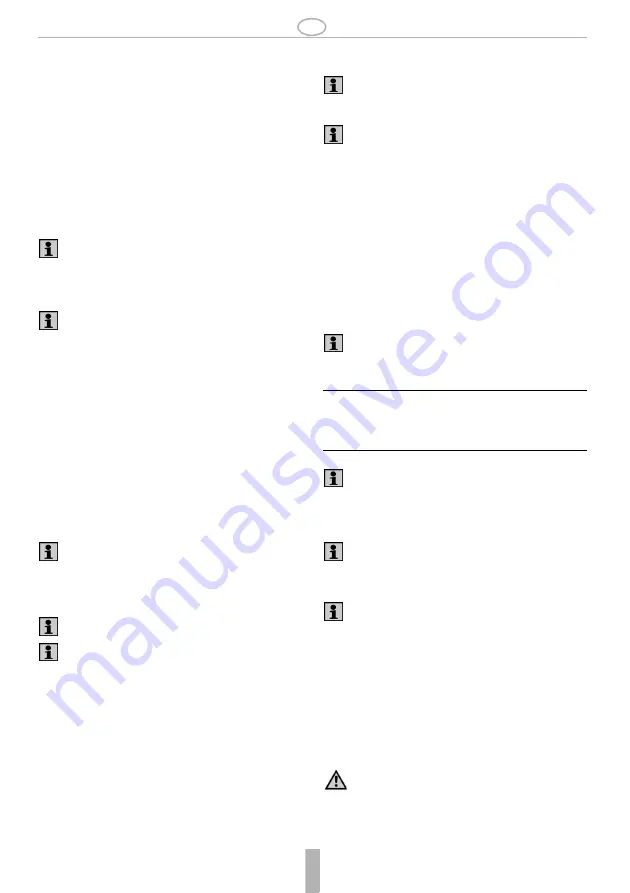
MU1H-1556GE23 R1114
7
Honeywell GmbH
GB
• Provide a straight section of pipework of at least five times
the nominal valve diameter after the pressure reducing
valve (in accordance with EN 806)
• The refilling combination has an integrated strainer - no
separate strainer necessary
- Refilling combination is protected against malfunction
and corrosion damage resulting from ingress of foreign
bodies, e.g. welding beads, sealing materials, metal
cuttings and rust
• The national installation regulations must be observed
during the assembly.
7.2. Assembly instructions
1. Thoroughly flush pipework
2. Install refilling combination
• Install in horizontal pipework with discharge connection
directed downwards
• Note flow direction (indicated by arrow)
• Install without tension or bending stresses
3. Provide a straight section of pipework of at least five times
the nominal size after the refilling combination
4. Attach drain pipe to discharge connection (plastic pipe
40 mm)
8. Start-up
8.1. Filling up the system
1. Slowly open shut off valves on inlet and outlet
8.2. Setting outlet pressure
1. Close shut off valve on inlet and outlet
2. Release pressure on outlet side
• e.g. loosen the pressure gauge
• afterwards screw in pressure gauge again
3. Slacken tension in compression spring
• Turn adjustment handle counter clockwise (-) until it
does not move any more
4. Slowly open shutoff valve on inlet
5. Turn adjuster knob until the pressure gauge shows the
desired value
6. Slowly open shutoff valve on outlet
9. Maintenance
9.1. Inspection
9.1.1. Testing pressure reducing valve
1. Close shutoff valve on outlet
2. Check outlet pressure on pressure gauge when no flow is
occurring
• If the pressure is increasing slowly, the valve may be
dirty or defective. In this instance, carry out servicing
and cleaning
3. Slowly open shutoff valve on outlet
9.1.2. Testing discharge valve
1. Procedure according to instruction of the test control unit
TKA295 resp. TK295
9.1.3. Testing outlet check valve
1. Procedure according to instruction of the test control unit
TKA295 resp. TK295
9.2. Maintenance
In accordance with DIN EN 1717 a regular maintenance must
be taken.
9.2.1. Valve insert
1. Close shut off valve on inlet and outlet
2. Release pressure on outlet side
• e.g. loosen the closing plug 1
• afterwards screw in closing plug again
3. Slacken tension in compression spring
• Turn adjustment handle counter clockwise (-) until it
does not move any more
To avoid stagnating water the refilling combination
(NK300S) must be attached as directly as possible to
the service pipe!
The rules of the drinking water regulation must be
considered during the assembly!
Fasten the plastic sealing plugs manually only (without
tools)
Because of casual fluctuation of pressure dripping water
at discharge valve can occur!
This is no malfunction and therefore no reason for
complaint!
Pressure reducing valve is set to 1.5 bar by factory.
The pressure of the system should be at least 2 bar
above the set outlet pressure.
Maintenance of backflow preventer must be carried out
by authorized personnel!
• Frequency: every 6 month (depending on local
operating conditions)
• To be carried out by an installation company
Inspection with a test control unit and maintenance-set
(see accessories)
Take note of the instructions of the test control unit
TKA295 or TK295
Quick test for the discharge valve:
• Lower the inlet pressure
if the discharge valve opens (it drops), the function is
o.k.
Take note of the instructions of the test control unit
TKA295 or TK295
We recommend a planned maintenance contract with
an installation company
Frequency: every 1-3 years (depending on local
operating conditions)
To be carried out by an installation company
Caution !
There is a spring in the spring bonnet. It may cause
injuries if the spring is derailing.
• Make sure tension in compression spring is
slakkened!