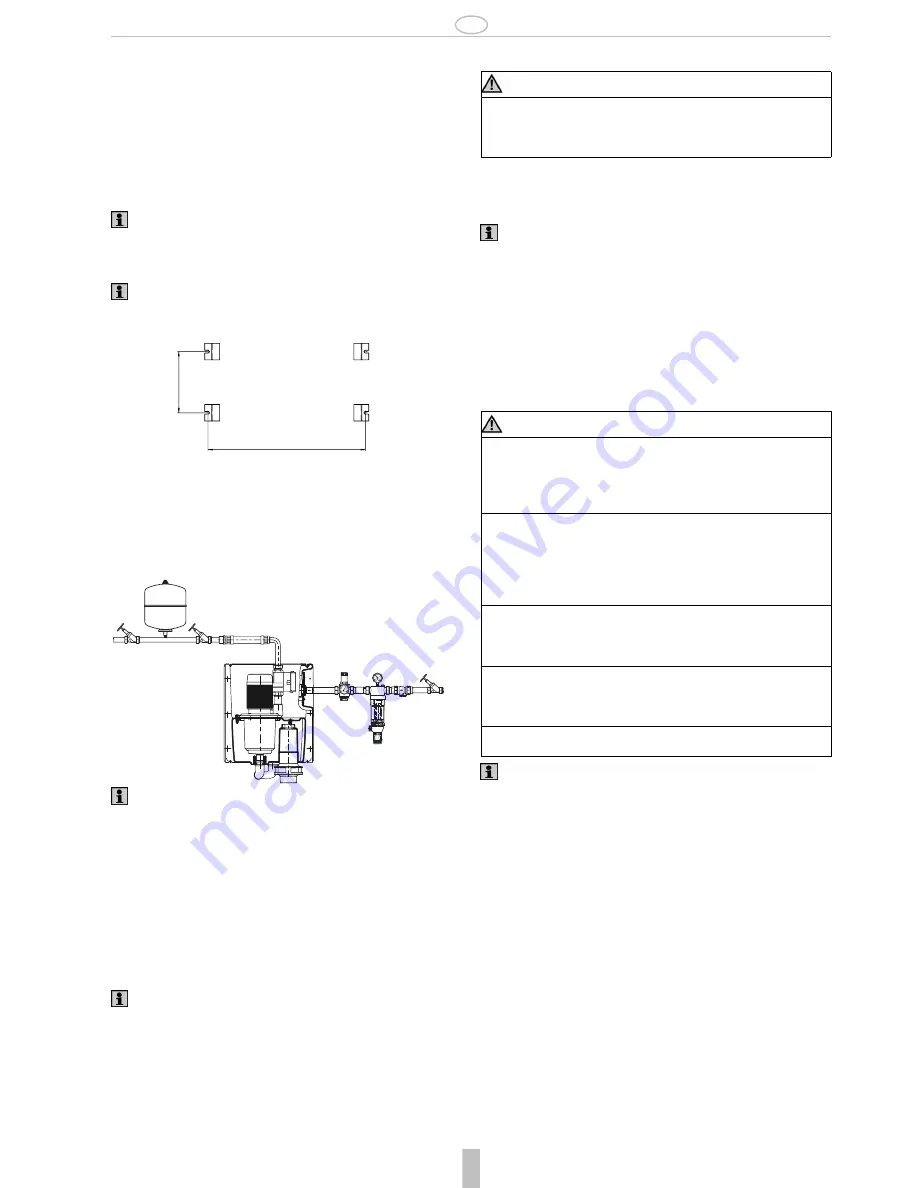
Honeywell GmbH
10
Translation of original - EN1H-1377GE23 R1114
GB
6.3 Inspection before assembly
Check the following points prior to installation:
• According to specifications on the type label, the system is suitable for the
electric supply network.
• The medium to be pumped corresponds to the permissible pumping
media
• The above-mentioned safety instructions have been observed.
• The installation room is dry, frost-free and well-ventilated.
6.3.1 Installation site
6.4 Installing the compact booster unit
1. Remove the packaging before installing the system.
2. Mark the 4 mounting points using the drilling template included.
3. Drill holes (4 x Ø10mm).
4. Insert suitable, proper sized dowels.
- wall plugs included only for mounting in concrete and full brick walls.
5. Mount and adjust both of the lower fixing attachments.
6. Set the system in both of the lower fixing attachments.
7. Mount upper fixing attachments.
6.5 Installing the pipelines
6.5.1 Water connection
1. Attach inlet connection R
3
/
4
" with flexible pressure hose to the drinking
water line.
2. Fill angular tank with water.
3. Open drinking water line.
- After opening the drinking water line, the tank is automatically filled.
6.5.2 Pressure connection
1. Install membrane pressure expansion vessel in consumption water line.
Set pre-pressure to 3,2 - 3,4 bar. For filling use nitrogen only!
2. Connect the system to the consumption water line using the flexible pres-
sure hose.
6.5.3 Connecting the overflow
An overflow for free drain as prescribed by EN 1717 is implemented, and
has a nominal width of 70mm for this system. This overflow becomes effec-
tive when the drinking water backfeed leaks and the water exceeds the
maximal overflow point.
1. Connect the overflow.
6.6 Electrical connection
6.6.1 Safety instructions
1. Compare the mains voltage with the specifications on the type label.
2. Insert mains plug in the electrical socket.
6.7 Verification of the waterflow
The water shortage monitor must not be activated at maximal withdrawal.
Should the water shortage monitor nevertheless be activated, then the pres-
sure side must be throttled. For maximum withdrawal and backfeed amounts
see chapter description.
Ideally select an outer wall for mounting.
The wall must be able to take 4 wall plugs Ø 10mm and carry the weight
of the system (approx. 35 kg when filled with water).
Make allowance for space for operating and maintenance tasks.
Install connecting cable with zero potential. No load is allowed to be put
on either the connections or the system.
Install pressure reducing valve ahead of the system to ensure that not
more than 4bar prepressure is fed from the drinking water network.
It is recommended to install a stop valve and an external filter.
Avoid overly bending the flexible connecting pipe, as this reduces the
service life and puts an improper load on the connections.
To avoid frequently pump activation for small withdrawal amounts, in-
stall membrane pressure expansion vessel downstream of the CBU. A
membrane pressure expansion vessel is included in scope of delivery.
It is recommended to install a stop valve.
476
185
Caution
Overflow not connected
ª
Danger of flooding the installation room!
Lead the overflow line to a drain with adequate dewatering
capacity (connection DN70).
The absence of backwater prevention due to the wastewater system
leads to the loss of DVGW-approval! If the systems overflow funnel is
missing, the system must be connected to the wastewater system with
an overflow siphon found in the accessories. In doing so, it must be en-
sured that the overflow siphon is not firmly connected to the system and
that the installation is performed according to DIN 1986-100, EN 1717.
With a secure connection to the wastewater system, we recommend the
installation of a siphon to avoid unpleasant odour.
Danger
Danger of injury from electric voltage.
ª
High shock currents and burns from direct and indirect contact with
live parts.
Turn off the power supply before assembling the compact
booster unit and secure it from being turned on.
Faulty mains connection
ª
Damage to the electricity network, short circuit!
The electrical system must conform with the installation regula-
tions according to VDE 100 (i.e. grounded electrical sockets).
The electrical network must be equipped with a residual current
device for max. 30mA.
Non- or erroneously-connected cables
ª
Malfunctions, which endanger the safety of operating personnel.
Work on electrical equipment may only be performed by specia-
list electric technicians.
Improperly connected wiring and lines (e.g. too small bend radius)
ª
Smouldering and fires from cables.
Work on electrical equipment may only be performed by specia-
list electric technicians.
Live cable ends and components
Make sure the protective earth system is connected throughout.
The installation of a motor protection device is recommended.