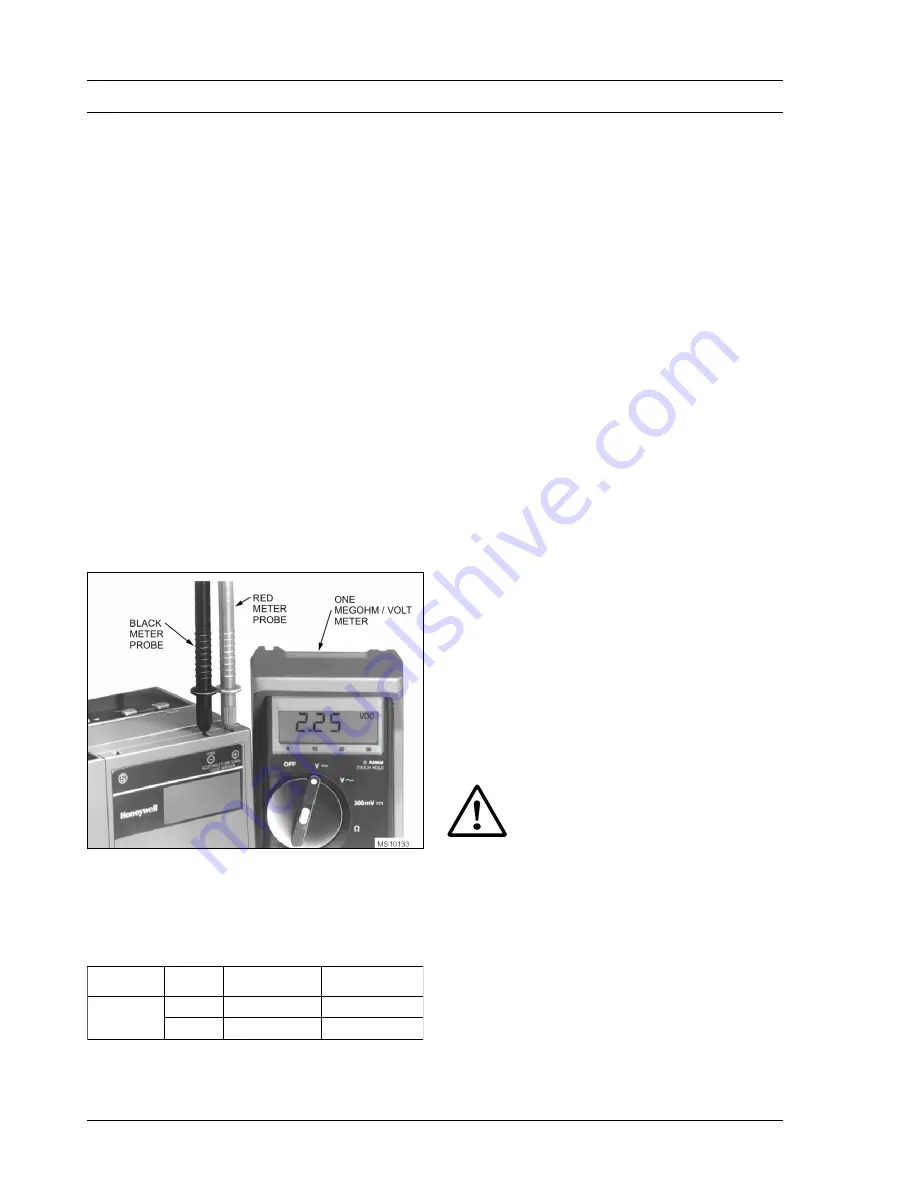
EN1C-0015SZ20 R0602
12
ADJUSTMENTS AND CHECKOUT
Adjust Detector Sighting
With the flame detector installed and the burner running,
adjust the sighting position of the detector for optimum flame
signal. It is suggested that a volt-Ohm meter with a minimum
sensitivity of one megohm/volt and a zero to five or ten Vdc
scale be used for R7861 amplifier flame signal measurements.
Measure the flame signal as illustrated in Fig. 11. Be careful
to make the proper connections of positive (red) meter lead
to positive (+) control jack and negative (black) meter lead to
negative (-) or (-Com) jack with 7800 SERIES controls. When
the 7800 SERIES control has the keyboard display module,
a zero to five Vdc voltage is displayed on the module.
NOTE: The flame Signal must be steady.“Use a W136 test
meter (or similar) when measuring the current on an
R7061 amplifier.
Move the detector and sight pipe around to sight the flame
from various positions and angles. Try to get a maximum
steady (or stable) reading on the meter. The signal must be
above the minimum acceptable voltage listed in Table 1.
Measure the flame signal for the pilot alone, the main burner
flame alone, and both together (unless monitoring only the
pilot flame when using an intermittent pilot, or only the main
burner flame when using direct spark ignition). Also measure
the flame signal at low and high firing rates and while
modulating in between (as applicable). With the detector in
its final position, all required flame signals must be steady
(or stable) and as specified in Table 1. If you cannot obtain
the proper signal, refer to the Troubleshooting section.
Pilot Turndown Test
If the detector is used to prove a pilot flame before the main
fuel valve(s) can be opened, perform a pilot turndown test
before welding the sight pipe into position. Follow the
procedures in the flame safeguard control instructions and
in the burner manufacturer instructions.
lgnition Spark Response Test
Test to make certain that ignition spark is not actuating the
flame relay in the flame safeguard control.
A Close the pilot and main burner manual shutoff valves.
B Start the burner and run through the lgnition period. lgnition
spark should occur, but the flame LED must not light. The
flame signal should not be greater than 0.25 Vdc.
C If the flame relay does pull in, reposition the detector farther
from the spark, or relocate/resight the detector to
eliminate/reduce the detector response to reflected UV
radiation. It may be necessary to construct a barrier to
block the ignition spark from the detector view. Continue
adjustments until the flame signal due to ignition spark is
less than the flame signal values indicated in step B.
Response to other Ultraviolet Radiation Sources
Some sources of artificial light produce small amounts of
ultraviolet radiation. Under certain conditions, an ultraviolet
detector responds to them as if it is sensing a flame. Do not
use an artificial light source to check the response of an
ultraviolet flame detector. To check for proper detector
operation, conduct flame failure response tests under all
operating conditions.
Weld the Sight Pipe
When the flame signal is acceptable after all adjustments
are made, remove the detector and weld the sight pipe in its
final position. (lf you are using a swivel mount, the pipe may
already be welded). Then reinstall the detector.
Final Checkout
Before putting the burner into service, check out the
installation using the checkout procedures in the instructions
for the appropriate flame safeguard control. After completing
the checkout, run the burner through at least one complete
cycle to verify correct operation.
CAUTION
Do not put the system into operation until all
checkout tests in the instructions for the
appropriate flame safeguard control and any
others specified in the burner installation
instructions are satisfactorily completed.
Fig. 11. Measuring voltage flame Signal with 7800 SERIES
controls
e
m
a
l
F
r
o
t
c
e
t
e
d
r
e
i
f
i
l
p
m
A
e
l
b
a
t
p
e
c
c
a
.
n
i
m
l
a
n
g
i
s
y
d
a
e
t
s
e
l
b
a
t
p
e
c
c
a
.
x
a
m
l
a
n
g
i
s
y
d
a
e
t
s
4
0
0
1
A
1
6
0
7
C
0
2
0
1
A
1
6
0
7
C
3
0
0
0
F
1
6
0
7
C
1
6
0
7
R
A
µ
0
,
3
—
—
1
6
8
7
R
C
d
V
5
2
,
1
C
d
V
0
,
5
Table 1. Flame signal
Summary of Contents for C7061A
Page 16: ...16 EN1C 0015SZ20 R0602 ...