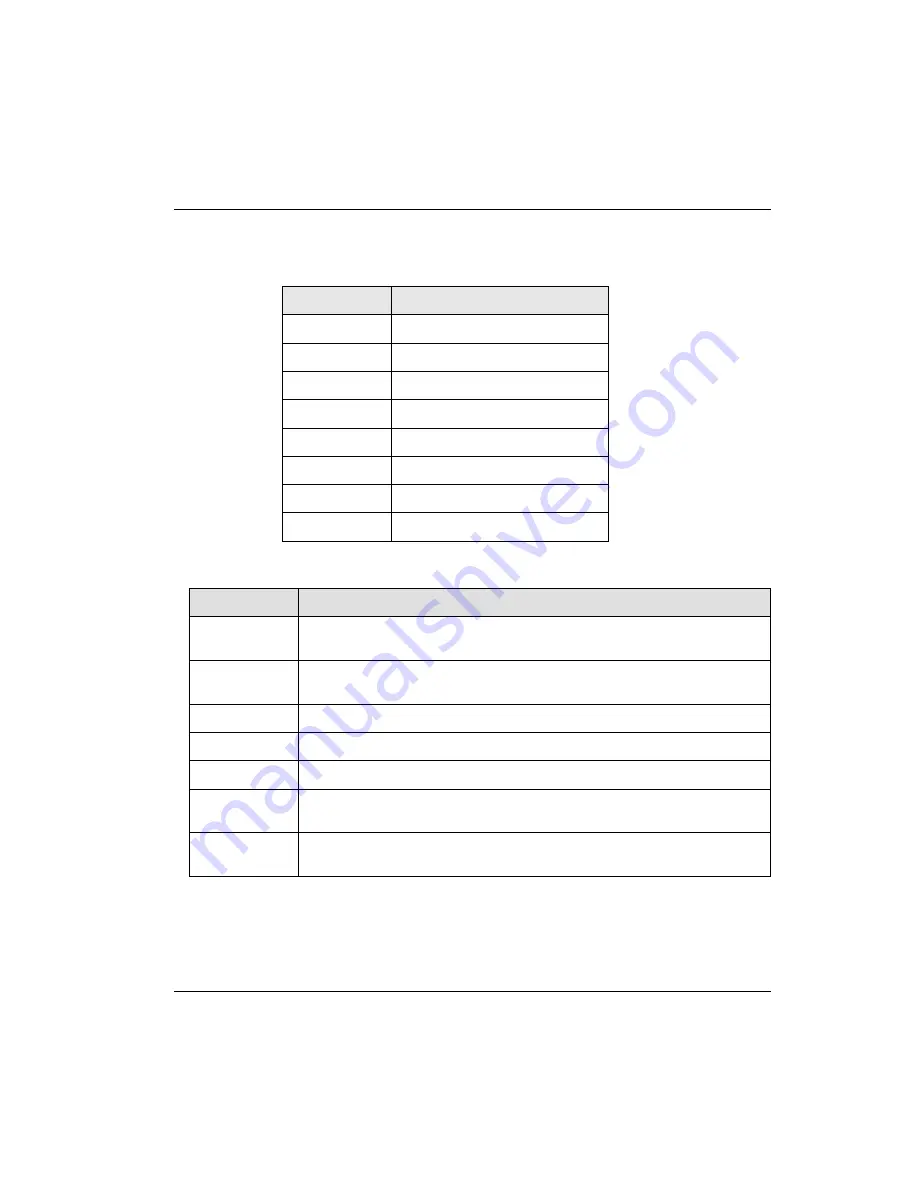
6. Global Constant and Global Variable
6.2. Global Constant
R200
2MLF-HO2A, 2MLF-HD2A High Speed Counter Module User's Guide
93
May 2010
Honeywell
2.
Pulse input types (channel 0: _Fxy_CH0_PLS_MODE, channel 1:
_Fxy_CH1_PLS_MODE)
Setting value
Contents
0
2 phase 1 multiplier
1
2 phase 2 multiplier
2
2 phase 4 multiplier
3
CW/CCW
4
1 phase /1 input /1 multiplier
5
1 phase /1 input /2 multiplier
6
1 phase /2 input /1 multiplier
7
1 phase /2 input /2 multiplier
3.
Comparison output types (channel 0: _Fxy_CH0_CP0 (1)_MODE, channel 1:
_Fxy_CH1_CP0 (1)_MODE)
Setting value
Contents
0
In case of current count value < comparison reference value, OUT0(1) is
On
1
In case of current count value ≤ comparison reference value, OUT0(1) is
On
2
In case of current count value = comparison reference value, OUT(1) is On
3
In case of current count value ≥ comparison reference value, OUT(1) is On
4
In case of current count value > comparison reference value, OUT(1) is On
5
In case of comparison minimum value ≤ current count value ≤ comparison
maximum value, OUT(1) is On
6
In case of comparison minimum value ≥ current count value, current count
value ≤ comparison maximum value, OUT(1) is On