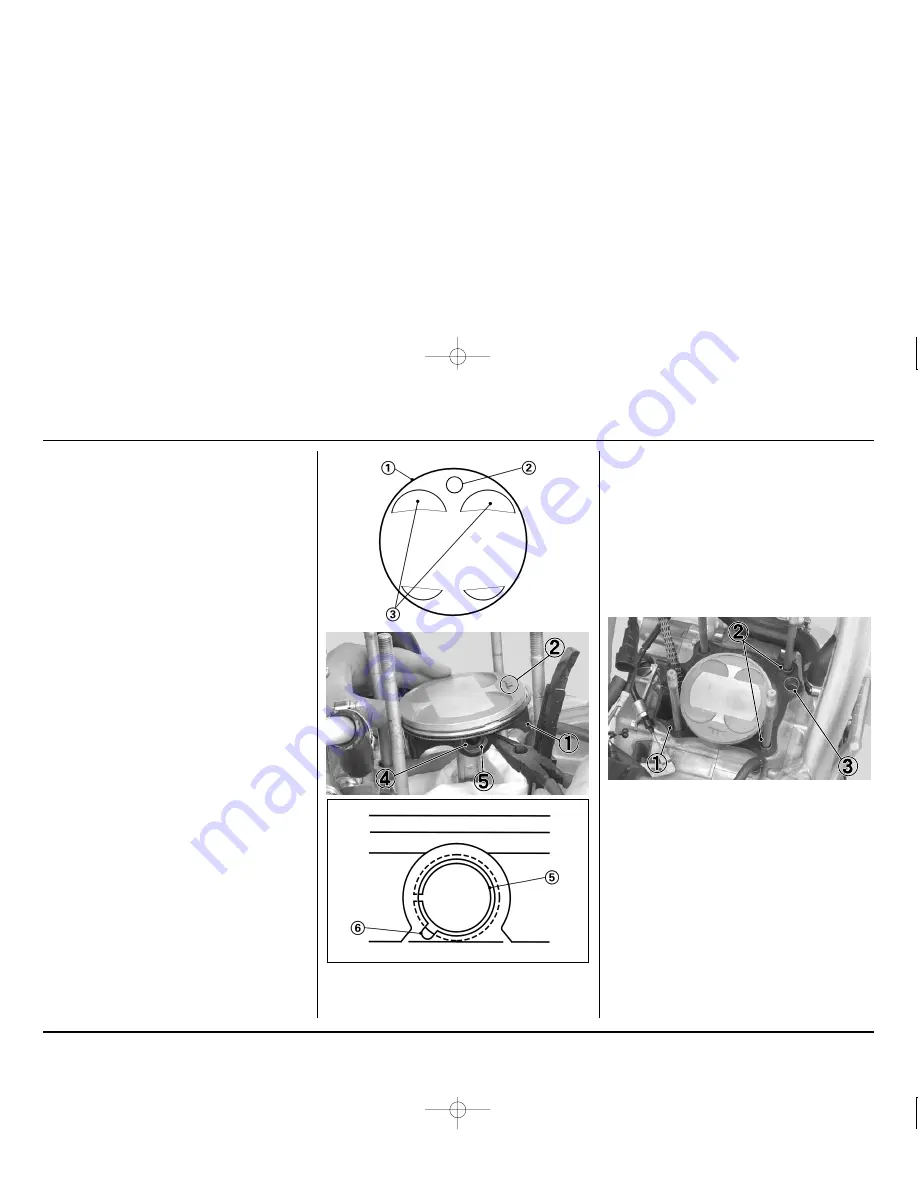
43
Piston Installation
Place clean shop towels in the crankcase to keep the
piston pin clips from falling into the crankcase.
Apply molybdenum disulfide oil (a mixture of 1/2 en-
gine oil and 1/2 molybdenum disulfide grease (con-
taining more than 3% molybdenum disulfide additive))
to the connecting rod small end.
Install the piston with the “IN” mark and/or the large
valve recesses facing the intake side of the engine.
Apply flesh engine oil to the piston pin.
Install the piston pin and new piston pin clips.
CAUTION:
•
Use new pin clips. Never reuse old clips.
•
Do not let the clips fall into the crankcase.
•
Do not align the piston pin clip end gap with the
piston cut-out.
(1) PISTON
(2) “IN” MARK
(3) LARGE VALVE RECESSES
(4) PISTON PIN
(5) PISTON PIN CLIP
(6) CUT-OUT
Cylinder Installation
Clean off any gasket material from the gasket surface
of the crankcase, being careful not to let any material
fall into the crankcase.
NOTE:
•
Be careful not to remove any metal from the gasket
surface.
Remove the shop towel. Do not let any gasket debris
fall into the crankcase.
Install cylinder gasket, A dowel Pins and B dowel pin.
CAUTION:
•
Do not let the dowel pins fall into the crankcase.
(1) CYLINDER GASKET
(2) A DOWEL PINS
(3) B DOWEL PIN
Clean the any gasket material off the cylinder.
IN