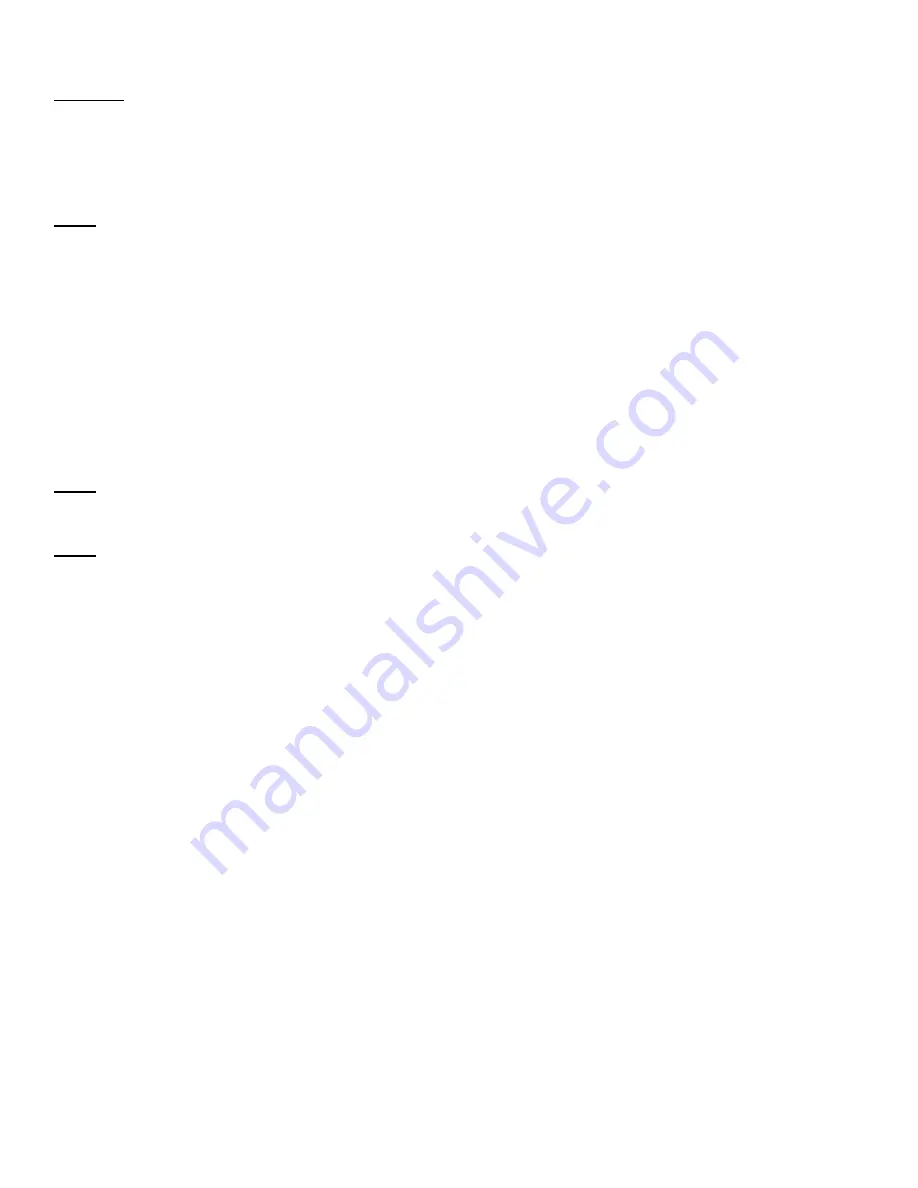
12
3. Drill a 7/8” hole into the exhaust pipe where the oxygen sensor will be mounted.
WARNING! Ensure that no metal shavings enter the exhaust that may cause damage to either your catalytic converters or
mufflers. To remove any metal shavings, insert a small magnet into the hole and use the magnet to collect the
shavings.
4. Insert the weld ring into the hole and carefully weld the ring in place by placing a bead all the way around the outer edge of the weld
ring to ensure a leak proof connection. Ensure that you do not damage the threads inside the weld ring. If you damage the threads
inside the weld ring, use a 18 mm tap to re-thread the weld ring.
NOTE:
Someone with experience welding exhaust should install the oxygen sensor weld ring. Any competent exhaust shop will be
able to accomplish this task at a minimum cost.
5. Although the oxygen sensor is supplied with a small amount of anti seize compound applied to the oxygen sensor threads, Holley
recommends that the thread be thoroughly coated with additional anti-seize compound. When applying the anti-seize compound,
ensure that the stainless steel sensor head remains clean. Insert the oxygen sensor into the weld ring and tighten it securely with a
7/8” open end wrench.
DO NOT OVERTIGHTEN THE OXYGEN SENSOR!
6. Connect the wiring harness to the oxygen sensor by pressing the two three position connectors together until the locking latch on
the oxygen sensor connector snaps into place.
7. Route the wiring harness, away from any direct sources of heat and moving parts, from the oxygen sensor to the rear of the ECU.
Secure the wiring harness with wire ties or wire clamps.
8. Reconnect the primary wiring harness, previously disconnected, to the ECU. Plug the small, black connector on the oxygen sensor
wiring harness into the 6 position connector on the rear of the ECU.
NOTE:
The oxygen sensor should only be used AFTER the
PRO-JECTION
2D
system has been properly tuned in an open loop mode
(oxygen sensor is disconnected). Utilizing the oxygen sensor without first tuning the
PRO-JECTION
2D
system in an open
loop mode may result in engine fuel requirements that are outside the range of adjustment of the closed loop system.
NOTE:
The digital ECU utilizes only three of the six positions in the small connector on the rear of the ECU. The other three positions
are for FACTORY USE ONLY and no connections should be made to these 3 connector positions.
SYSTEM MAINTENANCE
The
PRO-JECTION
2D
system is virtually maintenance free. To ensure performance and reliability, periodically check all fuel lines for
leaks and replace them as needed. Also ensure that all electrical connections remain secure and that all wires are routed away from
and direct sources of heat, such as the exhaust system, and any moving parts.
If a decrease in system performance is noticed, a dirty or clogged fuel filter may be the cause. Holley recommends that both fuel filters
(installed with the
PRO-JECTION
2D
system) be changed every 20,000 miles of normal operation. These filters are non-serviceable
and must be replaced. Contact your local parts dealer for replacement fuel filters.