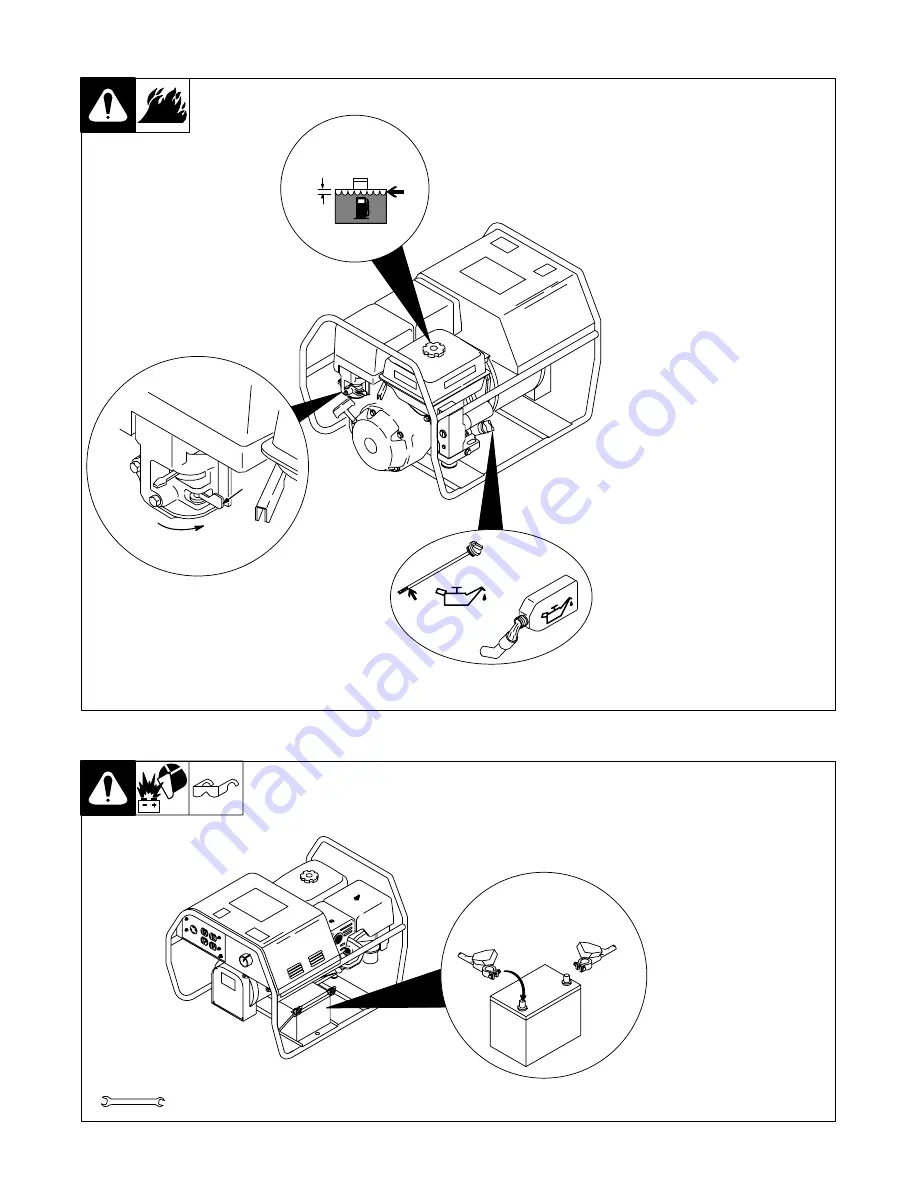
OM-498 Page 15
4-5.
Engine Prestart Checks (Honda-Powered Units)
Ref. 802 099-A
Full
Full
Gasoline
1/2 in
(13 mm)
Check all fluids daily. Engine must
be cold and on a level surface. Unit
is shipped with 10W30 engine oil.
Engine stops if oil level gets too low.
1
Fuel Valve
Open valve.
Close fuel valve before moving
unit or carburetor may flood
and make starting difficult.
Fuel
Add fresh fuel before starting
engine the first time (see mainte-
nance label for specifications). Fill
fuel tank up to 1/2 in. (13 mm) from
top to allow room for expansion.
Check fuel level on a cold engine
before use each day.
Oil
After fueling, check oil with unit on
level surface. If oil is not up to full
mark on dipstick, add oil (see main-
tenance label).
To improve cold weather
starting:
Keep battery in good condition.
Store battery in warm area off
concrete surface.
Use correct grade oil for cold
weather.
1
Open
4-6.
Connecting The Battery (Honda Electric-Start Models Only)
802 100-A / Ref. S-0756-D
3/8, 1/2 in
Tools Needed:
+
–
Connect negative (–)
cable last.
Turn Engine Switch to Off
(electric-start models only).
Summary of Contents for 1435
Page 4: ......
Page 35: ...OM 498 Page 31 198 014 C Figure 9 2 Wiring Diagram For Welding Generator ...
Page 36: ...OM 498 Page 32 201 026 A Figure 9 3 Wiring Diagram For Auxiliary Power Panels 1 Of 2 ...
Page 37: ...OM 498 Page 33 201 026 A Figure 9 4 Wiring Diagram For Auxiliary Power Panels 2 Of 2 ...
Page 53: ...OM 498 Page 49 Notes ...
Page 58: ...OM 498 Page 54 Notes ...