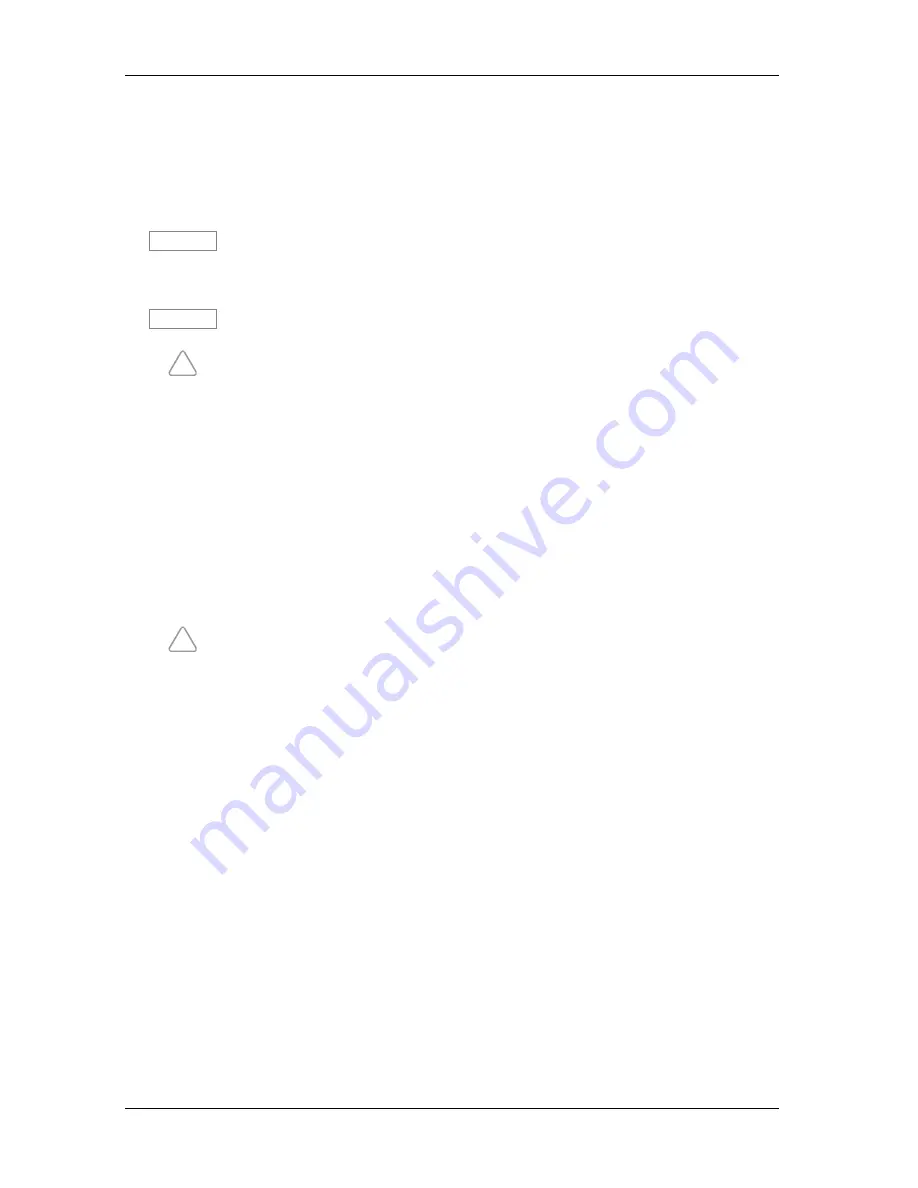
6 System integration
Operation manual mzr-2961, mzr-4661
20
Technical data subject to change without prior notice!
Last update: April 2018
6.3
General instructions for the assembly of the liquid supply network
Foreign bodies and dirt particles can block the micro annular gear pump and
lead to its damage.
Warning
Please note that all the components of the liquid supply system should be
clean and flush them if needed before pump installation. Remember to remove
all remaining splinters or swarf from connection fittings, rests from liquid
containers and any dirt from valves, tubing and filters.
Warning
Operate the pump with a filter featuring 10 µm or smaller pores. The filter
protects the pump from particles and dirt.
!
If the pump is connected once again with a hose that has already been used,
the enlarged ending of the hose should be cut off in order to prevent it from
slipping off and the liquid from flowing out of the connection.
Assembly of the tubing and piping system
1.
Please cut the tubing rectangular with a hose cutter. If metal pipes are used
an intensive cleaning procedure is necessary. After machining the pipes
have to be cleaned and flushed very carefully. Smallest swarfs within the
fluidic system can cause failure of the micro annular gear pump.
2.
Connect the fittings with the tubing respectively the pipe work according to
the attached installation instruction.
!
Please note that the correct assembly of tubes respectively pipes with the
pump head is a necessary condition to secure the right direction of flow. When
you want to operate the pump in reverse direction please contact
HNP Mikrosysteme since this is not possible in any application.
3.
The suction line should be installed ascending to the pump for better
degassing. The suction line should be designed as short as possible. The
inner diameter of the suction line should be large to guarantee good
priming of the liquid. At the planning of the pipe system take care of
possibilities for degassing.
4.
Operate the micro annular gear pump always with a filter with a pore size
of 10 µm or smaller. The filter prevents that particles or solids penetrate
into the pump what can cause major damage.
5.
Avoid dry running of the pump. Make sure that the liquid flow is not
interrupted.