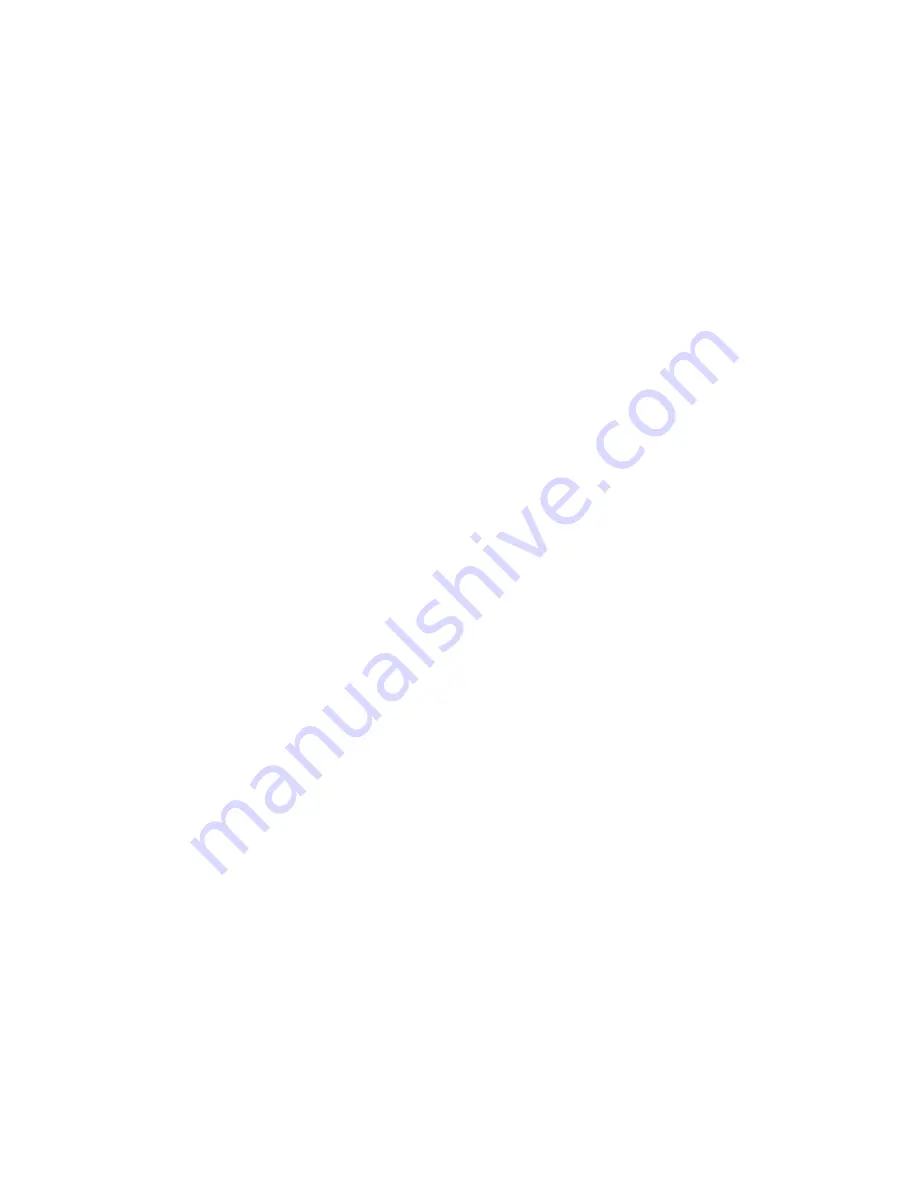
IMPULSE SEALING EQUIPMENT
To ensure that satisfactory sealing performance is achieved and that
service life of consumable spares (such as element wire, Teflon and
rubber pressure pads) are maximised, it is necessary to understand the
operating principles of this type of equipment.
1.
To adjust the heat setting for a particular thickness of material, the
power output is not varied, and varying the length of time that the
current passed through the element resistance wire effects adjustment.
The timer control allows infinitely variable time adjustment up to a
maximum of around 4 seconds.
2.
When the red heating indicator light goes out the temperature has
reached its maximum and the polythene is molten to effect the weld. It
is important that before allowing the jaws to open for removal of the
polythene a short cooling time is allowed to enable the polythene to
solidify and to regain its original strength. On machines fitted with a
dual timer control, the cooling time can be pre-set but on standard
machines with simple heating time control, the operator should allow
sufficient time for cooling before releasing the jaws. Depending on
material thickness a cooling time of 1 to 7 seconds is usually sufficient.
3.
To complete the seal in the minimum possible time considerable power
is applied to the element for the short duration of the welding cycle.
The instantaneous temperature reached during the brief cycle is very
high, but close contact of the rubber pressure pad removes excess
temperature and prevents deterioration of the thin Teflon barrier tape.
4.
It follows that if the pressure bar is released before the temperature
reduces to a level that the Teflon can withstand, it will deteriorate
rapidly and require premature replacement.
5.
For this reason adequate cooling allowance is critical to the service life
of the Teflon. Although capable of withstanding up to 20,000 seals
before replacement, insufficient cooling time can cause burning within a
very short period.
Summary of Contents for HM3000CDM
Page 2: ......