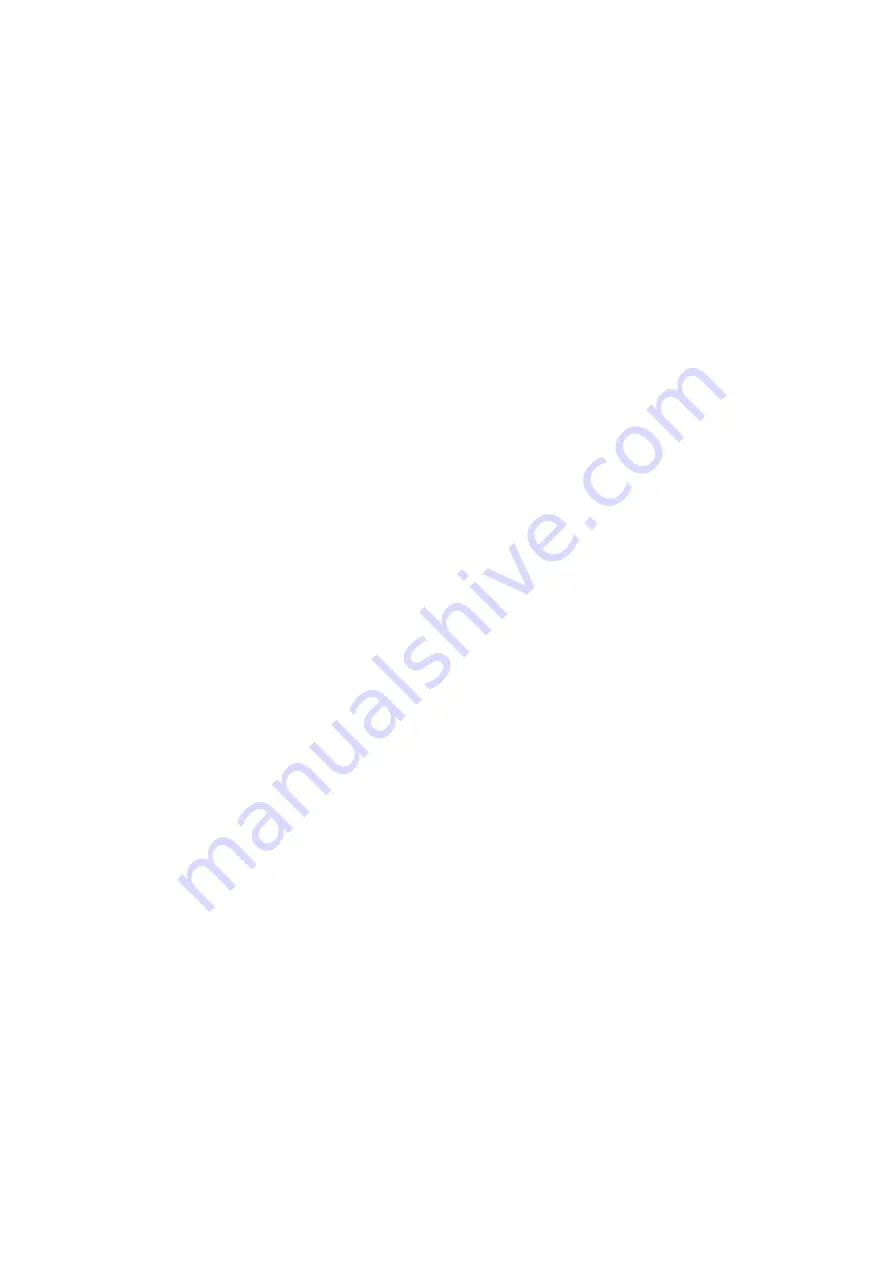
TYP
Type identification
UMT
User management tool
Underreach
A term used to describe how the relay behaves during a fault condition. For
example, a distance relay is underreaching when the impedance presented
to it is greater than the apparent impedance to the fault applied to the
balance point, that is, the set reach. The relay does not “see” the fault but
perhaps it should have seen it. See also Overreach.
UTC
Coordinated Universal Time. A coordinated time scale, maintained by the
Bureau International des Poids et Mesures (BIPM), which forms the basis of
a coordinated dissemination of standard frequencies and time signals. UTC
is derived from International Atomic Time (TAI) by the addition of a whole
number of "leap seconds" to synchronize it with Universal Time 1 (UT1),
thus allowing for the eccentricity of the Earth's orbit, the rotational axis tilt
(23.5 degrees), but still showing the Earth's irregular rotation, on which UT1
is based. The Coordinated Universal Time is expressed using a 24-hour
clock, and uses the Gregorian calendar. It is used for aeroplane and ship
navigation, where it is also sometimes known by the military name, "Zulu
time." "Zulu" in the phonetic alphabet stands for "Z", which stands for
longitude zero.
UV
Undervoltage
WEI
Weak end infeed logic
VT
Voltage transformer
X.21
A digital signalling interface primarily used for telecom equipment
3I
O
Three times zero-sequence current.Often referred to as the residual or the
earth-fault current
3U
O
Three times the zero sequence voltage. Often referred to as the residual
voltage or the neutral point voltage
1MRK 511 403-UEN Rev. L
Section 15
Glossary
Bay control REC670
233
Commissioning manual
© 2017 - 2022 Hitachi Energy. All rights reserved
Summary of Contents for REC670
Page 1: ...Relion 670 SERIES Bay control REC670 Version 2 2 IEC Commissioning manual ...
Page 2: ......
Page 28: ...22 ...
Page 54: ...48 ...
Page 60: ...54 ...
Page 66: ...60 ...
Page 90: ...84 ...
Page 212: ...206 ...
Page 218: ...212 ...
Page 232: ...226 ...
Page 240: ...234 ...
Page 241: ...235 ...