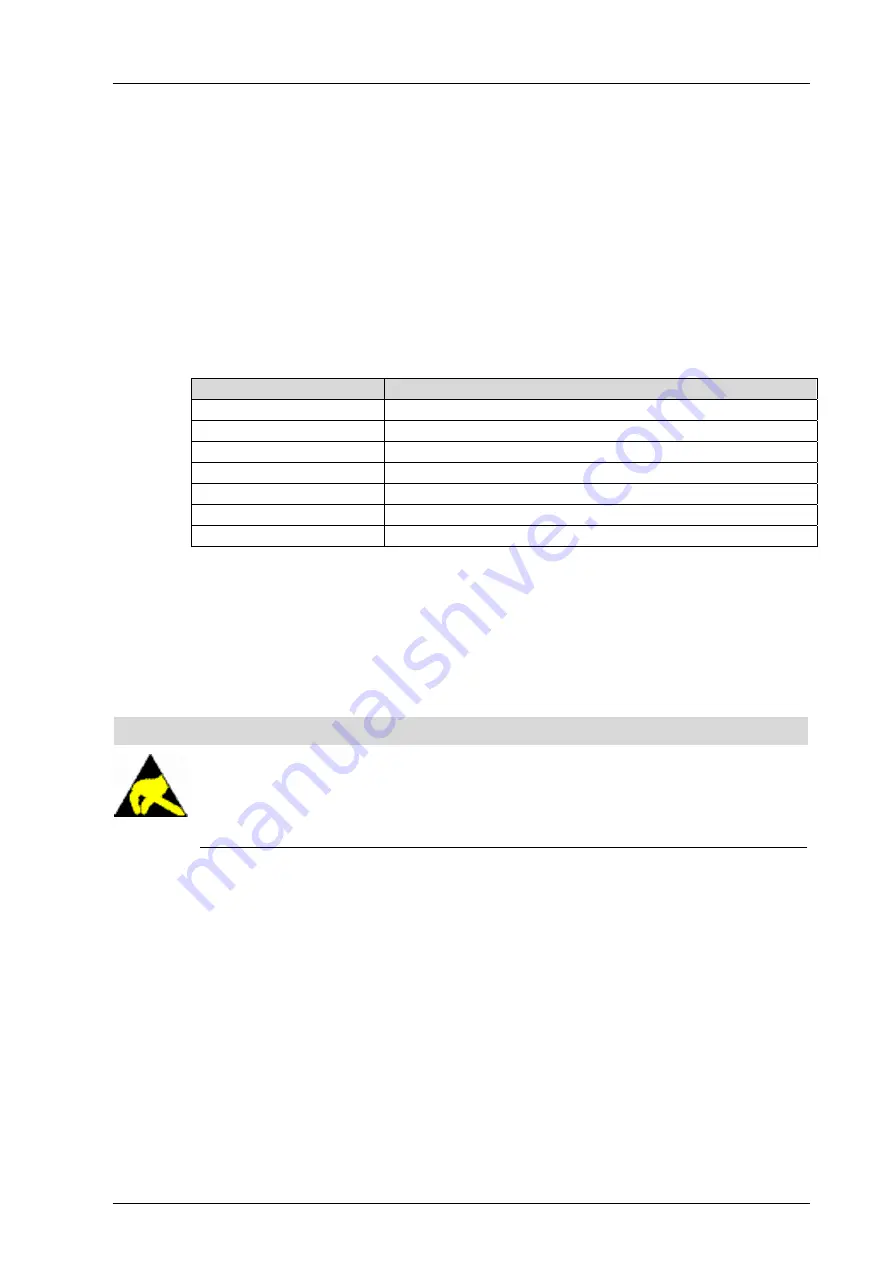
CIO 2/4 01
2 Safety
HI 800 199 E Rev. 1.00
Page 9 of 40
2 Safety
The following safety information, notes and instructions must be strictly observed. The
product may only be used if all guidelines and safety instructions are adhered to.
This product is operated with SELV or PELV. No imminent danger results from the product
itself. The use in Ex-Zone is permitted if additional measures are taken.
2.1 Intended
Use
HIMatrix components are designed for assembling safety-related controller systems.
When using the components in the HIMatrix system, comply with the following general
requirements
2.1.1 Environmental
Requirements
Requirement type
Range of values
Protection class
Protection class III in accordance with IEC/EN 61131-2
Ambient temperature
0...+60 °C
Storage temperature
-40...+85 °C
Pollution
Pollution degree II in accordance with IEC/EN 61131-2
Altitude
< 2000 m
Enclosure Standard:
IP20
Supply voltage
24 VDC
Table 3:
Environmental Requirements
Exposing the HIMax system to environmental conditions other than those specified in this
manual can cause the HIMatrix system to malfunction.
2.1.2
ESD Protective Measures
Only personnel with knowledge of ESD protective measures may modify or extend the
system or replace devices.
NOTE
Device damage due to electrostatic discharge!
When performing the work, make sure that the workspace is free of static and
wear an ESD wrist strap.
If not used, ensure that the device is protected from electrostatic discharge, e.g.,
by storing it in its packaging.
Summary of Contents for HIMatrix CIO 2/4 01
Page 34: ...9 Disposal CIO 2 4 01 Page 34 of 40 HI 800 199 E Rev 1 00...
Page 39: ......