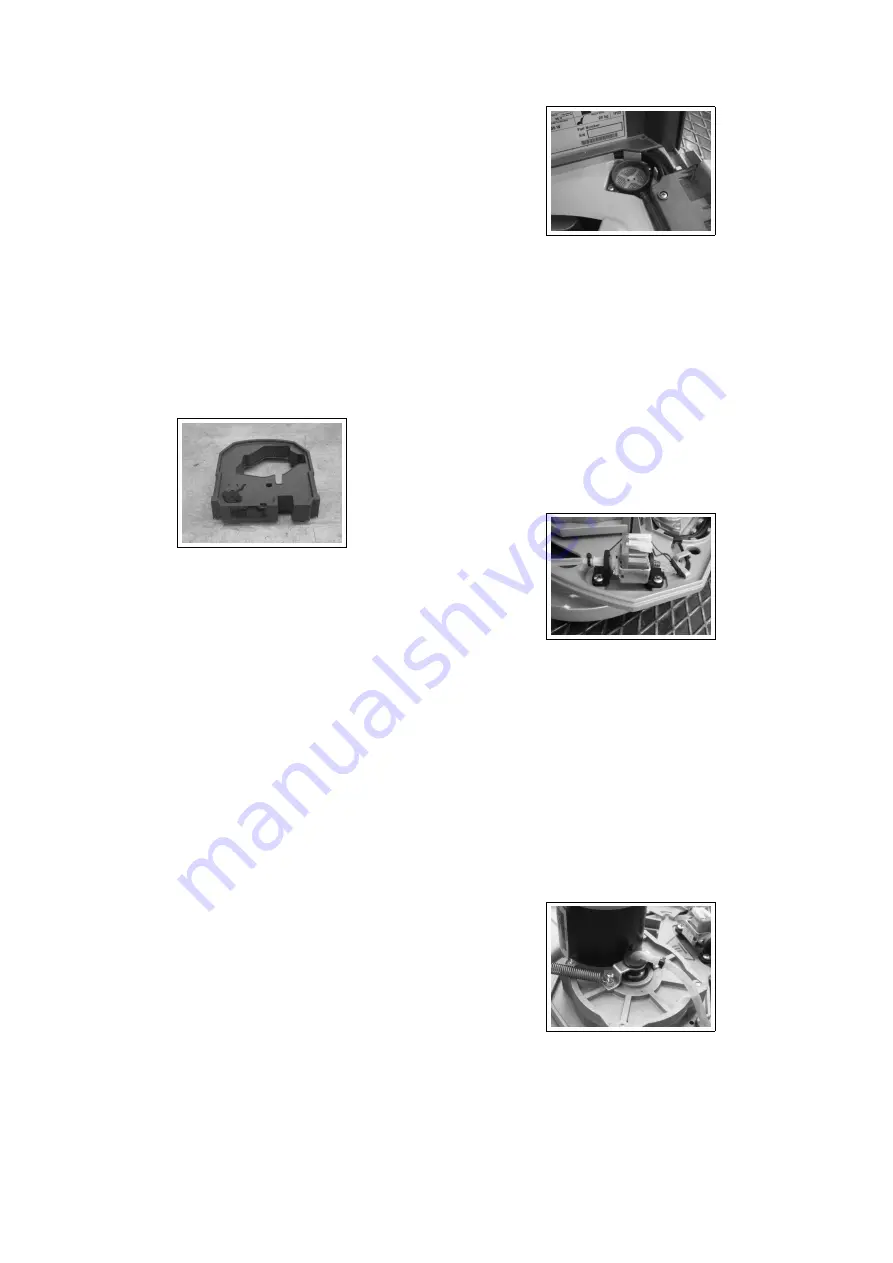
9.3
Maintenance
and
Checks
9.3.1
Solution Tank
Check
(to perform every
50h
)
The solution tank has to be clean and
intact. It has not to have cracks or any
other kind of damage. Verify, when the
tank is completely filled up, that there
are not leakage. If necessary replace the
Solution Tank.
9.3.1-1
9.3.2
Hoses
Check
(to perform every
50h
)
Every single hose has to be intact and
has not to be worn out. It is extremely
important that the hoses kept the orig-
inal flexibility and they haven’t suffered
any chemical reaction with the detergent
used with the machine.
If necessary
proceed with the replacement of the
damaged hoses.
9.3.3
Clean Water Filter
Check
(to perform every
2h
)
The filter has a great importance, be-
cause its knob allows the opening of the
solution tank valve.
The filter has to be periodically cleaned
and it is also important to check that it
is intact and has no anomalies.
9.3.3-2
9.3.4
Water Pump
Check
(to perform every
50h
)
The water pump has to block completely
the solution flow when the brush deck
is not working. Viceversa it has to grant
the flow rate when the brush deck is
working.
9.3.4-3
9.3.5
Distributor
Check
(to perform every
50h
)
The distributor has to be intact and has
to grant the proper solution flow without
any leakage in the gearbox.
9.3.5-4
49