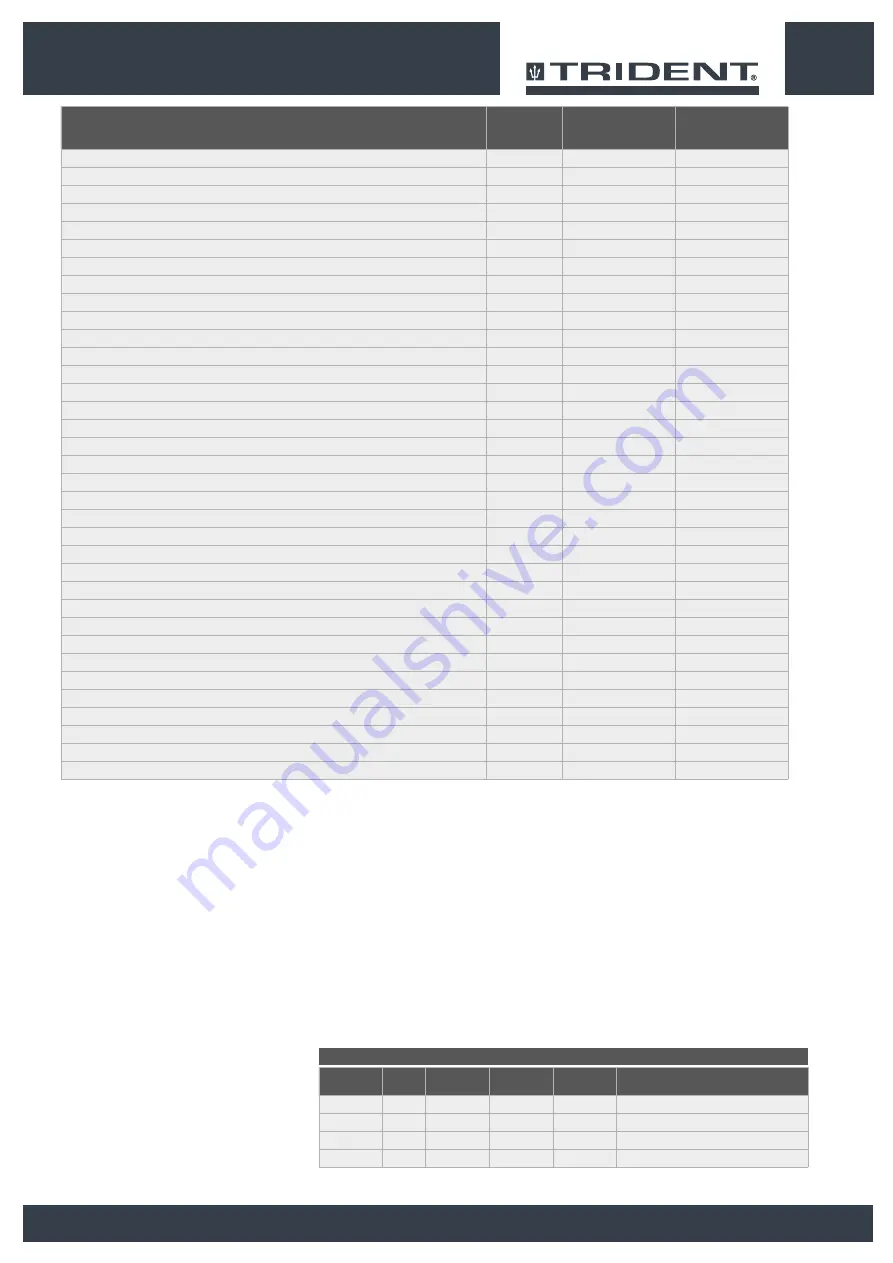
Remarks:
(1) Machine weight: refers to the overall weight of the machine; without the battery box; with no
operator on board, and with both tanks empty.
(2) Machine weight during transport: refers to the overall weight of the machine; with the battery
box inserted; with no operator on board, and with both tanks empty.
(3) Machine weight during work operations: refers to the overall weight of the machine; with the
battery box inserted; with addition of 70kg operator on-board; with the solution tank full; with
the detergent canister full; with the safety kit fitted.
BRUSH TYPE
CODE
QTY
Ø
EXTERNAL
LENGTH
TYPE OF
BRISTLE
NOTES
447963
2
Ø7.9in
33.7in
PPL 0.6mm
CENTRAL BRUSH
447964
2
Ø7.9in
33.7in
PPL 0.9mm
CENTRAL BRUSH
447965
2
Ø7.9in
33.7in
ABRASIVE
CENTRAL BRUSH
437874
2
Ø17.8in
-
PPL 1mm
SIDE BRUSH
13
TECHNICAL DATA
SI
[KMS]
TRIDENT R36
SS PLUS
TRIDENT R36
SS 2SL PLUS
Rated machine power
W
3050
3230
Working capacity up to
ft
2
/h
53820
53820
Working width
in
32.5
48.2
Working width with the lateral brush
in
-
41.3
Squeegee width
in
41.1
41.1
Central brush head brushes (number -Ø external bristles-length)
Nr - (Ø in - in)
2 - (Ø 7.9 - 33.7)
2 - (Ø 7.9 - 33.7)
Central brush head motor (voltage - nominal power rating)
V - W
36 - 750
36 - 750
Rpm of the individual brush on the central brush head
rpm
550
550
Lateral brush head unit motor (voltage - nominal power rating)
V - W
-
36 - 90
Lateral brush head brush rotations
rpm
-
75
Side brushes (number -Ø external bristles)
Nº - in
-
2 - Ø17.7
Maximum weight exerted upon the central brush head
lb
132
132
Maximum weight exerted upon the lateral brush head
lb
11
11
Traction motor (voltage / rated power)
V - W
36 - 900
36 - 900
Maximum negotiable slope (“transport” working program and empty tanks)
%
18
18
Maximum speed (with transport program)
mph
5.6
5.6
Vacuum motor (voltage - nominal power rating)
V - W
36 - 650
36 - 650
Vacuum head vacuum (versions with one motor - versions with two motors)
PSI
(2.76 - )
(2.76 - )
Wand kit vacuum
PSI
-
-
Maximum solution tank capacity
gal
50
50
Maximum recovery tank capacity
gal
53
53
Maximum capacity of the detergent canister (versions with automatic detergent dosing system)
gal
4
4
Debris hopper volume
gal
-
-
Turning circle (without front bumpers it and without roof)
in
38.8
38.8
Machine dimensions (length - width - height)
in
72.4 - 42.7 - 54.1
72.4 - 42.7 - 54.1
Machine dimensions with front bumpers kit and roof (length - width - height)
in
74.6 - 42.7 - 76.8
74.6 - 42.7 - 76.8
Battery compartment dimensions (length - width - useful height)
in
37.8 - 15.7 - 19.9
37.8 - 15.7 - 19.9
Machine weight
(1)
lb
970
992
Machine weight during transport
(2)
lb
1.931
1942
Machine weight during work operations
(3)
lb
2635
2657
Weight of the front bumpers kit and roof
lb
139
139
Maximum weight of the battery box (recommended)
lb
917
917
Sound pressure level (ISO 11201) - L
pa
dB(A)
< 70
< 70
Uncertainty K
pa
dB(A)
1.5
1.5
Body vibration level (ISO 2631)
m/s
2
0.5
0.5