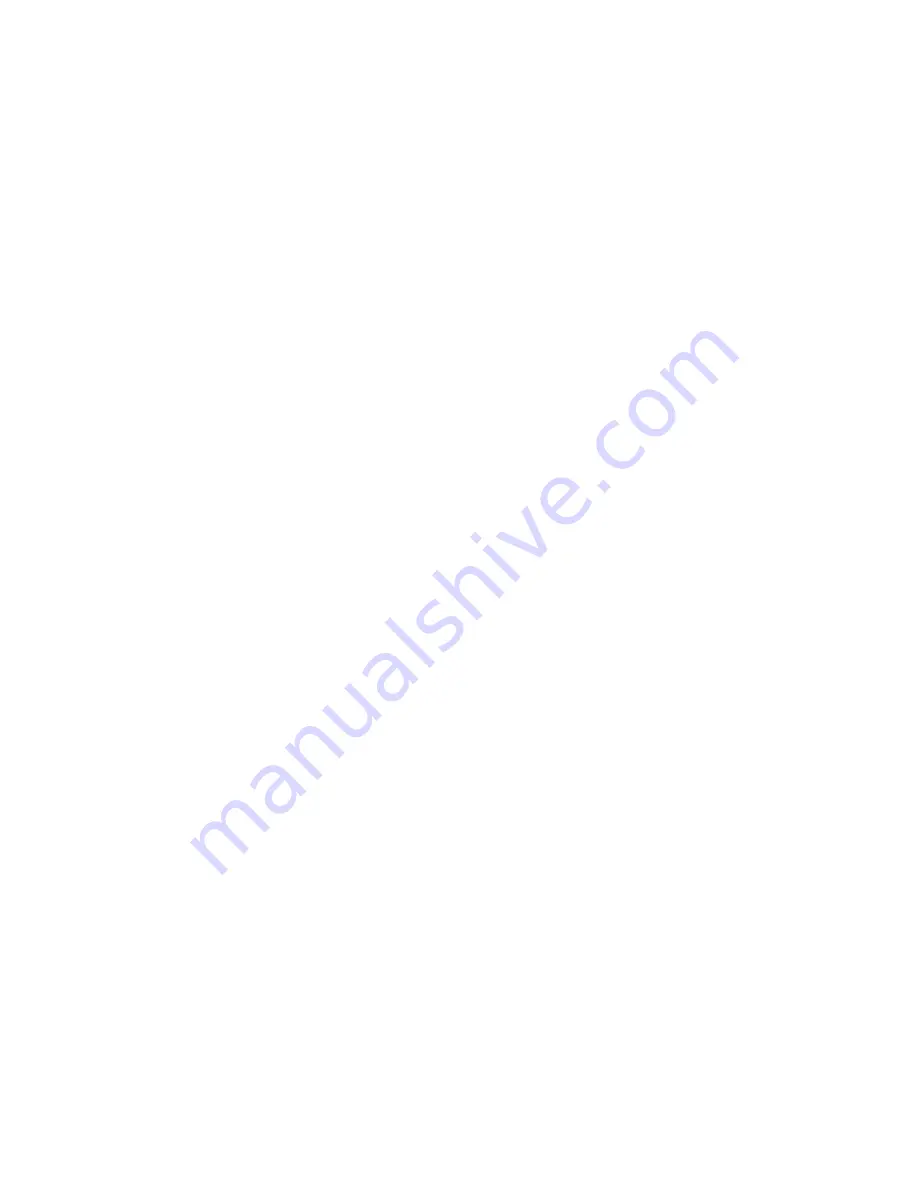
62
That one cyclic servo rod moves downwards and the other upwards does not matter. As a result, only the swash plate
remains at its predetermined height.
However, you can not take the table values for this because, in the case of cyclic moves, the swash plate does not slide
up and down parallel to the rotor shaft, but makes a pivoting movement about its center point.
As a result, the difference between the different link ball positions between the inner ring and the outer ring results in a
requirement.
That means the cyclic deflection on the blade grip is smaller than a collective one with the same tooth rack stroke.
Just calculate with the following values: 1mm toothed rack stroke is approx. 1.6 ° cyclic blade adjustment.
Now you only need to divide the required value by the degree and get the stroke to be set.
Example: 8 ° is required (so the tooth rack stroke would be 8 °: 1.6 ° = 5mm stroke).
For the measurement, give a pure aileron cyclic input without a elevator or collective pitch, then the one aileron servo rod
moves downwards by 5mm and at the same time the other aileron servo rod moves 5mm upwards.
At its height, the swash plate remains unchanged in its position.
Finally, you usually have to program the cyclic maximum values and limit them by a software cyclic-ring.
The FBL- system ensures that when the cyclic input of aileron and elevator cames at the same time, the deflection does
not become too great since both values add up. With this function, the swash plate always maintains the same maximum
angle, no matter which direction you swing it.
This prevents mechanical boundary transitions.
In any case, activate this function, if this is not already the case automatically. Set your cyclic maximum values in the
swash plate neutral position so that the reciprocating stroke does not exceed 10mm at the same time with a combined
cyclic full aileron and elevator input.
However, close to the maximum collective pitch values, these values are then no longer achieved, but this does not
matter.
After setting up in the operating mode, move the swash plate to the maximum values of all conceivable combined vertices
to see if it mechanically jammed anywhere.
At the same time, carefully turn the rotor head from the top to the right (clockwise) to check whether there is any tension
on the linkage in any position.
Of course, you can also make the whole setup with a classic pitch gauge, taking care that the helicopter is standing stable
and that the blades are really at 0 ° when the swashplate is at the neutral position.
This must be done in any case at the latest now, if everything else is set so far anyway.
It is precisely with such a stiff system, that the tracking differences have a particularly negative effect on the flight
performance.
Place the TDF on a flat, non-slip support and install the main rotor blades.
Align the blades as accurately as possible and place the rotor head in a position along the helicopter so that one blade is
above the tail tube. Then calibrate your pitch gauge on a reference surface on the helicopter, which is at right angles to
the rotor plane, e.g. the engine cover.
The gauge should be placed as accurately as possible along the helicopter lateral axis, before setting it to zero. Turn the
display screen towards the helicopter tip, because you can then also carry out the measurement on this side, namely on
the rotor blade, which looks to the front.
Then attach the balance to the rotor blade and adjust the value of the linkage to zero. To do this, always pull off the
linkage at the the swash plate to adjust it.
Again, you do not need to try long, but can calculate. The M2.5 thread of the link rod has a pitch of 0.45mm. This means
that the smallest possible adjustment, namely a half turn of the ball joint, causes a change of 0.225 mm. This corresponds
to a difference of approx. 0.5 degrees.
In the worst case, this will reach 0.25 ° to your desired destination, which is quite sufficient. Try to get this on the other
blade as well. However, your new value should correspond to the already set blade and not the previous desired value,
since the absolute dimension is not decisive, but the equality of both blades is important.
To set the zero pitch, do not use this questionable method, where the rotor blades are turned through 90 ° in the blade
holders so that the tips are positioned as indicators.
This can perhaps be done with a helicopter of the 450 size, with the blades much shorter and lighter, but not with a
machine of the 700size class. The leverage forces acting on the swash plate are poison for the linkages, the ball joints
and the servos.
Also, this type of measurement is not correct.