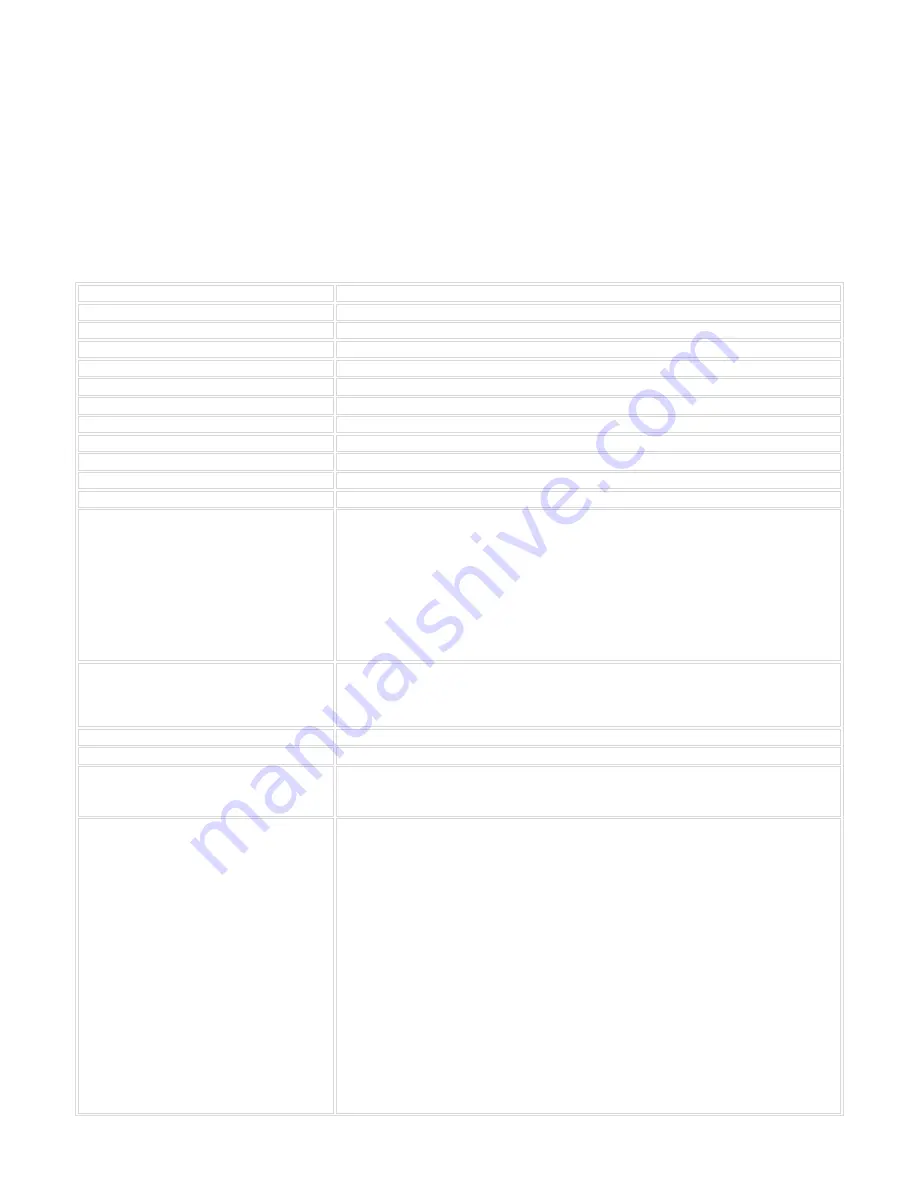
Some parts of the
TDF
loyal Henseleit customers will know from the TDR and the TDR-II. So the canopy is the same as it
is for TDR, as this design is still nice and aero dynamic - with good visibility - nothing to improve. A new decal design
changes the view, but also the old design can be used if wished. TDR-II design has to be modified a bit, but can than also
be used. TDR customers can also use there existing canopies - it fits without changes.
The approved main rotor of TDR II has been modified for 12mm main rotor shaft and 8 mm feathering spindle, to save
weight. The adjustable damping was implemented - so adjustments can be done on the field in seconds.
Technical Data:
Name
TDF
(
T
ree
D
ee
F
un)
Manufacturing and sales
Henseleit Helicopters
Main rotor diameter
up to 1600 mm
Rotor blades
680 - 720 mm
Recommended rotor blades
710 mm / 175 - 210 g
Tail rotor blades
up to 110 mm carbon blades
Empty weight of the mechanic
approx 1800 g
Total weight - depending on used components 3.6 - 4.8 kg
Total length - tip of canopy to end of tail
1390 mm
Total height
390 mm
Maximum width of skits
190 mm
Maximum width of canopy
140 mm
Recommended motor
PYRO 650
– 78 (6S setup)
PYRO 650
– 65 (7S / 8S setup)
PYRO 700
– 52 (for 10S)
PYRO 700
– 45 (for 12S)
Maximum motor PYRO 750
– 45 Competition (for 12S)
Recommended ESC
JIVE PRO 120+ HV
KOSMIK 160+HV depending on motor and flight syle (recommended only for PYRO 750
motors)
Gear ratio main rotor to tail rotor
1 : 5,56 (tail rotor is running during auto rotation)
Gear ratio motor to main rotor
9,27 : 1
Maximum flight pack size (L x W x H)
340 mm x 60 mm x 62 mm
When using 6S or 7S, the flight pack should be a weight of minimum 800 g.
Recomended servos and some general things
In gereral al standard servos can be used, but the
TDF
can also be flown with mid size servos
due to his weight and Linear Drive System, as 80 Ncm torque is more than enough.
Normally these servos are only half in weight of standard ones - so a total saving of about 160
g is possible.
Important is, tha there is no play in the servo and that the are precise in finding and holding
their position.
The enormous torque of up to 300 Ncm, the manufacturers are beating each other, I believe in
substantial exaggerating. Servos with more than 150 Ncm using in this helicopters are not
useful.
Even with 3 midi size servos the swash plate is pushed with nearly 25 kg (2 ½ baskets of
water).
Considered that the rotor blade with cyclical input and 1800 RPM on the main rotor change
from one side to the other about 30 times a second - you can imagine that the forces cannot
be as high, as the stud bolts would not stay in the plastic ball link if the force would be as high.