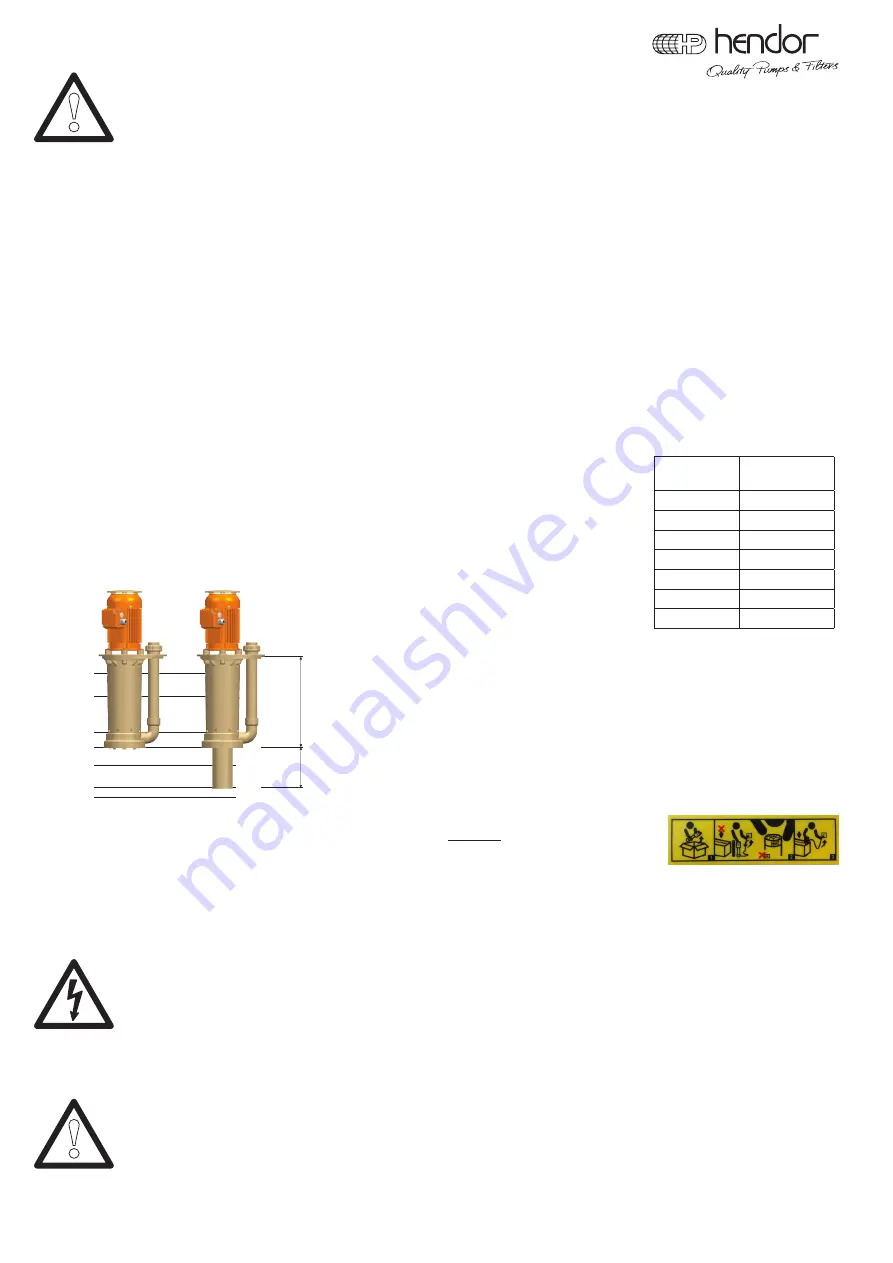
!
© Hendor - Quality Pumps & Filters
- 3 -
Info 2016715/R0
3.3 Checking direction of rotation
Vertical pumps:
Always check the direction of rotation
outside
the liquid.
Horizontal pumps:
Always check the direction of rotation
flooded
with liquid.
Briefly switching on the power will show direction of rotation, looking at cooling fan side. Ignoring these recommendations could
damage the pump severely.
3.4 Plumbing
1. Connections to the pump and filter should be provided with reliable, persistent and chemical resistant materials.
2. Where hoses are used, take care of using correct hose clamps.
3. Use the right elastomers when making the connections.
4. Pipes and hoses should be internally cleared of any obstructions.
5. Check tightness of connections to prevent leakage and spills before starting up.
6. Thermoplastic pump components do not tolerate any plumbing stress.
7. Plumbing should be properly aligned and supported to prevent distortion and damage of parts.
8. Leave enough space around the pump or filter for easy access and maintenance.
9. Keep location of the pump away from any heaters or heater coils.
10. Pumps and filters should be mounted on a sturdy base.
3.5 Polution
Solids and mud are harmful for pumps. There are suitable strainers available to keep these substances out of the pump.
4.1 Vertical pumps
4.1.1 Installation
Take notice of enough bottom clearance at the suction side of vertical pumps.
See recommendations for bottom clearance.
Hendor vertical pumps are designed for in-tank installation.
Out-of-tank models are optional and require special installation instructions.
Ensure that the pump is connected correct to the power supply and
that the plumbing is fitted leakfree.
1 maximum liquid level
2 normal working level
3 minimum starting level
4 pump A stops pumping
5 pump B will continue to work
(if it is not switched off)
6 pump B stops pumping
7 bottom
tank
4.1.2 Operation and maintenance
At start up the pump should be
checked for direction of rotation OUTSIDE
the liquid (see label on pump).
Contaminated strainers (if mounted) can reduce performance and should be cleaned regularly.
Regular pump inspection
During operation all pumps should be checked regularly. Check flow, pressure, manometer indication, pipe work, hoses, hose clamps and
absorbed power by monitoring amperage of the motor. Pumps should be fitted with thermal overload switch. Check pumps for any unusual
noise or vibration (this may indicate the moment of maintenance).
Maintenance precautions
To avoid dangerous or fatal electric shock hazard and to avoid injury from starting the motor unexpectedly, disconnect and lock
out power supply to the motor. Always use genuine parts to assure good performance. When taking pump apart check for
sequence of disassembly and reassembly. After having completed maintenance or repair, follow safety and installation
instructions.
4.1.3 Dismantling and reassembly
For efficient maintenance of Hendor vertical pumps, some
special tools
are available (see page 5).
General precautions prior to dismantling
- always disconnect electric cables.
- disconnect discharge pipe.
- clean pump and remove remaining liquid in pump housing.
- do work on a clean bench.
When ordering Hendor parts always quote
serial number, pump type
and
drawing position number of the required part
.
!
Type
Minimum bottom
distance (mm)
D90
50
D110
55
D120
55
D160
25..100
D18
65
D20
100
D24
100
Immersion
length
(mm)
Suction
extension
B
A
1
2
3
4
5
6
7
max.
min.