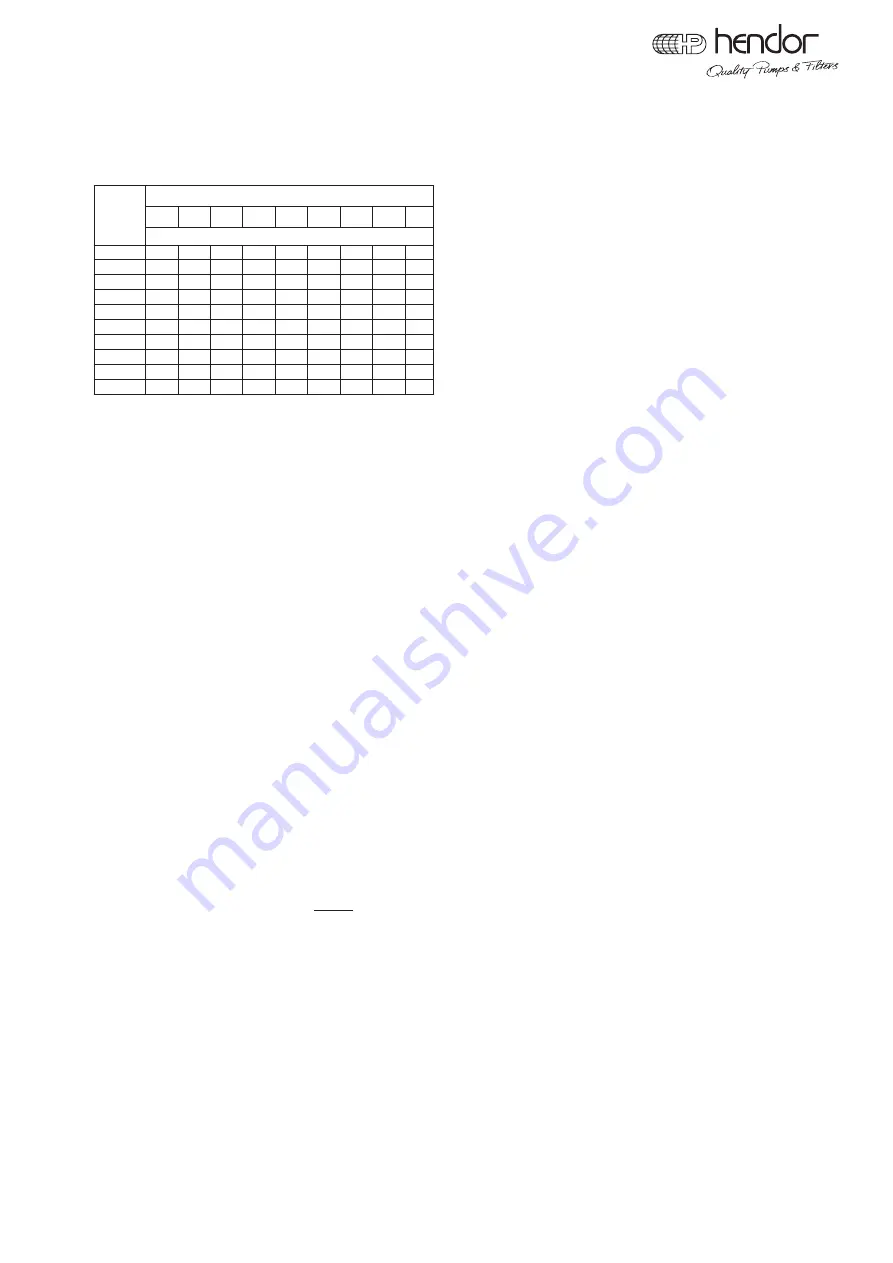
© Hendor - Quality Pumps & Filters
- 6 -
Info 2016715/R0
4.2 Horizontal Pumps
4.2.1 Installation
Horizontal magnetic drive & seal pumps are very sensitive to suction conditions. Often pump problems are caused by poor suction
conditions. The bigger the pump and the higher the temperature, the more important the general hydraulic guidelines should be applied.
Always try to respect the basic rules for liquid velocity v (m/s) and NPSH.
We recommend for Suction side v = 1 - 2 m/s; Discharge side v = 1,5 - 3 m/s
Flow (l/h)
Inner pipe diameter (mm)
15
20
25
32
40
50
65
80
100
Velocity (m/s) at given flow (l/h)
1000
1,57 0,88 0,57
2000
3,15 1,77 1,13 0,69
4000
6,29 3,54 2,26 1,38 0,88
6000
5,31
3,4
2,07 1,33
8000
4,53 2,76 1,77 1,13
10000
5,66 3,46 2,21 1,42 0,84
15000
5,18 3,32 2,12 1,26 0,83
20000
6,91 4,42 2,83 1,68 1,11
30000
10,4 6,63 4,25 2,51 1,66 1,1
40000
8,85 5,66 3,35 2,21 1,4
Golden rules for proper pipe work
1. Keep suction pipe as short as possible.
2. Increase pipe size on suction side by at least one pipe diameter for longer suction pipe and/or higher temperature.
3. Use eccentric adaptors at varying diameters to prevent air pockets.
4. Avoid elbows, bends and fittings at suction side. When unavoidable keep fittings at a distance of 10 times pipe diameter away
from pump inlet.
5. Pipe work should slope up towards pump to prevent air pockets.
6. Pipe work should be completely leak free.
7. Support pipe work near to pump to prevent stress on plumbing.
8. Allow sufficient liquid level to prevent air intake on suction side.
9. Use generously oversized strainer in case of foreign particles.
10. Use siphon breaker when priming over top of tank.
11. Never throttle pump on suction side.
12. In case of doubt consult Hendor for proper sizing and NPSH calculation.
4.2.2 Operation and maintenance
Magnetic drive pumps. How it works?
Driver (motor) and impeller (driven) are physically separated by a shell.
Pump part (wet end) is completely sealed and therefore isolated from plating proces.
Power transmission is established by magnetic force between motor shaft and impeller.
Bearings are lubricated and cooled by liquid itself.
Mechanical seal pumps. How it works?
Impeller is directly attached to the motor shaft by shaft coupling.
Mechanical seal on pump shaft prevents liquid from coming out.
Mechanical seal is lubricated and cooled by liquid itself.
These type of pumps are not self priming and not designed to run dry or hot. Optional priming chambers and dry run protection devices
are available.
Initial start-up
Priming instructions at
flooded suction
:
1. Open all valves on suction and discharge side.
2. The pump should always be flooded with liquid to prevent any damage on bearings.
3. These type of pumps are not self priming. Therefore liquid level in the bath should be ample above entrance level of the pump.
4. Check for direction of rotation before start-up by shortly switching on/off.
5. Start the pump when no air remains in the pump.
6. When pumping liquid with higher density than water, start up with almost closed discharge valve to reduce power consumption.
Priming instructions at
non flooded suction
:
1. Ensure entrance of suction pipe is in liquid.
2. Slowly fill pump casing and suction pipe. Use discharge connection to fill.
3. Check if pump is free of air.
4. Close discharge valve and check for direction of rotation before start-up by shortly switching on/off.
5. Start the pump.
6. Wait until pump is building up pressure, and slowly open discharge valve.
Restart after power failure: Check if the pump is able to prime again. Suction pipe and pump housing should be filled.
Contaminated strainers (if applicable) can reduce flow, therefore: clean strainers regular.