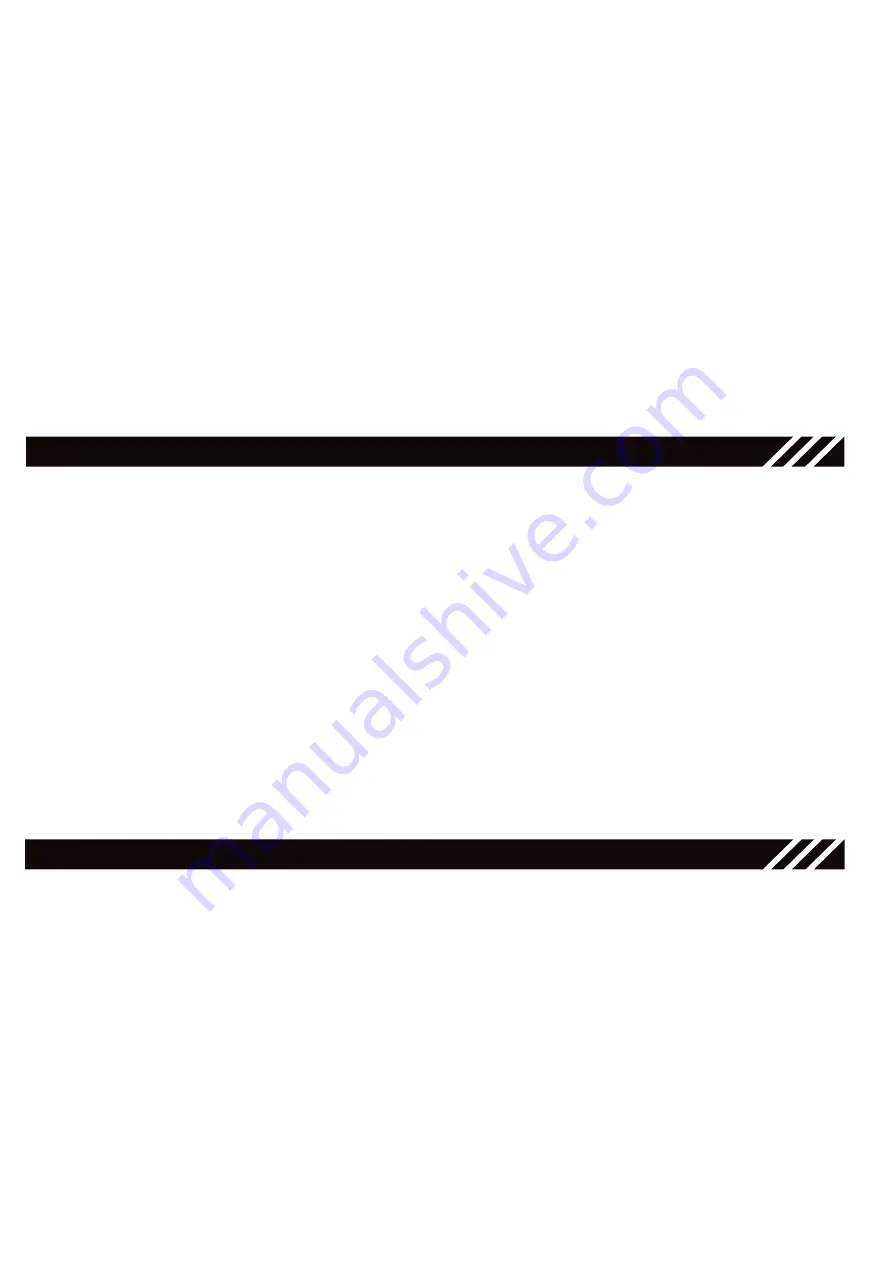
EN-10
8.0
PROTECTION GASES GUIDE
METAL
Mild steel
Aluminium
Stainless steel
Copper, Nickel and
Alloys
GAS
CO2
Argon + CO2
Argon + CO2 + Oxygen
Argon
Argon + Helium
Argon + CO2 + Oxygen
Argon + Oxygen
Argon
Argon + Helium
NOTE
Argon controls spatters
Oxygen improves arc stability
Arc stability, good fusion and minimum
spatter.
Higher heat input suitable for heavy
sections. Minimum porosity.
Arc stability.
Minimum spatter.
Suitable for light gauges because of low
flowability of the weld pool.
Higher heat input suitable for heavy sections.
Contact the technical service of your gas supplier to know the percentages of the different
gases which are the most suitable to your application.
9.0
WELDING HINTS AND MAINTENANCE
•
Always weld clean, dry and well prepared material.
•
Hold gun at a 45° angle to the workpiece with nozzle about 5 mm from the surface.
•
Move the gun smoothly and steadily as you weld.
•
Avoid welding in very drafty areas. A weak pitted and porous weld will result due to air blowing away
the protective welding gas.
•
Keep wire and wire liner clean. Do not use rusty wire.
•
Sharp bends or kinks on the welding cable should be avoided.
•
Always try to avoid getting particles of metal inside the machine since they could cause short circuits.
•
If available, use compressed air to periodically clean the hose liner when changing wire spools
IMPORTANT: Disconnect from power source when carrying out this operation.
•
Using low pressure air (3/5 Bar=20-30 PSI), occasionally blow the dust from the inside of the wel-
der. This keeps the machine running cooler. Note: do not blow air over the printed circuit board and
electronic components.
•
The wire feed roller will eventually wear during normal use. With the correct tension the pressure
roller must feed the wire without slipping. If the pressure roller and the wire feed roller make contact
(when the wire is in place between them), the wire feed roller must be replaced.
•
Check all cables periodically. They must be in good condition and not cracked.
1.
Wire feeder Slope-Up Time (Min. to Max. speed transition time), adjustable with the poten-
tiometer located inside the access panel (16).
2.
At the end of the the Slope-Up Time, the wire feed speed reaches the value adjusted with the
Left knob (8).
•
To stop welding, release the trigger. The arc stays ON accordingly to the set B.B.T. (Burn back time).
B.B.T. is the amount of time that the weld output continues after the wire stops feeding. It prevents the
wire from sticking in the puddle and prepares the end of the wire for the following arc start.
7.4 ALUMINUM WELDING
The machine needs to be set up as follows:
•
100% ARGON as welding protective gas.
•
Ensure that your torch is set up for aluminum welding:
1.
The lenght of the torch should not exceed 3m (it is advisable not to use longer torches).
2.
Install a teflon wire liner (follow the instructions for the replacing of the wire liner).
3.
Use contact tips that are suitable for aluminum wire and make sure that the diameter of the contact
tip hole corresponds to the wire diameter that is going to be used.
•
Ensure that drive rolls are suitable for aluminum wire.
Summary of Contents for TP 195
Page 3: ...III 8 0 SCHUTZGAS ARTEN D 10 9 0 SCHWEISSWISSEN D 10 10 0 FEHLERSUCHE D 11 ...
Page 4: ...IV ...
Page 41: ...V Figure 8 ...
Page 43: ...VII ...
Page 44: ...VIII 77613015 ...