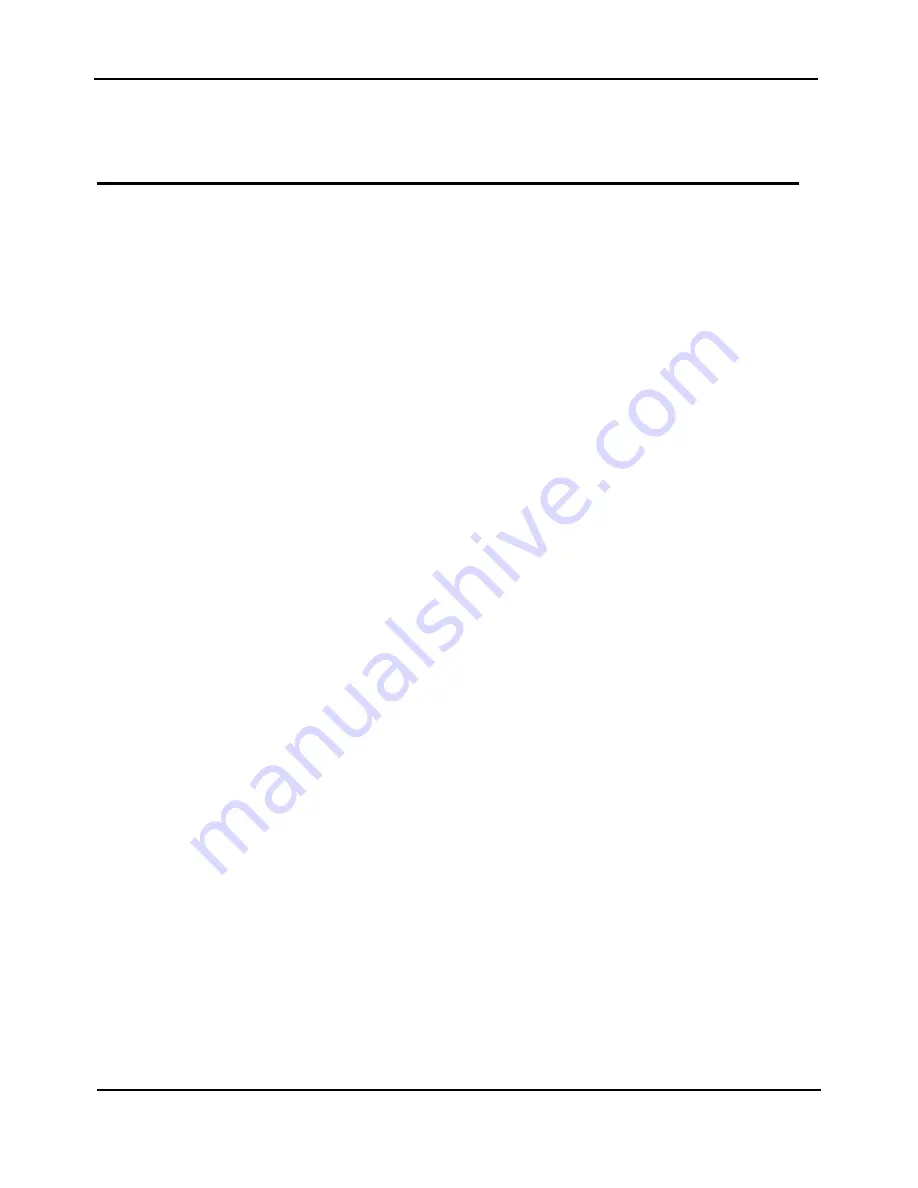
OPERATING INSTRUCTIONS TREND SERIES
PROBLEM
POSSIBLE
CAUSE
REMEDY
No front panel indications
Fuse blown.
Power source.
Replace fuse.
Check power.
Display flashes zeroes.
Instrument turned off/on with function
switch in Monitor Parts position.
Reset instrument by turning function
selector to Standby/Clear.
Bypass/Clear LED flashing.
Meter display off.
Monitor/Calibrate switch (inside door)
in calibrate position.
Set switch to Monitor (left) position.
Trend lights do not change.
Meter does not display SPM or
Tolerance settings.
Function switch in Bypass position.
Turn function switch to Monitor Parts
to activate auto-timing for Strokes per
minute.
High or Low Tolerance Alarms do not
stop press.
Tolerance settings in OFF position.
Select tolerances from 5% to 45% to
activate tolerance alarms.
Alarms will not reset.
Function selector in Monitor
Parts/Reset not Active.
Possible open gage wire.
Turn function keyswitch to Reset
Active.
Check strain gage wiring and
connections.
Tolerance alarms stop machine
before tolerance setting is reached.
Capacity alarms settings have been
activated.
Check Capacity Alarm Sets.
Reset capacity alarms if required.
Alarms are fired or monitor tries to
sample when machine is not running.
Strain Gain wires are run in conduit
with high voltage wires.
Route sensor wires in separate
conduit.
Display will not zero or unusual
numbers are displayed.
Switches on individual channel boards
are improperly set.
Move all channel board switches to
forward position.
Display does not zero when RESET
button is pressed.
Normal condition in Monitor Parts
position. Display will zero only when
resetting alarm condition.
With function switch in Standby, peak
load display is reset. In Monitor Parts,
display is not reset when RESET is
pressed.
Meter display off. Press/Machine will
not run.
Instrument turned off/on with function
switch in Monitor parts position.
Check power.
Reset instrument by turning function
switch to Standby/Clear then to
Monitor Parts.
TREND alarms lit, machine machine
continues to run.
Top stop wires are jumped out or
press is being operated in inch mode.
Check wiring. Operate in run mode.
T
Summary of Contents for Trend Loadgard TLG2300
Page 26: ...OPERATING INSTRUCTIONS TREND SERIES A...
Page 27: ...OPERATING INSTRUCTIONS TREND SERIES B...
Page 28: ...OPERATING INSTRUCTIONS TREND SERIES C...
Page 29: ...OPERATING INSTRUCTIONS TREND SERIES D...
Page 32: ...OPERATING INSTRUCTIONS TREND SERIES G...
Page 33: ...OPERATING INSTRUCTIONS TREND SERIES H...
Page 35: ...OPERATING INSTRUCTIONS TREND SERIES J Appendix C TLG 8000 Operation Guidelines...
Page 36: ...OPERATING INSTRUCTIONS TREND SERIES K Appendix C TLG 8000 Operation Guidelines...
Page 39: ...OPERATING INSTRUCTIONS TREND SERIES N...
Page 40: ...OPERATING INSTRUCTIONS TREND SERIES O...
Page 41: ...OPERATING INSTRUCTIONS TREND SERIES P...
Page 42: ...OPERATING INSTRUCTIONS TREND SERIES Q...
Page 43: ...OPERATING INSTRUCTIONS TREND SERIES R...