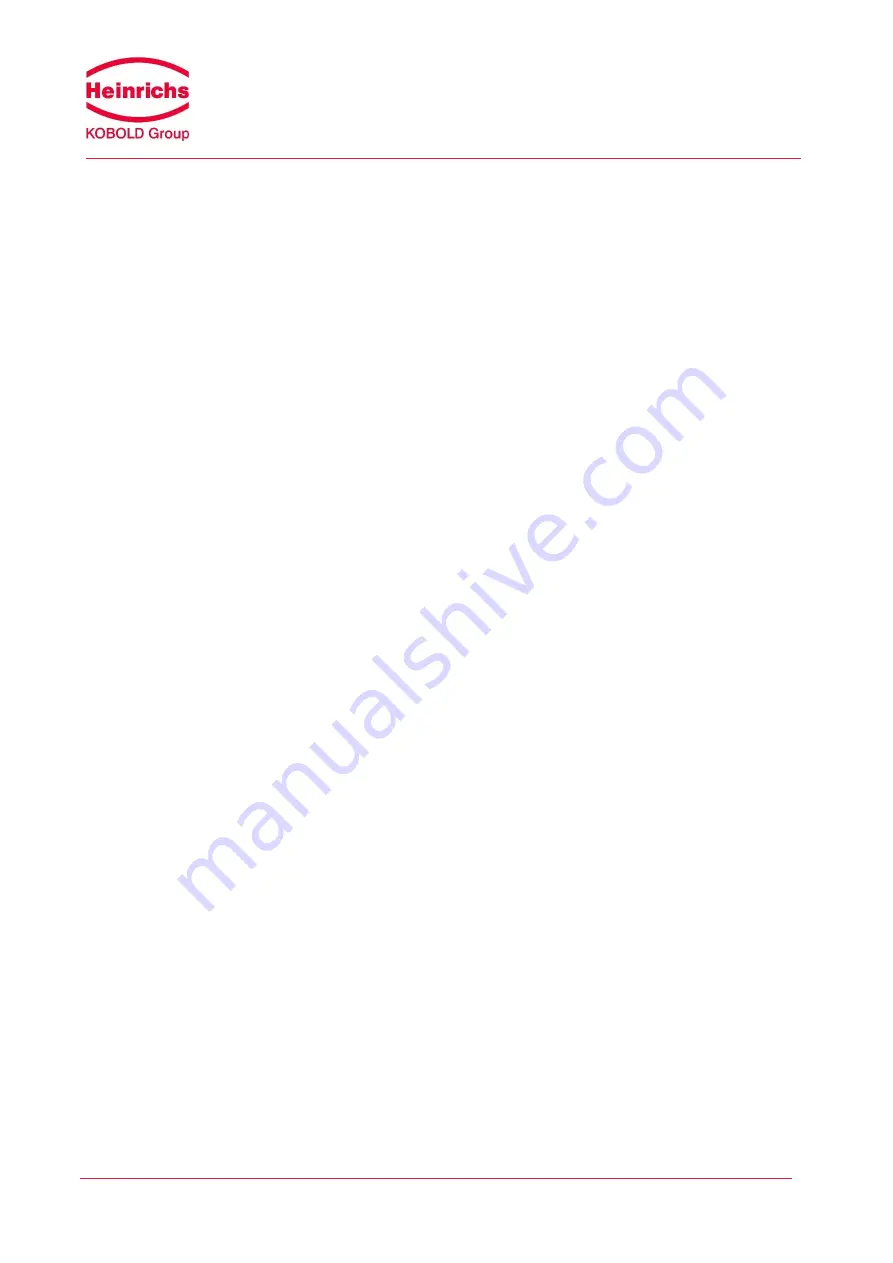
Heinrichs Messtechnik GmbH
Page 20 of 31
Ex-Supplement operating manual
UMC4 with TM/TMU/TME/TMR/TM-SH
operation at temperatures above 220 °C may lead to an accelerated deterioration insulation materials
and thus a reduction in the sensors life span.
5.3
Requirements for installation in all environments
a)
The installation of the intrinsically safe circuits requires a control drawing (system description), to be
issued by the operator/erector.
b)
The equipment is only to be installed and connected in a de-energized state.
c)
The sensor is to be installed (from specialists) according to applicable regulations.
d)
When mounted separately (remote mount configuration), equipotential bonding between the sensor
and transmitter must be ensured
e)
It is to be insured that the intrinsically safe circuits of the sensor cable are not laid together with non-
intrinsically safe circuits.
f)
If the sensor is used at an ambient temperature of less than -20 °C or greater 60 °C, suitable cables,
cable entries and conduit entries are to be used.
g)
The operational wall thickness of the stainless steel flow tubes may be < 1 mm. In this case, the
operator is to ensure that in the area of these tubes, no risk of damage by the process medium or
through mechanical influence shall occur.
h)
Although the measuring tubes are in constant oscillation, the deflection of this oscillation is
significantly smaller (< 1 mm) than the materials stress levels allow and thus presents no addition
requirements for protective measures.
i)
The sensor may be used in such a way that in the measuring tubes an explosive atmosphere may be
present occasionally or for a long period of time.
j)
Seized screws or adhering joints (e.g. by frost or corrosion) are not to be opened with force when the
presence of a potentially explosive atmosphere is considered possible.
k)
Where substances of explosion group “A” or “IIC” are present and the presence of an Ex
-atmosphere is
considered possible, only non-sparking tools shall be used.
l)
The electrical connections from the sensor to the junction box are made by means of a connection
flange. Care must be taken to guarantee the IP protection class.
5.4
Ex relevant screw and bolt torques
Potential Equalisation fixation
6 Nm
Nuts sensor-neck/J-box
6 Nm
Screws J-box lid (Aluminium)
2 Nm
Screws J-box lid (Polyester)
1.2 Nm
Cable glands to J-box adapter
12 Nm
Cable gland caps
8 Nm