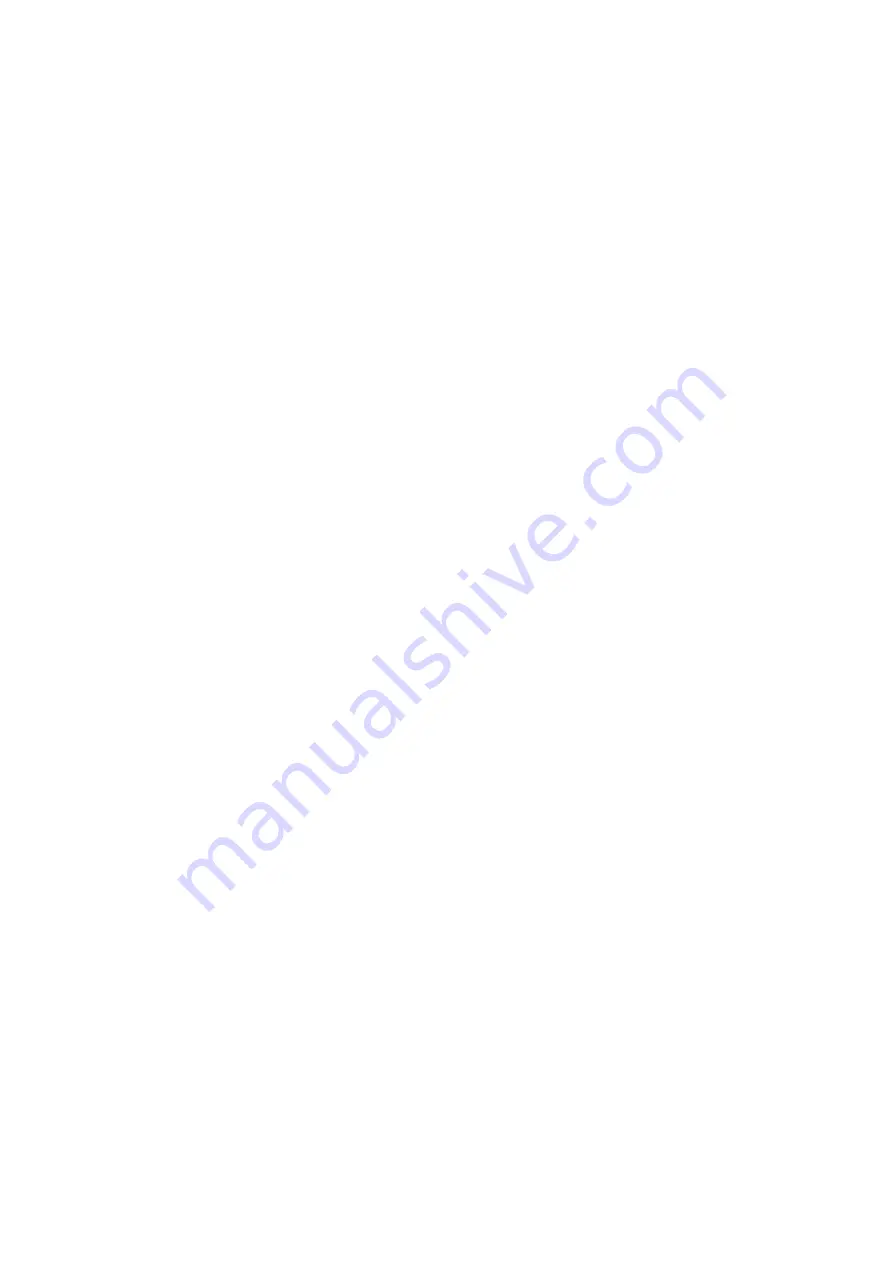
15
Confi guration
The EnDat interface makes it possible
to set various functions regarding data
transmission or the general operation
of the encoder. The various EnDat words
for setting functions are located in
the “operating status” or “operating
parameters” memory areas. The settings
are normally saved and need only be made
once.
Operating status
Function initialization
Recovery time:
10 µs
•
†
t
m
†
30 µs selectable to 1.25 µs
†
t
m
†
3.75 µs (for mode commands no.
8 to 14 and f
C
> 1 MHz)
Reduced recovery time is set when very
•
short cycle times are to be attained.
Multiturn functions:
Makes the connection of battery-
•
buffered encoders possible.
Reference pulse initialization:
Only with incremental encoders for
•
fi nding the optimal reference mark
position
The following functions are reserved for
future applications and therefore cannot
yet be set:
Oversampling, diagnostics reset
•
EnDat 2.2 cyclic operation I/O, statuses of
•
touch probes, referencing of incremental
encoders can be switched off
Write-protection
The customer can write-protect the OEM
parameters (“electronic ID label”) and/or
the operating parameters (e.g. datum shift).
Operating parameters
Zero point shift
This function is called “electronic datum
setting” and enables the customer to fi t
the encoder datum to the datum of the
application.
Confi guration of diagnostics
This EnDat word activates the desired
valuation numbers for transmission of
diagnostic information.
Recommendation: All available valuation
numbers should be activated to ensure the
maximum depth of information on the
encoder’s function reserves.
Address assignment and instructions
Reserved for future bus operation through
the EnDat interface.
Threshold sensitivity to temperature
Specifi cation of a temperature threshold
at which the encoder transmits a warning
to the subsequent electronics. The
temperature is derived from the encoder’s
internal temperature sensor
Cycle time
Setting the cycle time with which the
higher-level control transmits EnDat
requests. Reserved for future applications.
HEIDENHAIN offer various aids for
implementing the EnDat interface in
subsequent electronics (see also
“Implementation” section under
www.EnDat.de
):
EnDat Demotool software
As its hardware basis, the EnDat Demotool
software needs a PWM 20 (IK 215 is
possible, but not recommended). The
EnDat Demotool software supports you
when implementing the EnDat interface:
Communication with EnDat encoders on
•
the basis of mode commands
Logging of EnDat command sequences
•
Provides a reference when integrating of
•
the EnDat master into the control loop
EnDat master
The EnDat master controls communication
with EnDat encoders from HEIDENHAIN.
It allows simple transmission of position
data and additional data to the higher-level
application. The EnDat master can be
integrated by means of a micro controller
(µC) or an FPGA (Field Programmable Gate
Array) or ASIC.
The µC solutions are used if the intended
clock frequencies are relatively low.
Integration in an FPGA or ASIC is chosen
primarily for high transmission frequencies
with pure serial data transfer. Several
variants are available for integration in
an FPGA or ASIC.
EnDat master, standard
•
EnDat master, safe
•
EnDat Master, reduced
•
EnDat Master, light
•
Documentation
EnDat Specifi cations
•
EnDat 4
•
EnDat Seminar
•
FAQ and implementation at
•
www.EnDat.de
EnDat
•
Technical Information
Description of the EnDat master
•
component at
www.mazet.de
Implementation of EnDat