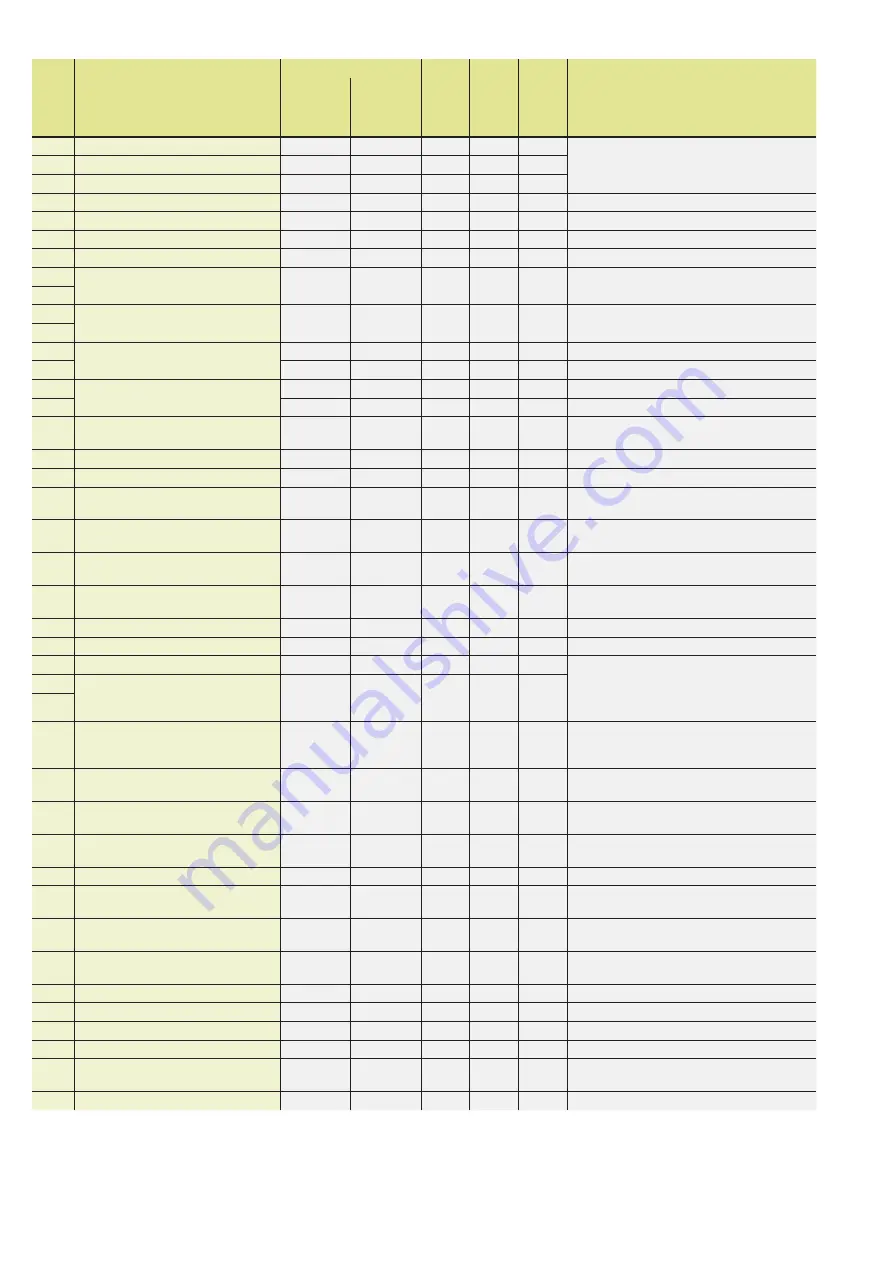
12
Parameters of the encoder manufacturer for EnDat 2.2
Unit
for
Requir
ed
Depends on
application
Inf
or
mativ
e
Word
Contents
Linear
encoder
Rotary/
angle
encoder
Remark
0
Status of additional data 1
–
–
–
All
–
Can be safety related.
Cross checking of “what is required” and
“what does the encoder support”
1
Status of additional data 2
–
–
–
All
–
2
Status of additional functions
–
–
–
All
–
3
Acceleration
m/s
2
1/s
2
–
All
–
Consider the scaling factor
4
Temperature
K
K
–
All
–
Consider the scaling factor
5
Diagnostic status
–
–
–
–
All
–
6
Support of error message 2
–
–
All
–
–
For defi nition of an “error mask” (safety related)
7
Dynamic sampling status
–
–
–
All
–
Safety technology
8
9
Measuring step or measuring steps
per revolution for position value 2
nm
–
–
All
–
Safety technology
10
11
Accuracy of position value 2 depending
on linear velocity or shaft speed, area I
LS
1)
LS
1)
–
All
–
Safety
technology
12
LS
1)
LS
1)
–
All
–
Safety
technology
13
Accuracy of position value 2 depending
on linear velocity or shaft speed, area II
LS
1)
LS
1)
–
All
–
Safety technology
14
LS
1)
LS
1)
–
All
–
Safety technology
15
Distinguishable revolutions Position
value 2 (only for multiturn encoders)
–
–
W D
–
–
Required for correct calculation of the position
16
Direction of rotation of position value 2
–
–
All
–
–
–
17-20
Encoder designation
–
–
–
–
All
–
21
Support of instructions
–
–
–
–
–
Not yet supported.
Not for safety technology
22
Max. permissible encoder temperature
at measuring point
K
K
–
W L D
IL i
–
Not supported by
E
23
Max. permissible acceleration
m/s
2
1/s
2
–
W L D
IL i
–
Not supported by
E
24
Number of blocks for memory area
section 2
–
–
All
–
–
Depends on encoder; program fl exibly.
25
Maximum clock frequency
kHz
kHz
All
–
–
Depends on connector, cable lengths
26
Number of bits for position comparison
–
–
–
All
–
Safety technology
27
Scaling factor for resolution
–
–
All
–
–
For calculation of the smallest display step (LS).
28
Measuring step, or measuring steps
per revolution or subdivision values of
a grating period
–
–
All
–
–
29
30
Max. velocity or rotational shaft speed
for constant code value
m/min
min
–1
–
W L D
IL i
–
Specifi c to application. Applies for encoders
that permit higher mechanical than electrical
speed. (Not supported by the EIB.)
31-33
Offset between position value and
position value 2
–
–
–
All
–
Safety technology
34
“Number of distinguishable
revolutions” with scaling factor
–
–
W D
–
–
Required for correct calculation of the position
35
Support of operating status error
sources
–
–
–
All
–
Expanded EnDat error message, particularly for
battery-buffered encoders
36-38
Safety-relevant measuring steps
–
–
–
All
–
Safety technology
39-40
Non-safety-relevant subdivision of the
relative position
–
–
–
All
–
Safety technology
41-42
Non-safety-relevant subdivision of the
absolute position
–
–
–
All
–
Safety technology
43
Generation of a warning message
through limit position signals
–
–
–
L IL
–
Presently available only with certain
incremental exposed linear encoders
44
Support of touch probe statuses
–
–
T
–
–
Supported features
45
Timestamp unit of measure
–
–
T
–
–
–
46
Referencing of incremental encoders
–
–
–
IL, Ir, E
–
Is re-referencing supported?
47
Support of I/Os
–
–
–
All
–
Are I/Os supported, and if so, which?
48
Number of OEM blocks for memory
area section 2
–
–
–
All
–
The memory area section 2 makes larger
OEM memory possible
63
CHECKSUM
–
–
–
–
–
–
1)
The higher-valued byte contains the divisor with respect to the maximum permissible linear velocity or rotational shaft speed up to
which this accuracy is valid.