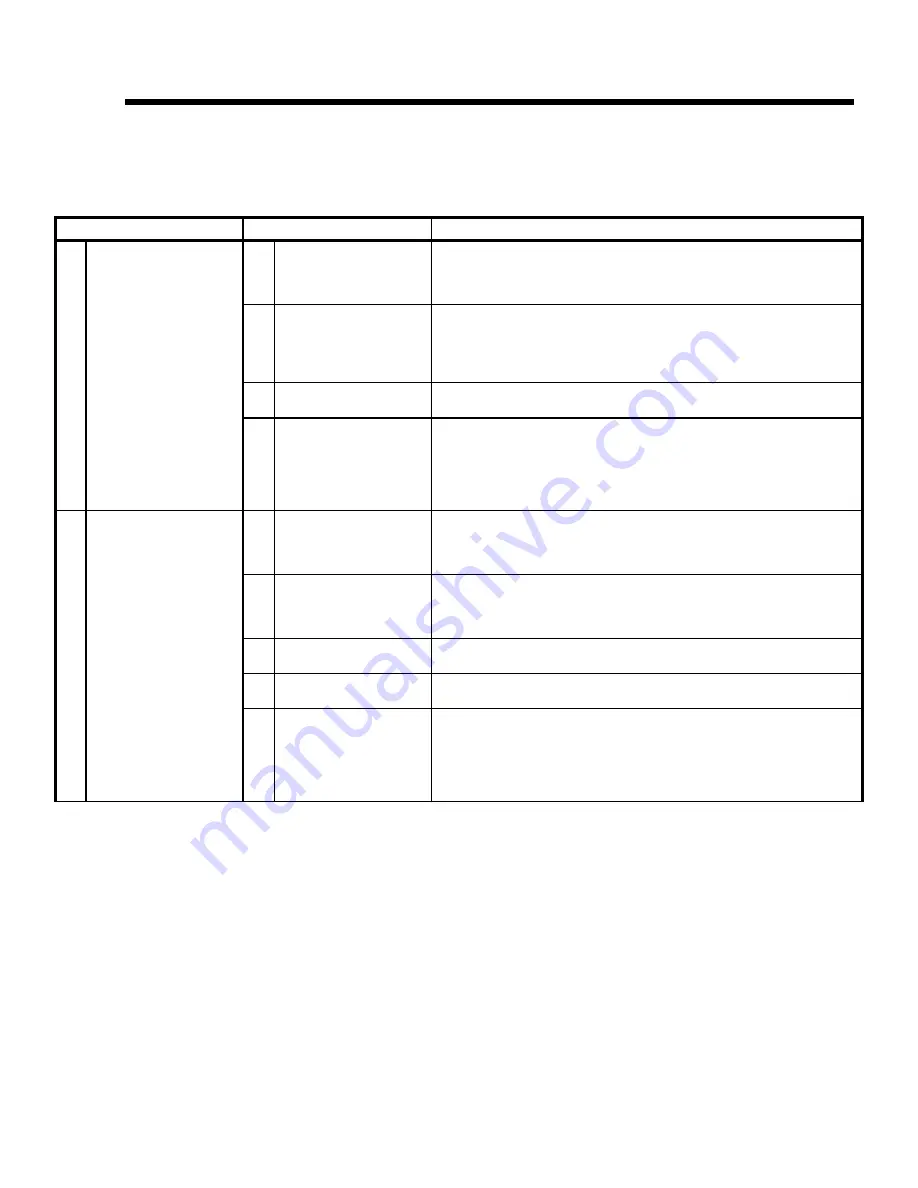
Heatilator • Caliber CNXT Series • 4047-132 Rev P • 11/07
59
With proper installation, operation and maintenance your gas appliance will provide years of trouble-free service. If you do
experience a problem, this troubleshooting guide will assist a quali
fi
ed service person in the diagnosis of a problem and the
corrective action to be taken. This troubleshooting guide can only be used by a quali
fi
ed service technician.
14
14
Troubleshooting
Intelli
fi
re Ignition System
Symptom
Possible Causes
Corrective Actions
1.
The ignitor/module makes
noise, but no spark.
A.
Incorrect wiring.
Verify “S” wire (white) for sensor and “I” wire (orange) for ignitor are
connected to the correct terminals on the module and the pilot assembly.
Reversed wires at the module may cause the system to make a sparking
noise, but the spark may not be present at pilot hood.
B.
Loose connections or
electrical shorts in the
wiring.
Verify there are no loose connections or electrical shorts in wiring from
module to pilot assembly. The rod closest to the pilot hood should be ignitor.
Verify connections underneath pilot assembly are tight; also verify the
connections are not grounding out to the metal chassis, pilot burner, pilot
enclosure, mesh screen if present, or any other metal object.
C.
Ignitor gap is too large.
Verify gap of ignitor to pilot hood. The gap should be approximately .17 in. or
1/8 in.
D.
Faulty module.
Turn ON/OFF rocker switch or wall switch to OFF position. Remove ignitor
wire “I” from module. Place ON/OFF rocker switch or wall switch in ON
position. Hold ground wire about 3/16 in. away from “I” terminal on module. If
there is no spark at “I” terminal, module must be replaced. If there is a spark
at “I” terminal, module is
fi
ne. Inspect pilot assembly for shorted sparker wire
or cracked insulator around electrode.
2.
Pilots won’t light, there is
no noise or spark.
A.
Transformer installed
correctly.
Verify that transformer is installed and plugged into module. Check voltage of
transformer under load at space connection on module with ON/OFF switch
in ON position. Acceptable readings of a good transformer are between 3.2
and 2.8 volts AC.
B.
A shorted or loose
connection in wiring
con
fi
guration or wiring
harness.
Remove and reinstall the wiring harness that plugs into module. Verify there is
a tight
fi
t. Verify pilot assembly wiring to module. Remove and verify continuity
of each wire in wiring harness.
C.
Improper wall switch
wiring.
Verify wall switch is wired correctly.
D.
Module not grounded.
Verify black ground wire from module wire harness is grounded to metal
chassis of appliance.
E.
Faulty module.
Turn ON/OFF rocker switch or wall switch to OFF position. Remove ignitor
wire “I” from module. Place ON/OFF rocker switch or wall switch in ON
position. Hold ground wire about 3/16 in. away from “I” terminal on module. If
there is no spark at “I” terminal module must be replaced. If there is a spark at
“I” terminal, module is
fi
ne. Inspect pilot assembly for shorted sparker wire or
cracked insulator around electrode.
Summary of Contents for CNXT4236IH CNXT4842IH
Page 88: ...88 Heatilator Caliber CNXT Series 4047 132 Rev P 11 07 This page intentionally left blank...
Page 89: ...Heatilator Caliber CNXT Series 4047 132 Rev P 11 07 89 This page intentionally left blank...
Page 90: ...90 Heatilator Caliber CNXT Series 4047 132 Rev P 11 07 This page intentionally left blank...