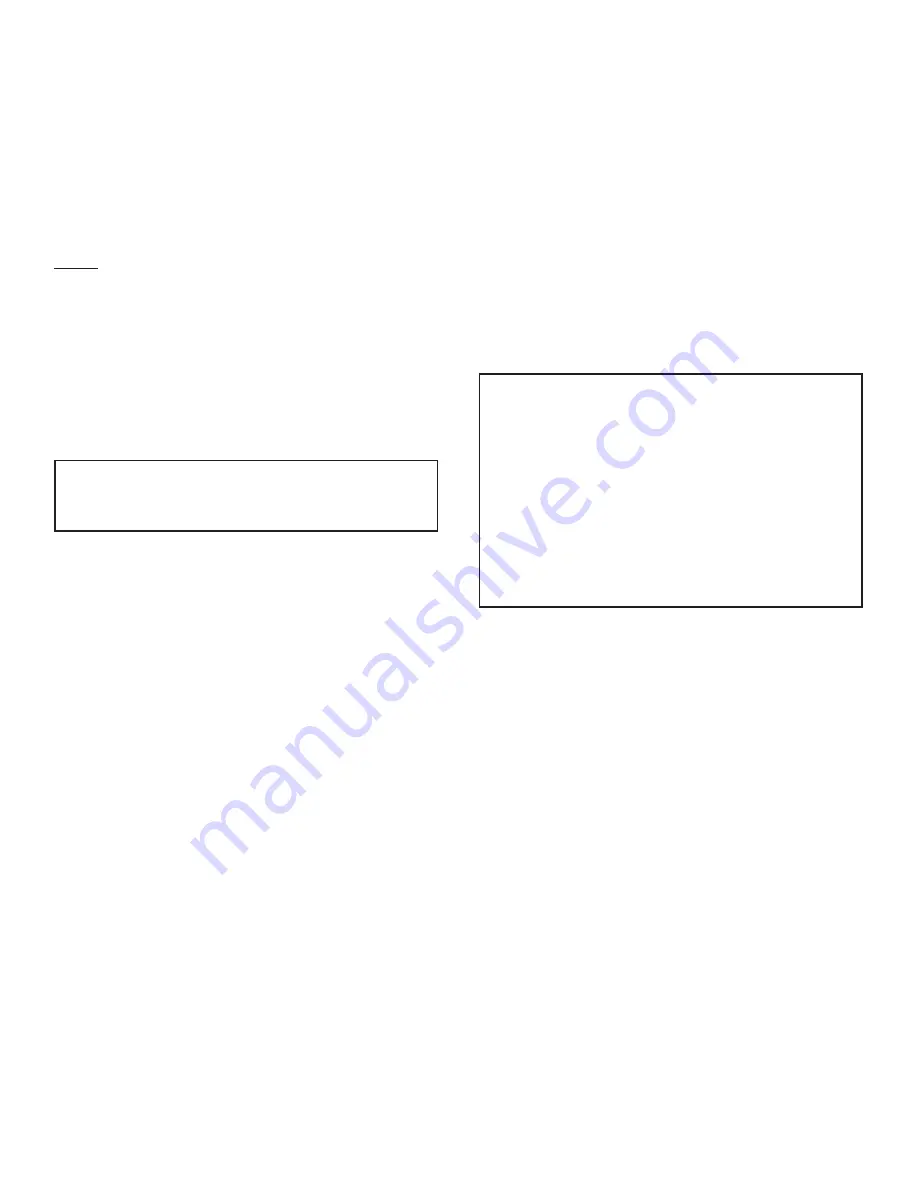
Heatilator • AVEO Series DV • 4058-210 Rev P • 1/13
17
B. Design and Installation Considerations
Heatilator direct vent gas appliances are designed to op-
erate with all combustion air siphoned from outside of the
building and all exhaust gases expelled to the outside. No
additional outside air source is required.
Installation MUST comply with local, regional, state and
national codes and regulations. Consult insurance carrier,
local building inspector, fi re offi cials or authorities having
jurisdiction over restrictions, installation inspection and
permits.
Before installing, determine the following:
• Where the appliance is to be installed.
• The vent system confi guration to be used.
• Gas supply piping.
• Electrical wiring requirements.
• Framing and fi nishing details.
• Whether optional accessories—devices such as a fan,
wall switch, or remote control—are desired.
D. Inspect Appliance and Components
• Carefully remove the appliance and components from
the packaging.
•
The vent system components and decorative doors and
fronts may be shipped in separate packages.
• If packaged separately, the log set and appliance grate
must be installed.
• Report to your dealer any parts damaged in shipment,
particularly the condition of the glass.
•
Read all of the instructions before starting the installation.
Follow these instructions carefully during the installation
to ensure maximum safety and benefi t.
C. Tools and Supplies Needed
Before beginning the installation be sure that the following
tools and building supplies are available.
Tape measure
Framing material
Pliers
Flat blade screwdriver
Hammer Phillips
screwdriver
Gloves Framing
square
Voltmeter
Electric drill and bits (1/4 in.)
Plumb line
Safety glasses
Level Reciprocating
saw
Manometer
Non-corrosive leak check solution
1/2 - 3/4 in. length, #6 or #8 Self-drilling screws
Caulking material (300ºF minimum continuous expo-
sure rating)
One 1/4 in. female connection (for optional fan).
Hearth & Home Technologies disclaims any responsibility for,
and the warranty will be voided by, the following actions:
• Installation and use of any damaged appliance or vent system
component.
• Modifi cation of the appliance or vent system.
• Installation other than as instructed by Hearth & Home
Technologies.
• Improper positioning of the gas logs or the glass door.
• Installation and/or use of any component part not approved
by Hearth & Home Technologies.
Any such action may cause a fi re hazard.
WARNING! Risk of Fire, Explosion or Electric Shock!
DO NOT use this appliance if any part has been under wa-
ter. Call a qualifi ed service technician to inspect the appli-
ance and to replace any part of the control system and/or
gas control which has been under water.
Improper installation, adjustment, alteration, service or
maintenance can cause injury or property damage. For
assistance or additional information, consult a qualifi ed
service technician, service agency or your dealer.
WARNING! Risk of Fire or Explosion!
Damaged parts
could impair safe operation. DO NOT install damaged, in-
complete or substitute components. Keep appliance dry.