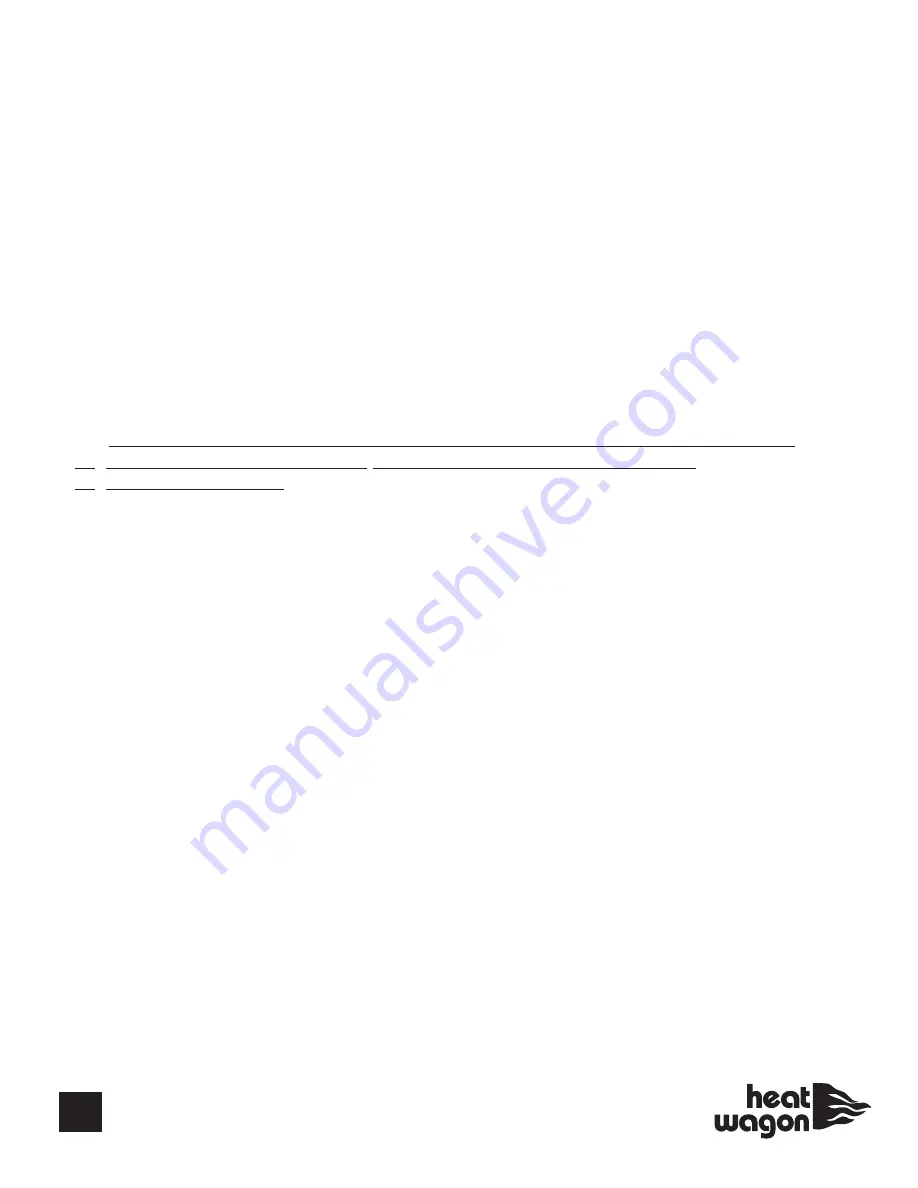
SAFETY & CAUTION
• Instructions given in this manual and the applicable regulations of the local authorities
must be followed.
• The unit may be operated only by those persons who have been instructed in its proper use.
• The unit is to be installed and operated in such a way as to ensure the safety of employees and
surroundings.
• Never cover the unit’s air openings.
• Always ensure adequate fresh air supply to the unit.
• Never stand in front of the discharge end of the heater.
• Keep a minimum clearance of 10 feet from the fuel source. Storing and use of liquid fuel must
comply with the regulations and instructions given by the local authorities.
• Unit’s emitted noise level at the range of 3 feet: 74 dBA.
• Do not introduce foreign objects into the unit.
• Do not expose the unit to direct water jets.
• All electric cables outside the unit are to be protected against damage.
• Always disconnect the unit from power supply and turn off the gas supply when maintenance
or service is being performed.
•
IF NOT OPERATED WITHIN GUIDELINES OF THESE OPERATING INSTRUCTIONS,
MANUFACTURER WILL NOT BE HELD RESPONSIBLE AND WARRANTY
WILL BECOME VOID
.
4
SPECIFICATIONS
Model No. VG500
Fuels: Vapor Propane or Natural Gas
Capacity: 500,000 BTU/HR
Blower: 6,475 CFM
2.05” W.C. SP
Electrical Rating: 240 Volts, 15 Amps
Fuel Consumption: NG-500 CFH / Propane-5.5 GPH, 1” FNPT Connection
Remote Thermostat: On/Off
Max. Discharge Temp.: 72ºF @ 0ºF Ambient
Duct Size: 21” Dia., 200 ft. max (straight), temp rating 300ºF min.
Shp. Dimensions: 90”L x 40”W x 60”H
Weight (approximate):
650 lbs.
Gas Supply:
Inlet Pressure Manifold Pressure
Max W.C. Min W.C. W.C.
Vapor Propane 14 W.C. 9” W.C. 3.6”
Natural Gas 14 W.C. 9” W.C. 6.1”
Summary of Contents for VG500
Page 16: ...16 Burner Parts List ...
Page 17: ...17 Burner Parts List ...
Page 18: ...Piping Connections Cartridge Assembly 18 ...
Page 19: ...19 240 Volt 1 PH ...