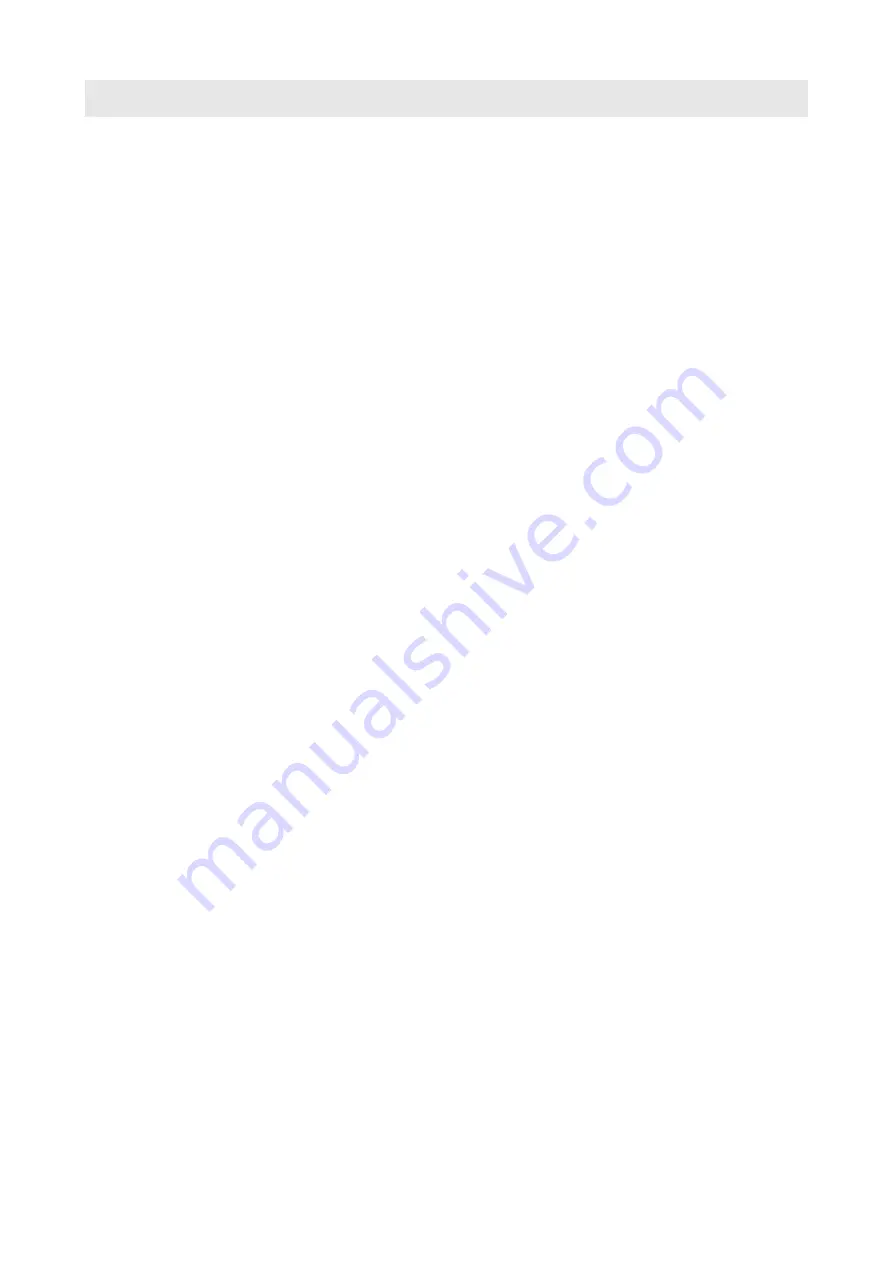
HB-TP180/200
Checking Facility for Temperature Control Units
General
6
O8354-EN 2018-11
1 General
1.1 Information about this manual
After reading this manual, the operator will be able to safely and
efficiently handle the checking facility for temperature control units.
The manual is an integral part of the checking facility for
temperature control units and must always be kept close to the
checking facility for temperature control units and readily
accessible for personnel. Before starting any work, the personnel
must have carefully read and understood this manual. A basic
requirement for safe work is the observance of all safety and
handling instructions in this manual.
Furthermore, the local accident prevention regulations and general
safety regulations are valid for the application area of the checking
facility for temperature control units.
Illustrations in this manual are for basic understanding and may
deviate from the actual design.
We reserve the right to make technical modifications in order to
improve usability.