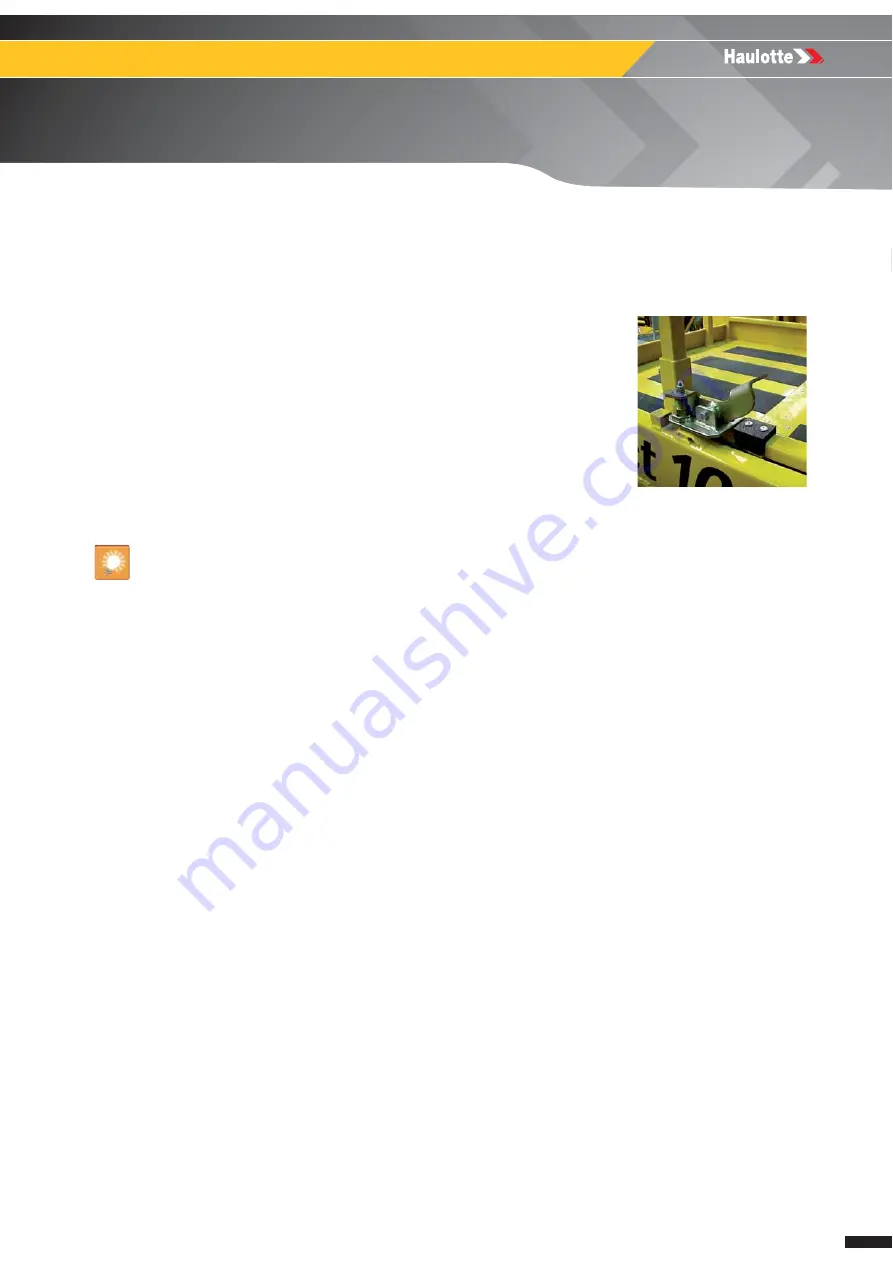
23
4001012670
E 06.20
USA / GB
Compact 8 (C 2032E) - Compact 8W (C 2047E) - Compact 10 (C 2747E) - Compact 10N
(C 2632E) - Compact 10N-1 - Compact 12 (C 3347E) - Compact 14 (C 3947E)
C -
Familiarization
1.3 -
MANUAL
EXTENSION
Machines are equipped with manual extension with several possible positions.
For : C8 (COMPACT 2032E) - C8W (COMPACT 2047E) - C10N (COMPACT 2632E) - C10
(COMPACT 2747E) - C12 (COMPACT 3347E) - C14 (COMPACT 3947E)
N.B.-:-D
O
NOT
LOAD
THE
EXTENSION
DECK
,
FOR
EASE
OF
MANOEUVRING
.
• Press the pedal.
• Push to the required notch.
The extension deck must be retracted and locked during transport or towing.
Summary of Contents for COMPACT 10
Page 48: ...48 4001012670 E 06 20 USA GB Control Filling up Oil tank M001 Notes ...
Page 58: ...58 4001012670 E 06 20 USA GB Replacement Hydraulic filter cartridge M003 Notes ...
Page 70: ...70 4001012670 E 06 20 USA GB Replacement Tightening Wheel M006 Notes ...
Page 72: ...72 4001012670 E 06 20 USA GB Lubrication Steering wheel pivots M010 Notes ...
Page 74: ...74 4001012670 E 06 20 USA GB Lubrication Guide rail M011 Notes ...
Page 76: ...76 4001012670 E 06 20 USA GB Lubrication Cylinder hinge M012 Notes ...
Page 80: ...80 4001012670 E 06 20 USA GB Hydraulics Hoses inspection Replacement MS0020 Notes ...
Page 82: ...82 4001012670 E 06 20 USA GB Electric Electrical wiring MS0025 Notes ...