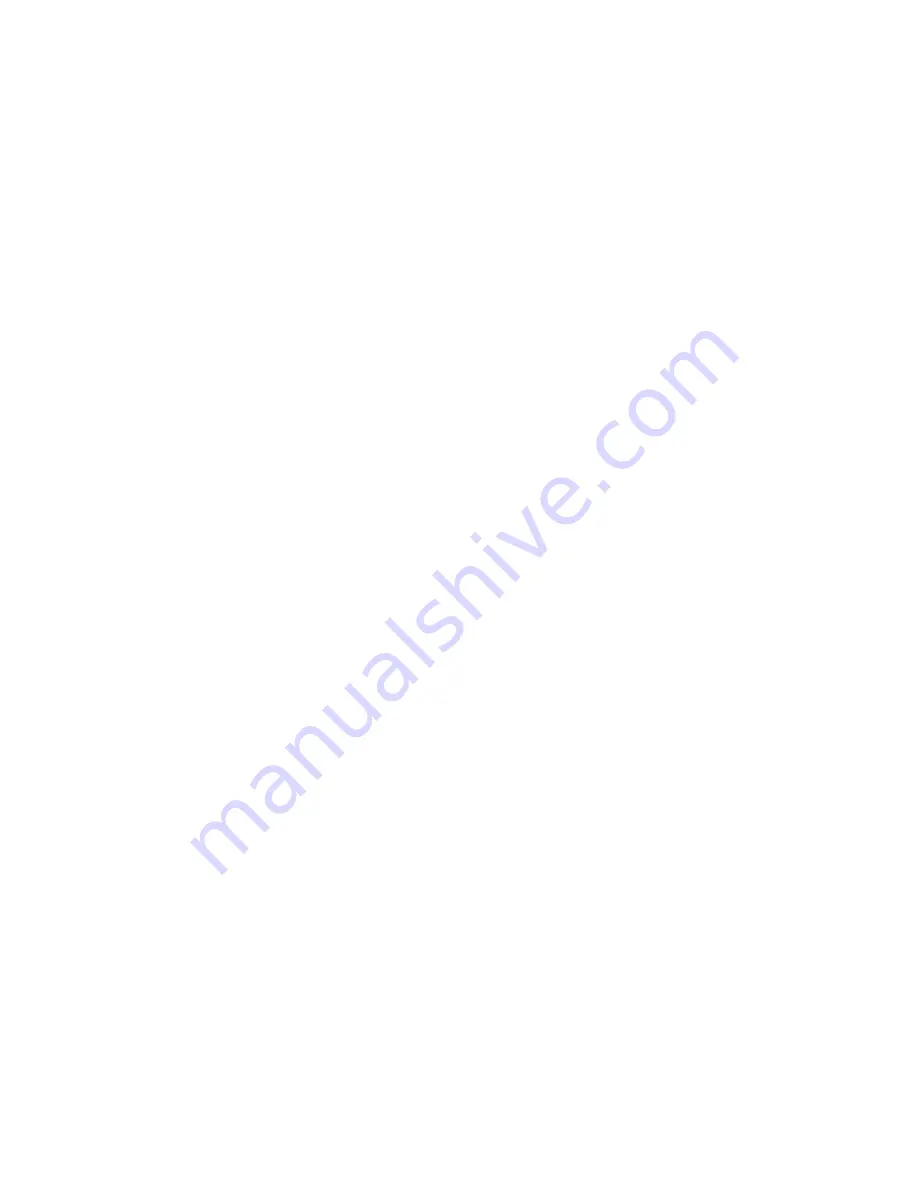
Wire Size Maximum Wire Length in Feet
16 ………………………………………………..160
14 ………………………………………………. 245
12 ………………………………………………. 395
j.
See Wiring diagram level referencing shielded cable for remote temperature dial connection.
10. Miscellaneous Installation Guidelines
a.
All sections not shipped attached must be assembled in the field by 1/4 – 20 x 5/8” sheet metal screws provided
in the cloth bag with each ship along section. See previous instructions – Important Notice to Equipment Users
– or follow general arrangement drawing provided for this unit to determine which items are crated and shipped
separately. Figure No. 1 through Figure No. 4 show typical unit assemblies.
b.
For outdoor or weather-proof models, a water-proof caulking is provided to seal all joints between optional sec-
tions as they are bolted together. Perimeter caulking on each ship along section must be completed to insure a
water tight unit.
c.
If filter section is used, bolt to appropriate section by sheet metal screws provided. Provide caulking as re-
quired. Filters and filter spacer(s) (if required) will be shipped installed in filter rack wherever possible. If filters
are shipped separately, install filters and filter racks (see filter maintenance for details). Filter spacer(s) will be
banded to filter channel where shipping necessitates filters going separately from filter section.
d.
If intake or discharge dampers are used, bolt to appropriate section with sheet metal screws provided. Provide
caulking as required. Re-connect conduit and wiring to damper motor(s) as required. Electrical wires for
damper motor(s) have been tagged for ease in connecting in the field.
e.
Vertical Unit Installation – see Figure No. 10.
All sections not shipped attached must be assembled in the field with splice channels and 1/2” bolts that are
provided. Models SB-112 through SB-218 are shipped with burner section and blower section assembled. LU
models are all produced with blower and burner in a common cabinet. Intake hood and birdscreen, filter sec-
tion, intake or discharge damper sections, or other large accessories are assembled, but shipped as individual
items.
Models SB-222 through SB-240 are shipped as separate sections.
All sections are shipped in a horizontal position. SB-112 through SB-218 has top mounting channel and base
channel shipped assembled with blower/burner section. SB-222 through SB-240 has top mounting channel
shipped as one section, but not physically attached to either blower or burner section – see Figure No. 10.
Unit base assembly is shipped separately for field connection to mounting channels and anchoring to floor. Op-
tional filter and/or inlet damper section(s) mount in base assembly – see Figures No. 11 and 12. All 1/2” bolts
and splice plates for unit assembly in the field are included with each unit.
The vertical SB and LU units are designed to simplify field installation. All parts have been designed in module
form to facilitate field installation of parts and accessories. The purpose of this manual is to supplement,
but
not to replace
the services of qualified field personnel to supervise the initial start-up and adjustment of vertical
SB and LU units. Persons without previous experience with large commercial and industrial make-up air equip-
ment should not attempt the initial adjustment and check-out procedure essential before such installations may
be considered as ready for operation
F. PRE-START INSPECTION
This inspection is extremely important and should be completed with greatest care given to detail. A good pre-start in-
spection will insure against possible unit damage on start-up and will save valuable analysis time in the event malfunc-
tions occur on start-up and check out.
1. Check to see that all factory installed plastic pipe plugs have been removed from gas valve inlet and any shipped
along gas pressure regulators and manual hand valves.
2. Make sure all field wiring and gas piping are in accordance with local and national codes.
3. Again, check supply voltage against unit voltage.
4. If an electric heating section is supplied, check supply voltage against element voltage.
5. Check all electrical connections in the main control panel and remote control panel.
6. Check that all fuses are installed and that fuse sizing agrees with the unit bill of material.
7. If optional steam, hot water, or chilled water coils are supplied, check to see that all piping connections are secure
and that face areas of coil(s) have not been damaged or blocked.
- 7 -
Summary of Contents for DIRECT GAS FIRED ELECTRIC STEAM
Page 13: ...H VALVE ADJUSTMENTS 11 ...
Page 22: ... 20 ...
Page 23: ... 21 ...
Page 24: ... 22 ...
Page 25: ... 23 ...
Page 26: ... 24 ...
Page 27: ... 25 ...
Page 28: ... 26 ...
Page 29: ... 27 ...
Page 30: ... 28 ...
Page 31: ... 29 ...
Page 32: ... 30 ...
Page 33: ... 31 ...
Page 34: ... 32 ...
Page 35: ... 33 ...