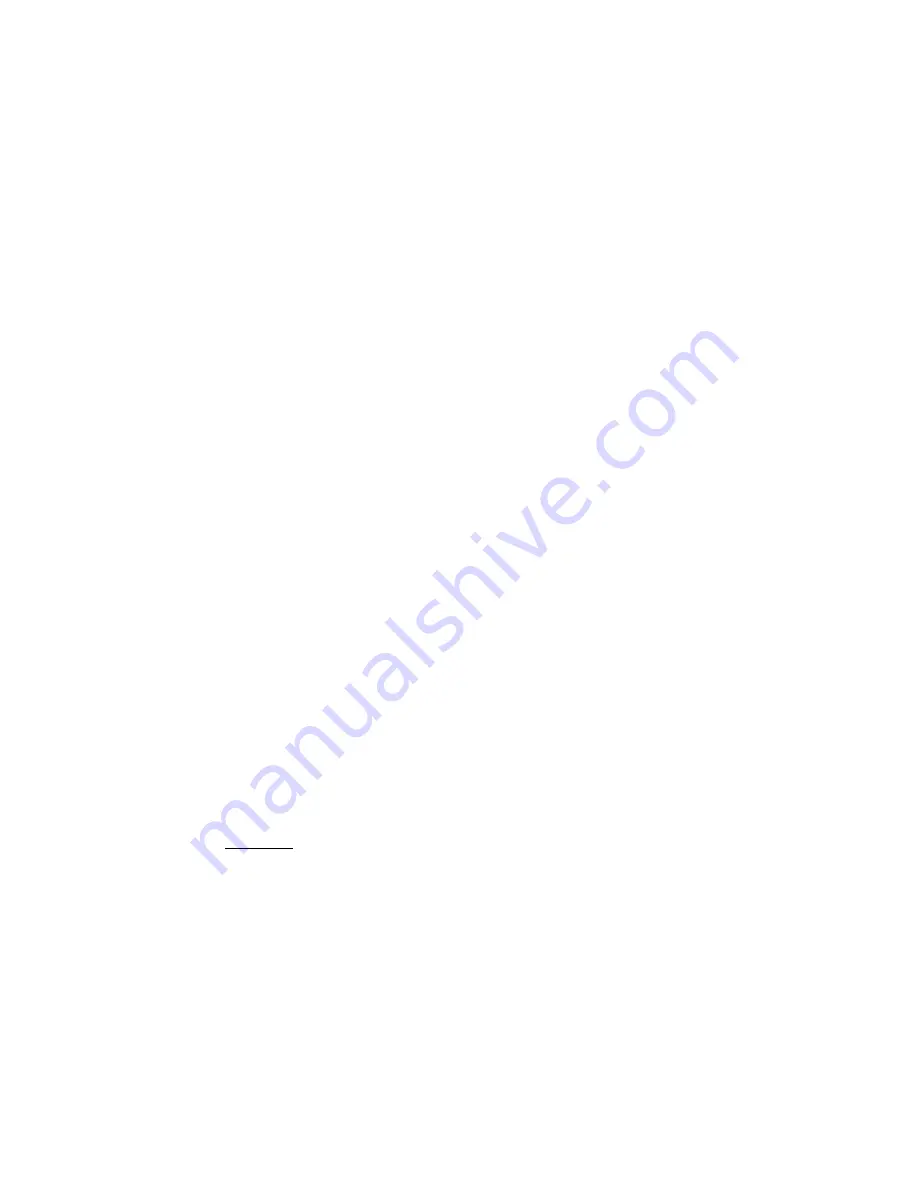
8.
Check to see if all gas connections are tight and that all joints have been properly lubricated.
9.
Check to see if all condensate drain piping has been completed (if required).
10.
Insure that all insulation is fastened securely to walls, ceiling, and floor areas.
11.
Check blower supply area to insure freedom of shaft rotation and proper belt tension - Remove any shipping
blocks and isolation support frame securing bolts (if ordered).
12.
Check blower motor to insure that pulleys are secure and drive belts are tight
13.
Check filters for cleanliness, and in the case of throw-away filters, make certain that they are free of moisture.
(Note: Wet filters will collapse under static pressure and the media will be sucked into the downstream sections
of the unit.)
14.
If any optional dampers are supplied, make certain that all dampers linkage is free to move and that no binding
will occur. If dampers are of the modulating type, check control capillary tubes to insure that the tubes will not rub
against any stationary objects.
15.
Check all areas for cleanliness.
16.
Secure all access doors.
17.
Check all canvas connectors (where used) between the unit and any duct work used.
18.
Instructions specify that service personnel shall perform a gas leak check during heater start-up, to verify the gas
tightness of the heater’s components and piping under normal operating conditions.
19.
Adequate instructions shall be provided for adjusting the pilot flame.
20.
Adequate instructions shall be provided for checking the gas tightness of the safety shut-off valve(s).
21.
Check blower shaft/coupler alignment on units with backward incline fans or split fan sets.
22.
Follow all list pre-checks prior to start-up as listed on factory start-up information form sent with equipment.
G. START-UP
All safety and operating controls have been checked during the factory test period, however, it is advisable to complete a
similar check when first operating the unit.
1.
Remove any shipping blocks from (gas units only):
a. High limit switch (if mercury bulb type) mounted on burner cabinet. Remove limit switch cover, remove paper
blocking, and tilt mercury bulb to reset.
b. Gas pressure switch(es) (if required) may have shipping screws. Remove screws if supplied.
c. Unit programming controller may be shipped with a paper shipping block. Remove programmer cover and
remove paper shipping block – re-install cover and adjust manual reset.
2.
Refer to heater rating plate for determining the minimum gas supply pressure for obtaining the maximum gas ca-
pacity for which this heater is specified.
3.
Prior to starting the heating sequence of the system, air needs to be purged from gas supply line up to the Hast-
ings equipment. CAUTION: The use of soap bubbles or an electronic leak detector is recommended to check for
leaks - Do not check for leaks with gas flame torch - Do not check for leaks with gas flame torch - Do not depend
on sensing the odor of gas to determine if the air has been purged from the gas line.
4.
The unit is equipped with an electronic modulating gas valve which is controlled by a discharge sensor located in
the discharge opening. Check to see that the sensor is properly positioned. Set the selector dial for desired dis-
charge temperature - factory set at 70°.
5.
If 70° F discharge temperature is not desired, move appropriate discharge selector dial to new position and set
inlet air controller to a temperature at least 5° F below this setting. Note: No adjustment required on modulating
gas valve. High and low fire positions are factory set for proper operation. In some cases, it may be possible or
desirable to reduce the low fire: be sure to keep continuous flame the full length of burner.
6.
Check setting of inlet air controller. This is factory set at 65° F to shut down burner when outside temperature
rises above 65° F. If unit is to be test run when outside temperature is above 65° F, this setting will have to be
raised for burner to operate. After unit has been test run, reset controller at 65° F.
7.
Close gas hand valves and pilot cock.
8.
Set all switches to “Off” position.
- 8 -
Summary of Contents for DIRECT GAS FIRED ELECTRIC STEAM
Page 13: ...H VALVE ADJUSTMENTS 11 ...
Page 22: ... 20 ...
Page 23: ... 21 ...
Page 24: ... 22 ...
Page 25: ... 23 ...
Page 26: ... 24 ...
Page 27: ... 25 ...
Page 28: ... 26 ...
Page 29: ... 27 ...
Page 30: ... 28 ...
Page 31: ... 29 ...
Page 32: ... 30 ...
Page 33: ... 31 ...
Page 34: ... 32 ...
Page 35: ... 33 ...