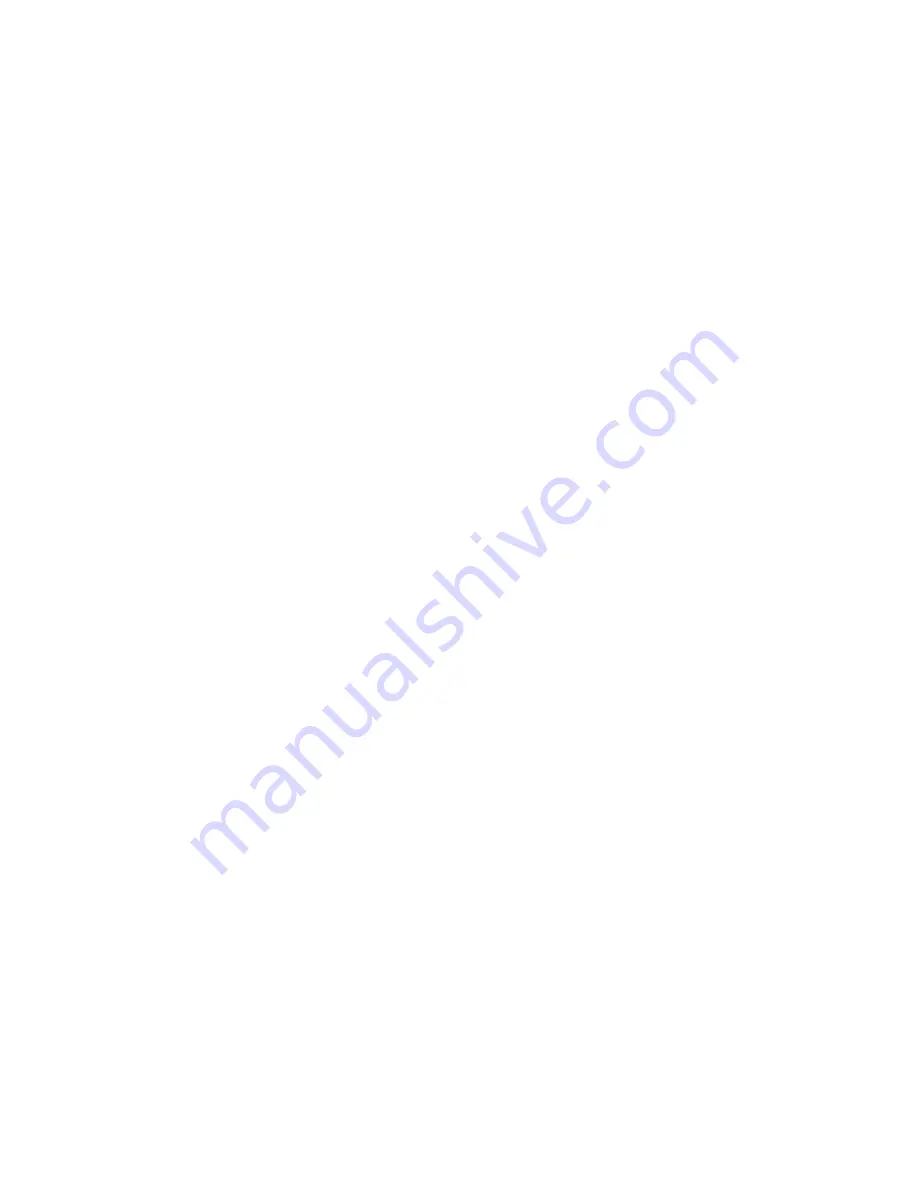
SECTION 2
E. INSTALLATION PROCEDURE
The following recommendations are not intended to supplant any requirements of federal, state, or local
codes having jurisdiction. This equipment shall be installed and wired in accordance with regulations of
the National board of Fire Underwriters, National Electric Code, and local governing bodies. In Canada,
equipment should be installed in accordance with the applicable provincial regulations.
1.
The units have been designed for rigging and handling through the units channel base frame and/or special lifting
lug hooks installed on the unit. All lifting operations must be accomplished with a load spreader of sufficient width
to insure that the lifting cables clear the side of the unit. If this type of spreader is not available, wood strips
should be inserted between the cables and unit where necessary. See Figure No. 1 and No. 2 in this manual.
Units are suspended from same lifting lugs as used for handling. See Figure No. 3 and Figure No. 4
To be properly set, the unit should be placed on a solid flat and level foundation and set exactly as detailed later
in the installation guide.
During the transit, unloading, and setting of the unit, bolts and nuts may have become loosened, particularly in the
pillow block ball bearing assemblies on blower section. It is recommended that all nuts and set screws be tight-
ened. Turn blower fan shaft by hand to make certain that no rubbing occurs and to check that bearing lock rings
are tight.
Open the cover on the electrical control box located at the top on the side of the burner section (blower section if
air handling unit only). Box can be opened by turning main fused disconnect switch to the “off” position
(disconnect is optional on air handling equipment). Inspect all wire terminals and wiring terminations to ensure
connections are tight. If unit is supplied with an electric heating section, check the separate electrical terminal box
for any loose connections.
2. Locating the Unit
Prior to locating the unit, authorities having jurisdiction should be consulted before installations are made. Ap-
proval permits should be checked against the unit received.
Locate the unit exactly level, making certain there is enough clearance for opening and removing access doors.
Special attention should be given to supply (if required) and discharge duct connections. Electrical power and
control hook-up points and steam or hot water supply and return lines (if required) should also be noted. This in-
formation should be cross-checked with the position of support beams and stand pipes to insure that support
structure dimensions coincide with those of the unit. Under structure beam spacing should also be checked to
preclude any interference with air ducts. Allow adequate clearance on both sides of unit for access to bearings,
motor, and all internal components. The heater inlet shall be located in accordance with the applicable building
code provisions for ventilation air.
Provide the following clearances:
Control Side - 48” (from unit mounted Main Control Panel)
Opposite Control Side - 12”
Top - 12”
Bottom - 12” (from combustibles)
Front - 36”
Rear - 36”
If main disconnect switch is shipped unmounted or provided by installer, a minimum clearance of 48” is required
and must be within sight of the unit.
3. Location of Accessories
The remote control panel will be located in the burner or electric section of the unit and must be removed and in-
stalled by the electrical contractor. Remote control panels for air handling units will be located in the blower sec-
tion for shipment. See remote control panel details in this bulletin. Field constructed intake accessories should be
properly designed to minimize the entry of snow and rain. Instructions should be given that adequate building
relief must be provided so as to not over pressurize the building when the heating system is operating at its rated
capacity. It should be noted that this can be accomplished by taking into account, through standard engineering
methods, the structure’s designed infiltration rate; by providing properly sized relief openings; or by interlocking a
powered exhaust system; or by a combination of these methods.
4. Electrical Connections
a. All wiring must comply with all applicable local, state, provincial, and national electric codes. Prior to running
power to the unit, visually inspect all nameplates, control voltage wiring, control transformer, and main fused
disconnect switch on the unit – cross check with bill of material to insure that the voltage option on the order is
the voltage option received.
Handling the Equipment
- 4 -
Summary of Contents for DIRECT GAS FIRED ELECTRIC STEAM
Page 13: ...H VALVE ADJUSTMENTS 11 ...
Page 22: ... 20 ...
Page 23: ... 21 ...
Page 24: ... 22 ...
Page 25: ... 23 ...
Page 26: ... 24 ...
Page 27: ... 25 ...
Page 28: ... 26 ...
Page 29: ... 27 ...
Page 30: ... 28 ...
Page 31: ... 29 ...
Page 32: ... 30 ...
Page 33: ... 31 ...
Page 34: ... 32 ...
Page 35: ... 33 ...