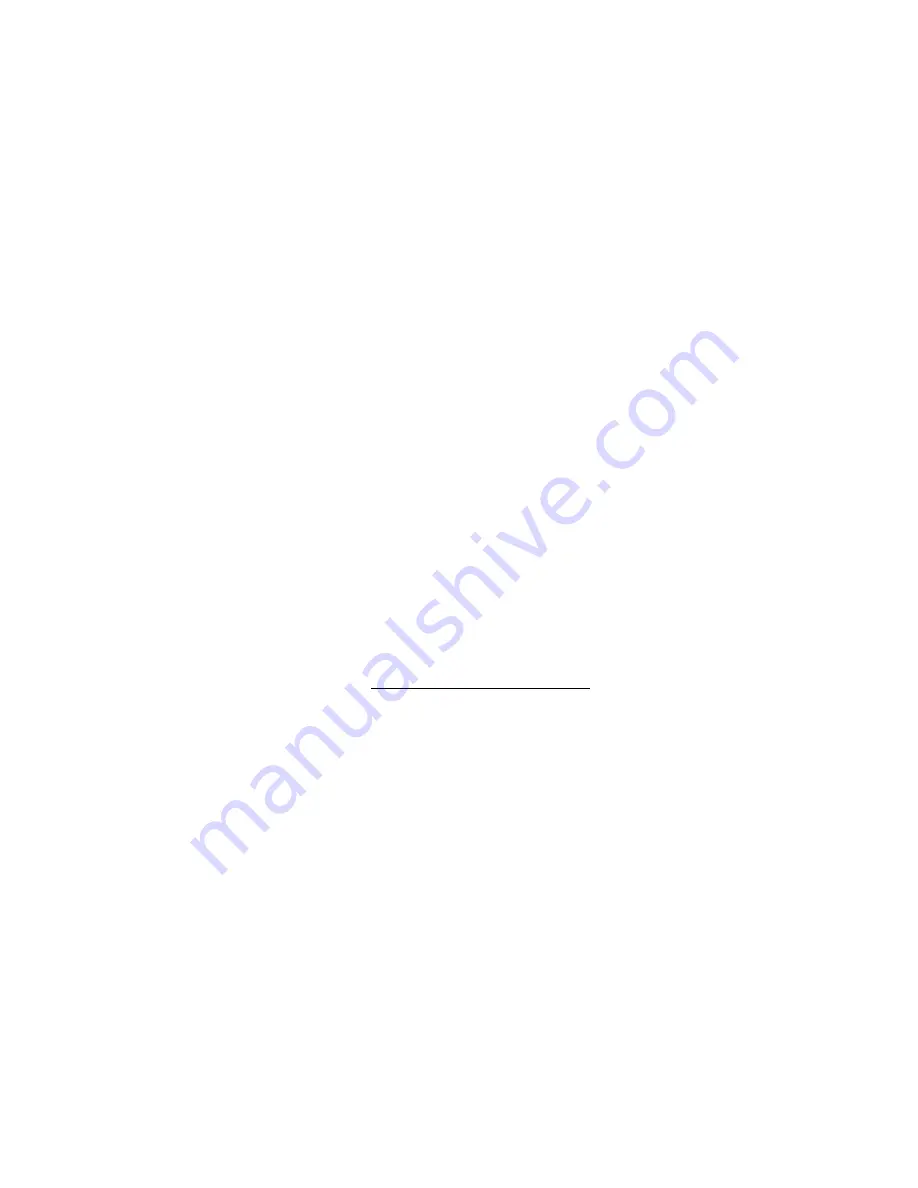
3.
Check all electrical connections in the main control panel.
4.
Check that all fuses are installed and that fuse sizing agrees with the unit bill of
material.
5.
Check to see if all gas, oil, or gas/oil connections are tight and that all joints have been
properly lubricated.
6.
Check positioning of flame rod (or photocell), spark electrodes, nozzles, cone, and
swirler. Make sure the combustion air fan is fastened securely to motor shaft.
7.
Check for cracks in refractory around the blast tube. This inspection requires close
observation with the aid of a good flashlight. Even a tiny crack can cause a positive
pressure within the combustion chamber and result in faulty burner operation.
8.
Check fan supply area to insure freedom of shaft rotation and proper belt tension.
Check to see that blowers are tight on shaft and turn freely without rubbing the blower
housing. The motor and shaft should turn readily by hand pull of the belts. Properly
adjusted belts can be easily depressed about one inch. Make sure the fan shaft pillow
block bearings are tight.
9.
Check fan motor to insure that pulleys are secure and drive belts are tight.
10.
Check all areas for cleanliness.
SECTION IV. – START-UP
All safety and operating controls have been checked during the factory test period; however, it
is advisable to complete a similar check when first operating the unit. Before attempting any
service work, make sure all electrical switches and manual valves are closed.
A.
PROCEDURE
1.
Remove any shipping blocks from:
a.
Gas pressure switch(s) (if required) may have shipping screws. Remove screws if
supplied.
b.
Unit programming controller may be shipped with a paper shipping block. Remove
programmer cover and remove paper shipping block – reinstall cover and adjust
manual reset.
c.
The high limit should be set for 200
°
F. The fan control should be set at 120
°
F on
high and 90
°
F on low. Note that fan operation is intermittent.
-16-
Summary of Contents for COUNTERFLO CF SERIES
Page 2: ......
Page 14: ... 11 ...
Page 15: ...Figure 6 Typical Light Oil Piping Suction System Two Pipe Method 12 ...
Page 18: ... 15 ...
Page 22: ... 19 ...
Page 25: ... 22 ...
Page 31: ... 28 ...