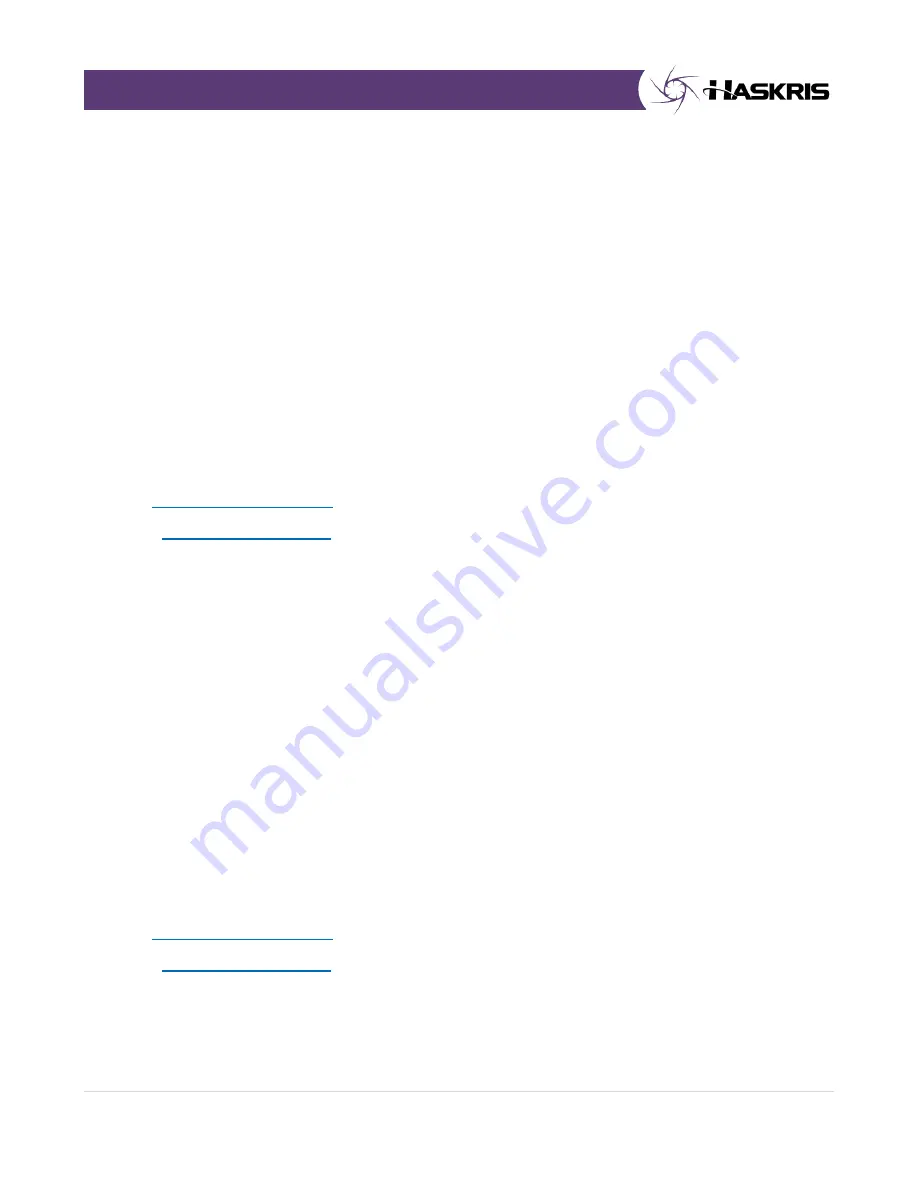
1 |
P a g e
1.0 PRELIMINARY INFORMATION
1.1 Installation Support (HMSA)
If at any time you have questions, encounter
problems or require technical support during
installation of your Haskris system, please
contact HMSA by any of the following
means:
Have the Product serial number available
when you call. The serial number can be
found on the panel near the
unit’s supply
and return connection and or on the lid of
the main electrical enclosure. Having the
serial number enables us to address
problems quickly and effectively.
Phone: 800-800-4925
Fax: 330-963-0749
Email:
Website:
www.hitachimed.com
The website contains information addressing
frequently asked questions, trouble shooting
guides and technical documentation.
1.2 Service Support (HMSA)
Contact HMSA if at any time you have
questions, encounter problems or
need spare parts for your Haskris
system.
Phone: 800-800-4925
Fax: 330-963-0749
Email:
Website:
www.hitachimed.com
The website contains information addressing
frequently asked questions, trouble shooting
guides and technical documentation.
Summary of Contents for OPC 12
Page 7: ...4 P a g e 2 0 INSTALLATION 2 2 System Location Continued ...
Page 8: ...5 P a g e 2 0 INSTALLATION ...
Page 15: ...12 P a g e 2 0 INSTALLATION ...
Page 26: ...23 P a g e 6 0 WARRANTY 5 0 MAINTENANCE ...
Page 27: ...24 P a g e 6 0 WARRANTY 5 0 MAINTENANCE ...
Page 28: ...25 P a g e 6 0 WARRANTY 5 0 MAINTENANCE ...
Page 29: ...26 P a g e 6 0 WARRANTY 5 0 MAINTENANCE ...
Page 30: ...27 P a g e 6 0 WARRANTY 5 0 MAINTENANCE ...
Page 32: ...29 P a g e 6 0 WARRANTY 5 0 MAINTENANCE ...
Page 33: ...30 P a g e 6 0 WARRANTY 5 0 MAINTENANCE 6 1 Standard Product Warranty 6 0 WARRANTY ...
Page 35: ...32 P a g e 6 0 WARRANTY 7 0 ELECTRICAL AND PIPING DIAGRAMS ...
Page 36: ...33 P a g e 6 0 WARRANTY 7 0 ELECTRICAL AND PIPING DIAGRAMS ...