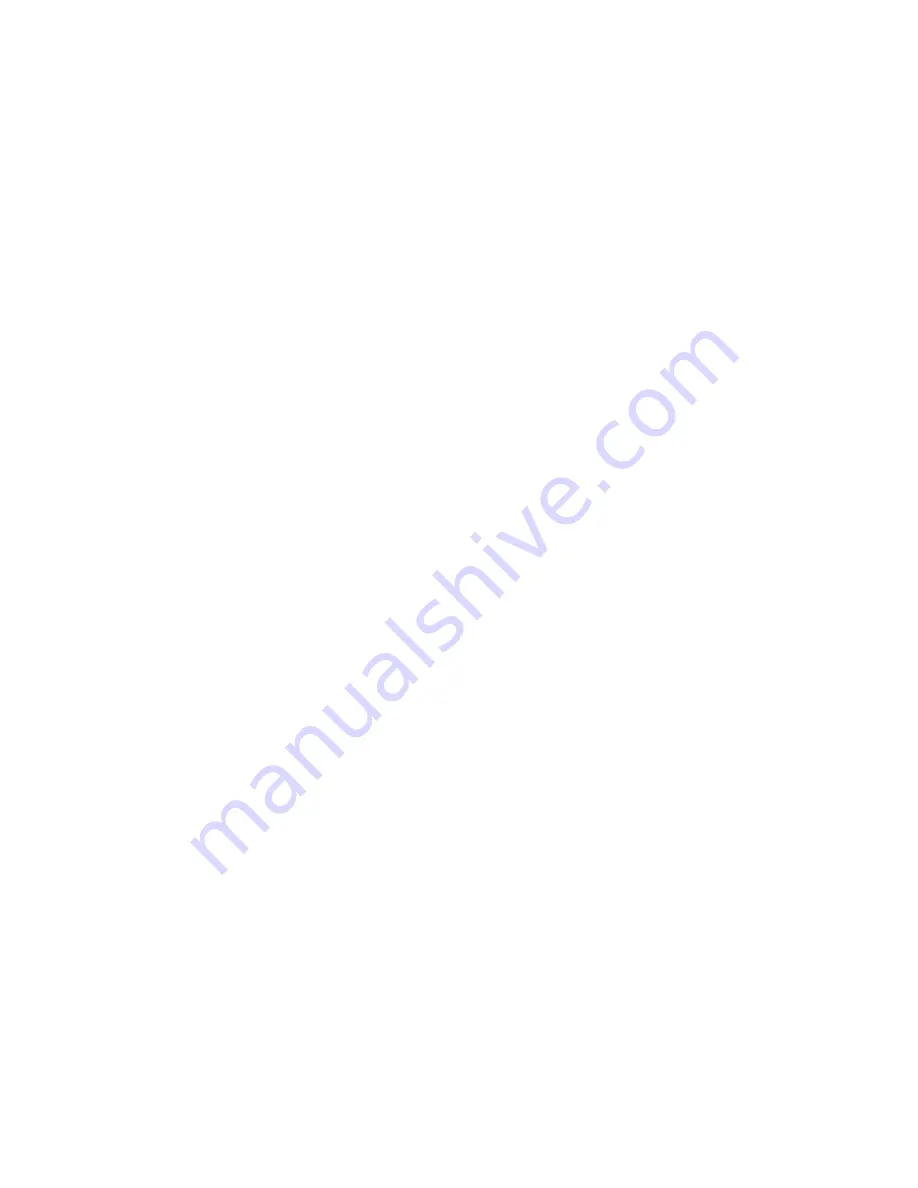
22
On start the signal will activate the flue
venter for a pre purge period and in turn will
make the air proving switch, once made, the
air proving switch will complete the circuit to
the control box and after a
40 second Delay
the automatic control should attempt light
the burner, because the gas is turned off
and flame cannot be established , the
control box will go to
LOCKOUT.
k) Reset the control on completion of dry
run.
l) Open gas cock.
m) Operate heater through installed control.
The flue venter will pre purge the heater and
in turn operate an air proving switch which
completes the electrical circuit to the control
box after a
40 second Delay
the control will
open the gas solenoid valve and the main
burner will light.
The flame can be observed at the burner
manifold, check that the burner is providing
a good flame i.e. even and stable.
n) Check pressure readings on the
manometers, and continue to let the heater
fire for ten minutes.
o) When the fan starts ensure that the
direction of rotation is correct , and that the
fan start is within 2 minutes of burner
ignition.
Caution
If the fan fails to operate within
approximately 2 minutes and the heater
goes to overheat it will shut down through
breaking the circuit to the gas valve, the
cause must be ascertained and rectified
before re-ignition.
Once the limit thermostat has tripped out it
must be manually reset to allow re-ignition
to take place.
p) After ten minutes check burner head
pressure is as specification - adjust as
necessary by removal of the gas pressure
adjustment cover, and using a screwdriver
turn the adjustment screw on the governor
as follows: Clockwise to increase. Anti
clockwise to decrease.
q) Check that the gas pressure remains
satisfactory for all appliances on the same
circuit.
r) Undertake combustion tests checking CO
CO
2
and efficiency (see section 7.0) CO
should not exceed (20PPM).
s) Check that the burners are extinguished
when the thermostat is set to its lowest
setting, and then remove the manometers.
t) Turn the thermostat to its highest setting
to re light the burner and replace the
adjustment screw cover.
On completion mark the gas valve
adjustment screw with paint/sealant to
prevent tampering with valve
u) Turn the thermostat to its lowest setting
and shut off the gas supply at the gas
control valve, allow the fan to continue to
run until the heater is cooled sufficiently for
the fan to shut down.
v) Turn off the electrical supply.
w) Close the side panel.
x) Set thermostat to desired setting.
y) Ensure that the user is familiar with the
heater and its controls and that the user is
satisfied with the commissioning and
testing, and that he is aware of the
instructions within the manual.
It is strongly advised that the commissioning
engineer runs through the lighting,
shutdown, and general safe and efficient
running of the heater before hand over.
On Completion of commissioning the fan
belts should checked for the correct
tension
3.4 Hand over
Up on sa tisf act ory co mp let ion of
commissioning and testing, a record of
commissioning information (contact name
date etc) should be made in the log book left
with the heater by the commissioning
engineer together with the user instructions.
At the same time the user should be made
aware of the most efficient and economical
methods of operation.
The user
must
be familiar and satisfied with
the safety, ignition, shutdown, and general
operational procedures.
Summary of Contents for HT2000
Page 51: ...51 Notes...