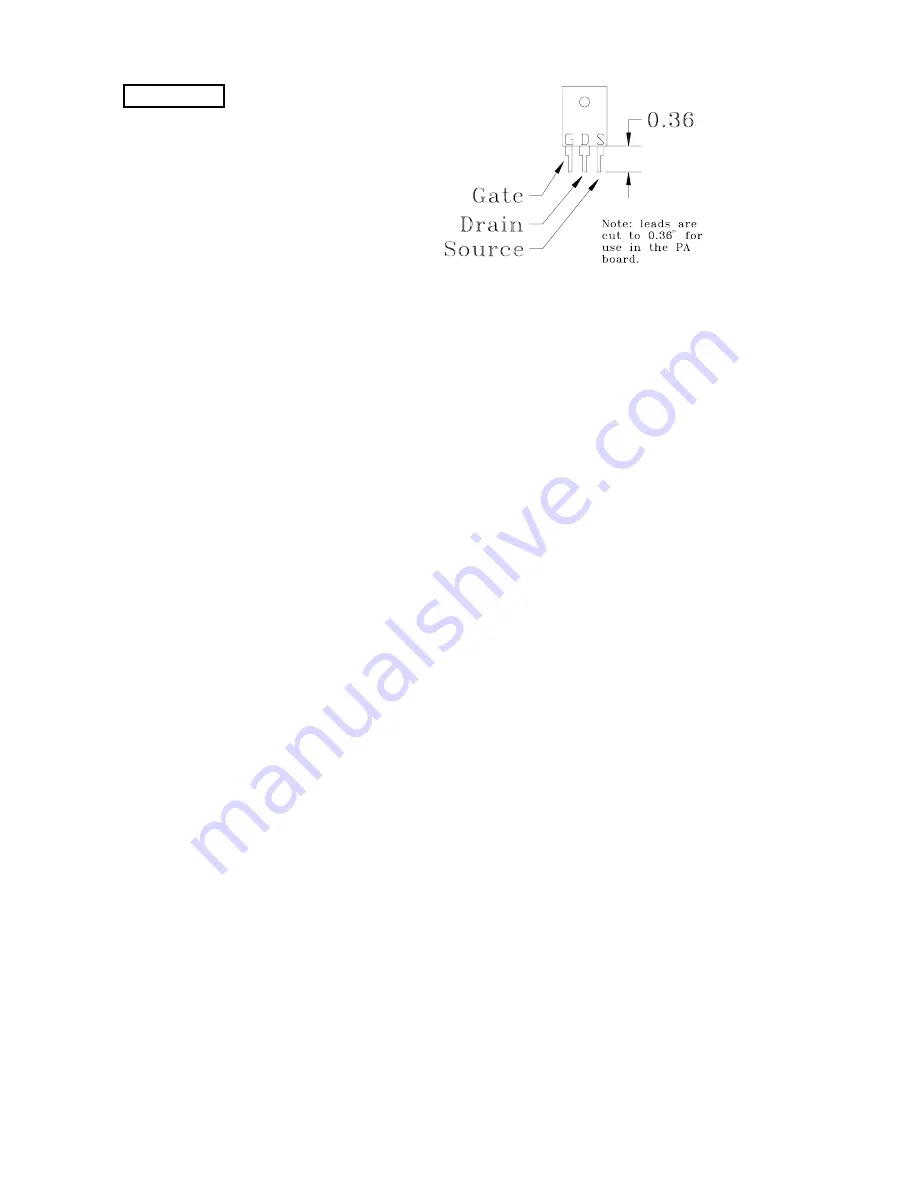
WARNING
NEVER ATTEMPT TO OPERATE THE
TRANSMITTER WITH ANY PA TRANSIS-
TORS REMOVED. IF REPLACEMENTS
ARE NOT AVAILABLE, IT IS NECESSARY
TO LEAVE THE SHORTED ONES IN CIR-
CUIT. THIS WILL KEEP THE TOROIDAL
COMBINING IN TACT, AND WILL NOT IM-
PAIR OPERATION OF THE TRANSMITTER
AT A REDUCED POWER LEVEL.
C.5.
Handling MOSFET’s
Due to the fragile nature of the gate of a
MOSFET, special care in their handling is
required. The gate can be destroyed by an
electrostatic discharge. Please read the en-
closed Technical Brief discussing safe han-
dling of transistors and integrated circuits.
Among other aspects of ESD control, this
publication covers the use of conductive
packaging and antistatic wrist bands.
NOTE
MOSFET transistors which are in circuit
in the GATES Series™ transmitters are
immune to this damage.
The MOSFET transistors are shipped in
antistatic packaging. The transistors should
remain in this packaging until they are to be
used or tested.
C.6.
Testing MOSFET’s
The MOSFETS used in the GATES Se-
ries™ transmitters may be checked with an
ohmmeter. However there is a requirement
which restricts the use of some ohmmeters.
If the battery voltage is too low (under 3V)
or too high (over 20V) the ohmmeter cannot
be used. A battery voltage less than 3V will
not give an operational check of the transis-
tor and a battery voltage greater than 20V
may result in damage to the transistor under
test. A Simpson 260, which uses a 9V bat-
tery on the Rx10k scale works quite well.
The following test applies to all MOS-
FETS used in the transmitter, but is not
necessarily applicable to MOSFETS used
in other equipment.
This test will show how a MOSFET can
be switched “on” and “off” by charging and
discharging the gate of the MOSFET.
Refer to Figure C-1 for the following test.
Connect the positive lead of the ohmmeter
to the source of the transistor. Momentarily
connect the negative lead to the gate and
then connect it to the source. Then connect
the positive lead to the drain (middle lead).
The ohmmeter should read at least 2 me-
gohms.
Remove the positive lead from the drain
and momentarily touch it to the gate. Re-
connect the positive lead to the drain. The
ohmmeter should read very near zero ohms.
C.6.1.
Replacing PA Transistors
Although there is no adhesive used in
attaching the transistors, you may find that
they remain in place after the mounting
screw is removed, and the terminals are
loosened. However, the transistors should
easily pop loose if you apply some leverage
to the transistor case. One way to do this is
to insert the shaft of a small screwdriver into
the mounting hole, then gently pry with the
screwdriver.
When installing new transistors, trim the
lead length so that the leads extend well into
the terminal blocks, but not so far as to bear
against the back end. A length of 0.36"
works well.
Tighten the transistor mounting screw
first, to no more than 5 inch-pounds.
Tighten the terminal block screws only after
the mounting screw has been tightened.
C.7.
Scoping the RF Drive
Measuring the RF drive with a scope can
be very meaningful in terms of identifying
blown transistors or a general RF drive
problem.
A failed PA transistor will usually cause
the RF drive level for that particular pair of
transistors to drop to a very low value. For
this reason, checking the drive levels on the
PA module(s) can help to readily identify
shorted transistors.
If a large number of PA transistors were to
short, it would possibly load down the entire
drive system. This will cause all of the PA
inputs to be somewhat low in drive, but the
inputs with shorted transistors would be
very low in drive.
NOTE
Insure that the REMOTE/LOCAL switch
located on the Controller board is in the
LOCAL position before performing the
checks outlined below. When the switch
is in the REMOTE position, RF Drive
and PDM are muted until the high volt-
age is turned on. After performing these
checks, set the switch back in the RE-
MOTE position.
It is usually advisable to check the RF
drive amplitude on the module before turn-
ing on the high voltage. It is not usually
necessary to readjust the IPA tuning.
RF Drive level is measured on the PA
modules with an oscilloscope. Place the
oscilloscope probe across R13 or the
equivalent terminal of any PA module. The
probe tip connects to the side closest to the
PA transistors.
Attach the probe ground lead to the RF
drive ground plane, which is the end of R13
furthest from the transistors. Do not use the
cabinet or chassis ground as this will give
an incorrect waveform. Proper drive level
should be 26-32 volts peak to peak on all
eight inputs of each PA module A1, A2, A3,
and A4, with the high voltage OFF.
C.8.
RF Drive Phasing Measurement
NOTE
Ensure that the REMOTE/LOCAL switch
located on the Controller board is set to
the LOCAL position before performing
the checks outlined below.
The RF drive phasing measurement may
be useful in locating some problems which
may be obscure to other means of trou-
bleshooting. Repeated failures of a particu-
lar PA transistor set might be caused by a
large drive phasing imbalance. Drive phase
imbalance could also reduce PA efficiency.
Measurements of the RF drive are made
with the transmitter in the OFF mode, but
the low voltage supply should be energized.
This is the usual condition when the trans-
mitter is ready to be turned on.
For the following procedure, an oscillo-
scope which can be externally triggered will
be required. This will allow examination of
the phase relationship between drive signals
on the PA.
Connect an oscilloscope across R13 posi-
tion on a PA module, with the probe tip on
the end of R13 closest to the transistors.
(Depending on the frequency of the trans-
mitter R13 may or may not be installed,
Figure C-1. Outline of MOSFET
C-2
888-2314-001
Rev. AE: 03-05-2002
WARNING: Disconnect primary power prior to servicing.
Summary of Contents for Gates Five 994 9204 002
Page 4: ......
Page 6: ...iv 888 2314 001 Rev X WARNING Disconnect primary power prior to servicing...
Page 8: ...vi 888 2314 001 Rev X WARNING Disconnect primary power prior to servicing...
Page 28: ...2 12 888 2314 001 Rev AC 2 29 00 WARNING Disconnect primary power prior to servicing...
Page 76: ...C 6 888 2314 001 Rev AE 03 05 2002 WARNING Disconnect primary power prior to servicing...
Page 82: ...E 4 888 2314 001 Rev AE 03 05 2002 WARNING Disconnect primary power prior to servicing...
Page 88: ...F 6 888 2314 001 Rev AE 03 05 2002 WARNING Disconnect primary power prior to servicing...
Page 96: ...H 2 888 2314 001 Rev AA 8 18 1999 WARNING Disconnect primary power prior to servicing...
Page 104: ...K 2 888 2314 001 Rev AE 03 05 2002 WARNING Disconnect primary power prior to servicing...
Page 108: ...L 2 888 2314 001 WARNING Disconnect primary power prior to servicing...