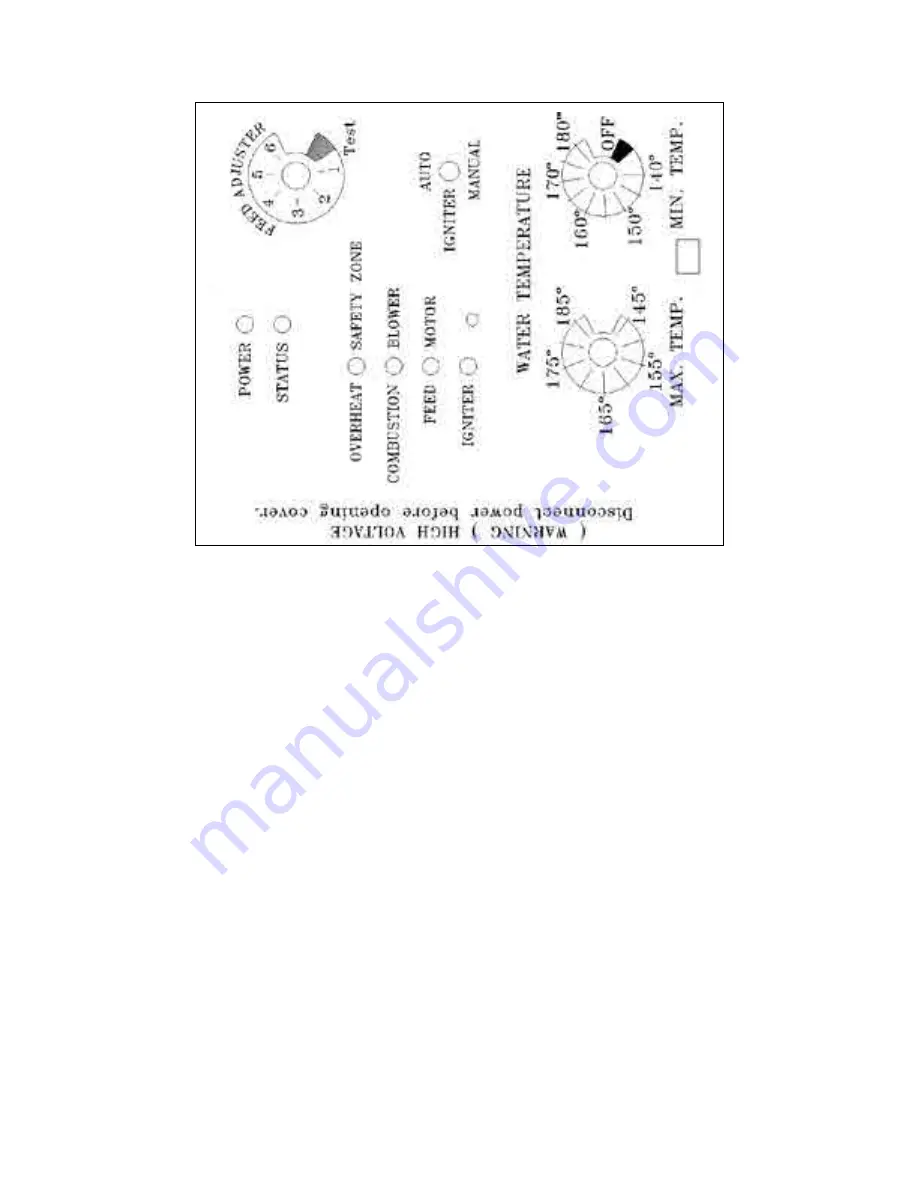
Quick
r
eference (
Auto-
light )
1.
T
urn
m
ode Selector to OFF
.
2.
Scrape the air holes in the burnpot.**
3.
Fill the hopper with pellets.
4.
T
urn Feed
Adjuster to “T
est”.*
5.
Check the Combustion Blower and Feeder Motor for operation.*
6.
T
urn Feed
Adjuster back to the #4, or previously known setting.
7.
T
urn the
m
A
x TE
m
P dial to the desired temperature.
8.
T
urn MIN TEMP
dial to the desired settings.*
9.
Flip the igniter switch to
Auto.*
The boiler will ignite if the temperature of the boiler water is less than the temperature set on
m
A
x TE
m
P dial..
*See the section on Operation for information about Manual Lighting and
Emergency Power
.
**See the section on Maintenance for more details about cleaning.